The production process of straight seam welded pipe is relatively simple. The main production processes are electric resistance welded straight seam steel pipe (ERW pipe) and submerged arc welded straight seam steel pipe (LSAW pipe). Straight seam pipe has high production efficiency, low cost and rapid development.
The strength of galvanized spiral welded pipe is generally higher than that of straight seam welded pipe, and the main production process is submerged arc welding.Spiral steel pipe (SSAW pipe) can use the same width billet to produce welded pipes with different diameters, and can also use narrower billets to produce welded pipes with larger diameters. But compared with the straight seam pipe of the same length, the weld length is increased by 30~100%, and the production speed is lower. Therefore, most of the welded pipes with smaller diameters adopt straight seam welding, and most of the large diameter welded pipes adopt spiral welding.
welding process
In terms of welding process, the welding method of galvanized spiral welded pipe is the same as that of galvanized straight seam steel pipe, but the straight seam welded pipe will inevitably have many T-shaped welds. Therefore, the probability of welding defects is also greatly increased, and the welding residual stress at the T-shaped weld is relatively large, and the weld metal is often in a three-dimensional stress state, which increases the possibility of cracks.
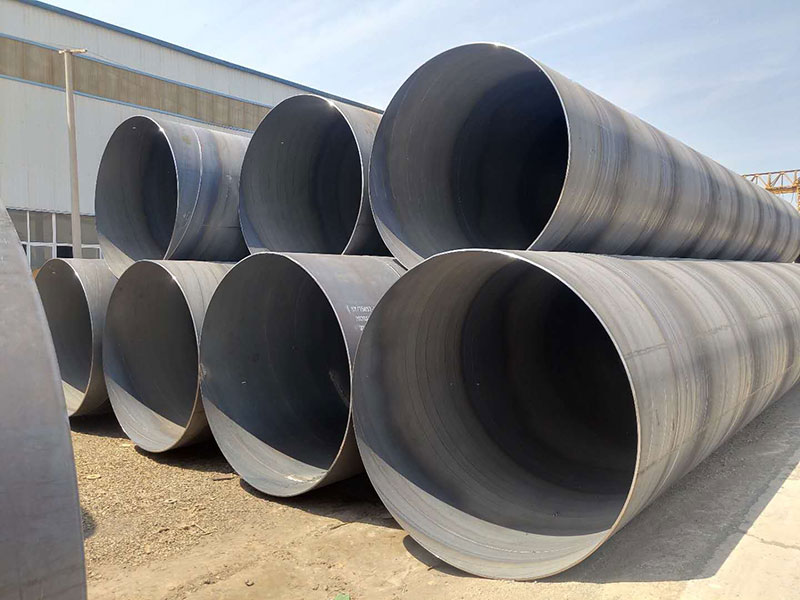
Static pressure burst strength
Through relevant comparative tests, it is verified that the yield pressure of the spiral welded pipe and the longitudinal seam welded pipe are basically consistent with the measured and theoretical values of the burst pressure, and the deviation is close. But whether it is yield pressure or burst pressure, the spiral welded pipe is lower than the straight seam welded pipe. The blasting test also shows that the circumferential deformation rate of the spiral welded pipe blasting opening is significantly greater than that of the straight seam welded pipe. This proves that the plastic deformation ability of the spiral welded pipe is better than that of the straight seam welded pipe, and the blasting opening is generally limited to one pitch, which is due to the strong restraint effect of the spiral weld on the expansion of the crack.
Toughness and fatigue strength
The trend of pipeline development is large diameter and high strength. With the increase of the diameter of the steel pipe and the improvement of the steel grade used, the tendency of the ductile fracture tip to expand steadily is greater. According to the tests of relevant research institutions, although the spiral welded pipe and the straight seam welded pipe are of the same level, the spiral welded pipe has higher impact toughness.
The strength of galvanized spiral welded pipe is generally higher than that of straight seam welded pipe, and the main production process is submerged arc welding.Spiral steel pipe (SSAW pipe) can use the same width billet to produce welded pipes with different diameters, and can also use narrower billets to produce welded pipes with larger diameters. But compared with the straight seam pipe of the same length, the weld length is increased by 30~100%, and the production speed is lower. Therefore, most of the welded pipes with smaller diameters adopt straight seam welding, and most of the large diameter welded pipes adopt spiral welding.
welding process
In terms of welding process, the welding method of galvanized spiral welded pipe is the same as that of galvanized straight seam steel pipe, but the straight seam welded pipe will inevitably have many T-shaped welds. Therefore, the probability of welding defects is also greatly increased, and the welding residual stress at the T-shaped weld is relatively large, and the weld metal is often in a three-dimensional stress state, which increases the possibility of cracks.
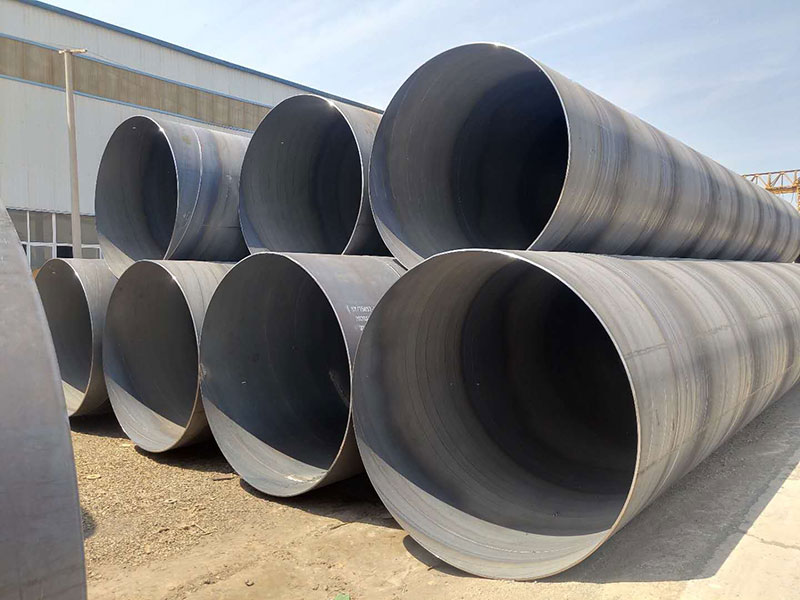
Static pressure burst strength
Through relevant comparative tests, it is verified that the yield pressure of the spiral welded pipe and the longitudinal seam welded pipe are basically consistent with the measured and theoretical values of the burst pressure, and the deviation is close. But whether it is yield pressure or burst pressure, the spiral welded pipe is lower than the straight seam welded pipe. The blasting test also shows that the circumferential deformation rate of the spiral welded pipe blasting opening is significantly greater than that of the straight seam welded pipe. This proves that the plastic deformation ability of the spiral welded pipe is better than that of the straight seam welded pipe, and the blasting opening is generally limited to one pitch, which is due to the strong restraint effect of the spiral weld on the expansion of the crack.
Toughness and fatigue strength
The trend of pipeline development is large diameter and high strength. With the increase of the diameter of the steel pipe and the improvement of the steel grade used, the tendency of the ductile fracture tip to expand steadily is greater. According to the tests of relevant research institutions, although the spiral welded pipe and the straight seam welded pipe are of the same level, the spiral welded pipe has higher impact toughness.
Previous:ASTM A519 gr 4130
Next:ERW pipe mill line