Non-destructive testing is a method of uating internal defects or performance status of an object through inspection technology without damaging the object being tested. Conventional non-destructive testing methods refer to five basic testing methods that are widely used in the engineering field, namely ultrasonic testing, radiographic testing, eddy current testing, magnetic particle testing and penetrant testing. This article will introduce these five conventional non-destructive testing methods for ERW pipe in detail.
Five major non-destructive testing methods for ERW pipe
1. Ultrasonic testing
Ultrasonic testing uses the propagation characteristics of ultrasonic waves within the object to be tested to detect defects or performance status of the object. By emitting ultrasonic pulses, the internal structure and defects of the object being measured are judged based on the difference in propagation speed of ultrasonic waves in different media and phenomena such as reflection, refraction, and scattering. Ultrasonic testing is widely used in defect detection and structural uation of metals, composite materials, ceramics, concrete and other materials.
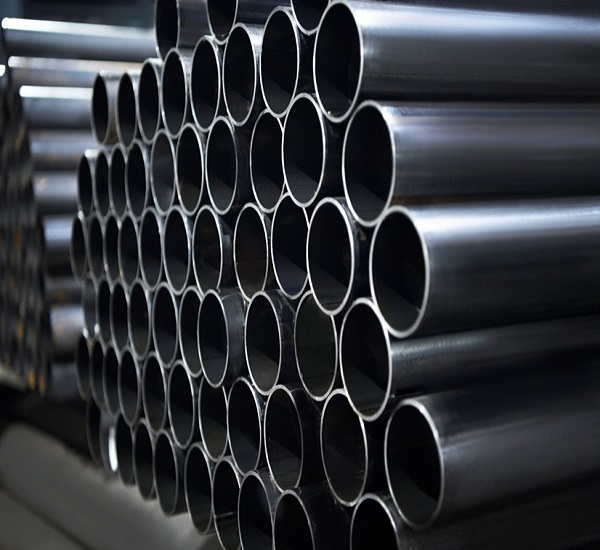
2. Radiographic detection
Ray detection uses rays (such as X-rays or γ-rays) to penetrate the object being tested, and detect defects or performance status of the object through the absorption, scattering and other phenomena of the rays. Radiographic inspection is commonly used for defect detection and quality assessment of metals, welded parts, pipes, containers and other materials. Radiographic testing has the characteristics of strong penetrating power and high sensitivity, and can detect tiny defects. However, it also has radiation safety issues and requires special protective measures.
3. Eddy current testing
Eddy current testing uses the principle of eddy current induction to detect defects or performance status of objects. By applying an alternating current to the surface of the object to be measured, eddy currents are generated, and the internal defects of the object to be measured are judged based on changes in the eddy currents. Eddy current testing is widely used in defect detection and surface quality assessment of metal materials, and can detect surface cracks, corrosion, pores and other defects.
4. Magnetic particle testing
Magnetic particle testing uses the principle that magnetic particles gather at defects on the surface of the object to be tested under the action of a magnetic field to detect defects or performance status of the object. By applying a magnetic field to the surface of the object to be measured, the magnetic powder causes magnetic field anomalies at the defects, and the defects of the object to be measured are judged by observing the aggregation of the magnetic particles. Magnetic particle testing is widely used in crack detection of metal materials and quality assessment of welded joints.
5. Penetration testing
Penetrant testing uses the permeability of liquids to detect defects or performance status of objects. By applying penetrant on the surface of the object to be tested, after it penetrates into the defect, the remaining penetrant on the surface is removed, and a developer is applied, and the defects of the object being tested are judged by observing the color developer seeping out at the defect. Condition. Penetrant testing is widely used in surface defect detection and quality assessment of metals, ceramics, plastics and other materials.
What is the purpose of non-destructive testing of ERW pipe?
(1) Quality management.
The performance and quality level of each product are usually clearly specified in its technical documents, such as technical conditions, specifications, acceptance standards, etc., which are characterized by certain technical quality indicators. One of the main purposes of non-destructive testing is to provide real-time quality control for ERW pipes that are non-continuously processed (such as multi-process production) or continuously processed (such as automated production lines), such as controlling the metallurgical quality, processing technology quality, and organization of ERW pipes. status, thickness of coating, size, orientation and distribution of defects, etc.
(2) In-service inspection.
Using non-destructive testing technology to monitor devices or components during operation, or conducting regular inspections during the maintenance period, we can promptly discover hidden dangers that affect the continued safe operation of ERW pipes or components and prevent accidents.
(3) Quality identification.
Before ERW pipe finished products (including materials and parts) are assembled or put into use, final inspection should be carried out, which is called quality appraisal. Its purpose is to determine whether the inspected object reaches the design performance and can be used safely, that is, whether it is qualified. This is not only an acceptance of the previous processing steps, but also can avoid hidden dangers in future use. Apply non-destructive testing technology in each (or one or several) process of casting, forging, welding, heat treatment and cutting to detect whether the ERW pipe meets the requirements to avoid continued futile processing of unqualified products.
Five major non-destructive testing methods for ERW pipe
1. Ultrasonic testing
Ultrasonic testing uses the propagation characteristics of ultrasonic waves within the object to be tested to detect defects or performance status of the object. By emitting ultrasonic pulses, the internal structure and defects of the object being measured are judged based on the difference in propagation speed of ultrasonic waves in different media and phenomena such as reflection, refraction, and scattering. Ultrasonic testing is widely used in defect detection and structural uation of metals, composite materials, ceramics, concrete and other materials.
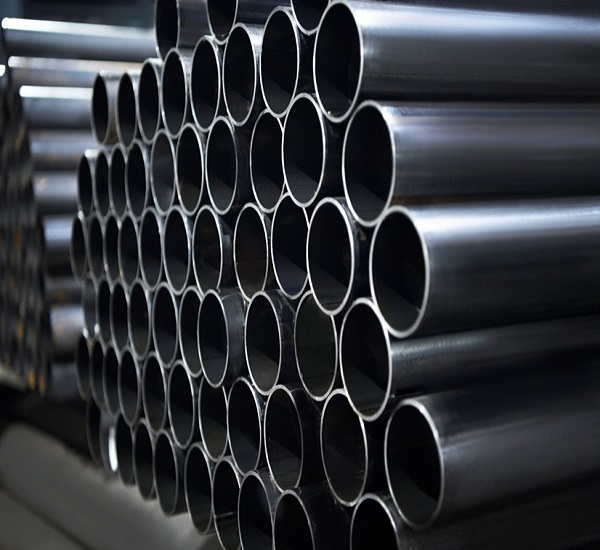
2. Radiographic detection
Ray detection uses rays (such as X-rays or γ-rays) to penetrate the object being tested, and detect defects or performance status of the object through the absorption, scattering and other phenomena of the rays. Radiographic inspection is commonly used for defect detection and quality assessment of metals, welded parts, pipes, containers and other materials. Radiographic testing has the characteristics of strong penetrating power and high sensitivity, and can detect tiny defects. However, it also has radiation safety issues and requires special protective measures.
3. Eddy current testing
Eddy current testing uses the principle of eddy current induction to detect defects or performance status of objects. By applying an alternating current to the surface of the object to be measured, eddy currents are generated, and the internal defects of the object to be measured are judged based on changes in the eddy currents. Eddy current testing is widely used in defect detection and surface quality assessment of metal materials, and can detect surface cracks, corrosion, pores and other defects.
4. Magnetic particle testing
Magnetic particle testing uses the principle that magnetic particles gather at defects on the surface of the object to be tested under the action of a magnetic field to detect defects or performance status of the object. By applying a magnetic field to the surface of the object to be measured, the magnetic powder causes magnetic field anomalies at the defects, and the defects of the object to be measured are judged by observing the aggregation of the magnetic particles. Magnetic particle testing is widely used in crack detection of metal materials and quality assessment of welded joints.
5. Penetration testing
Penetrant testing uses the permeability of liquids to detect defects or performance status of objects. By applying penetrant on the surface of the object to be tested, after it penetrates into the defect, the remaining penetrant on the surface is removed, and a developer is applied, and the defects of the object being tested are judged by observing the color developer seeping out at the defect. Condition. Penetrant testing is widely used in surface defect detection and quality assessment of metals, ceramics, plastics and other materials.
What is the purpose of non-destructive testing of ERW pipe?
(1) Quality management.
The performance and quality level of each product are usually clearly specified in its technical documents, such as technical conditions, specifications, acceptance standards, etc., which are characterized by certain technical quality indicators. One of the main purposes of non-destructive testing is to provide real-time quality control for ERW pipes that are non-continuously processed (such as multi-process production) or continuously processed (such as automated production lines), such as controlling the metallurgical quality, processing technology quality, and organization of ERW pipes. status, thickness of coating, size, orientation and distribution of defects, etc.
(2) In-service inspection.
Using non-destructive testing technology to monitor devices or components during operation, or conducting regular inspections during the maintenance period, we can promptly discover hidden dangers that affect the continued safe operation of ERW pipes or components and prevent accidents.
(3) Quality identification.
Before ERW pipe finished products (including materials and parts) are assembled or put into use, final inspection should be carried out, which is called quality appraisal. Its purpose is to determine whether the inspected object reaches the design performance and can be used safely, that is, whether it is qualified. This is not only an acceptance of the previous processing steps, but also can avoid hidden dangers in future use. Apply non-destructive testing technology in each (or one or several) process of casting, forging, welding, heat treatment and cutting to detect whether the ERW pipe meets the requirements to avoid continued futile processing of unqualified products.