Plastic-coated composite steel pipe is also called plastic-coated steel pipe. Plastic-coated steel pipe is a steel-plastic composite product with steel pipe as the base pipe, plastic powder as the coating material, a plastic layer on the inner surface, and a plastic layer or other anti-corrosion layer on the outer surface. .
The middle of the plastic-coated composite steel pipe is a composite structure of reinforced welded steel tube or seamless pipe. It overcomes the defects of easy rust, corrosion, high pollution, low strength and easy deformation of plastic pipes in the steel pipe itself, integrates the common advantages of steel pipes and plastic products, and is an environmentally friendly product promoted and used by the country.
Plastic-coated composite steel pipe is a steel-plastic composite pipe composed of a layer of organic matter with a thickness of 0.5 ~ 1.0mm melted on the inner wall of the steel pipe. It not only has the advantages of high strength, easy connection, and water shock resistance of steel pipes, but also overcomes the shortcomings of steel pipes such as easy corrosion, pollution, scaling, low strength of plastic pipes, and poor fire performance. The design life can reach 50 years. The main disadvantage is that it is not allowed to bend during installation, and when performing operations such as thermal processing and electric welding and cutting, the cutting surface should be painted with non-toxic room temperature curing glue provided by the manufacturer.
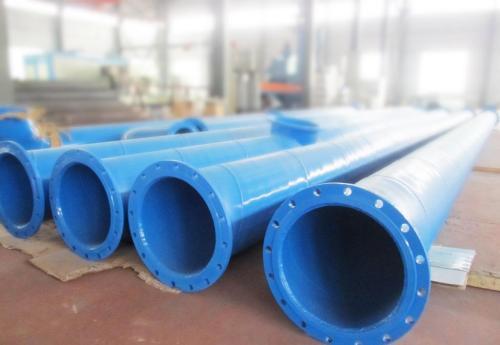
Appearance requirements for plastic-coated composite steel pipes
1. The coating layer should be smooth and flat, free from scratches, cracks, pinholes and adhesion of foreign matter and other defects.
2. The outer coating of the steel pipe should be red (fire-fighting), black or gray (water delivery).
3. There should be a clear and durable mark on the coated steel pipe, and the content of the mark should at least include: product model, base pipe specification and wall thickness, implementation standard, manufacturer's name or trademark, production date or batch number, etc.
Introduction to the production process of plastic-coated composite steel pipe
Plastic-coated composite steel pipes are divided into: hot-dipping process, internal and external spraying process, rotational molding process, shower coating process, suction coating process, fusion winding process, etc.
1. Hot dipping method: fluidized bed dipping, one-time film forming method. Also known as the first generation of anti-corrosion plastic coated steel pipe, polyethylene inside and outside.
2. Internal and external spraying process: Using electrostatic adsorption theory, through pre-treatment of steel pipes, spray polyethylene or epoxy resin powder with a spray gun. Also known as the second-generation anti-corrosion plastic-coated steel pipe, epoxy composite steel pipe inside and outside.
3. Flow coating process: also known as the curtain method, through the sieve filled with powder, it is coated on the outer wall of the heated steel pipe by means of flow coating. This process can produce outer polyethylene inner epoxy composite steel pipe. Also known as the third-generation anti-corrosion of plastic-coated steel pipes.
4. Fusion winding process:
Using the thermal fusion winding method, the hot melt adhesive and polyethylene are wound on the heated steel pipe in the form of an extruder, and react to form a three-layer structure. The full name is fusion bonded epoxy/extruded polyethylene structural protective layer. This process can produce outer three-layer polyethylene inner fusion bonded epoxy composite steel pipe. Also known as the fourth generation of anti-corrosion plastic coated steel pipe
The middle of the plastic-coated composite steel pipe is a composite structure of reinforced welded steel tube or seamless pipe. It overcomes the defects of easy rust, corrosion, high pollution, low strength and easy deformation of plastic pipes in the steel pipe itself, integrates the common advantages of steel pipes and plastic products, and is an environmentally friendly product promoted and used by the country.
Plastic-coated composite steel pipe is a steel-plastic composite pipe composed of a layer of organic matter with a thickness of 0.5 ~ 1.0mm melted on the inner wall of the steel pipe. It not only has the advantages of high strength, easy connection, and water shock resistance of steel pipes, but also overcomes the shortcomings of steel pipes such as easy corrosion, pollution, scaling, low strength of plastic pipes, and poor fire performance. The design life can reach 50 years. The main disadvantage is that it is not allowed to bend during installation, and when performing operations such as thermal processing and electric welding and cutting, the cutting surface should be painted with non-toxic room temperature curing glue provided by the manufacturer.
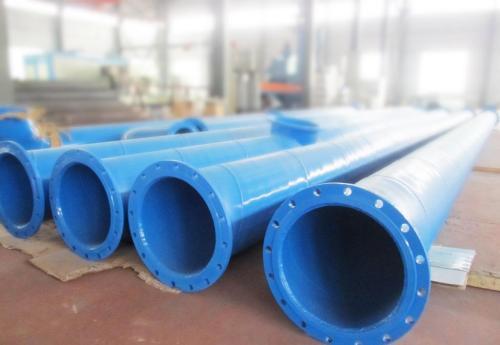
Appearance requirements for plastic-coated composite steel pipes
1. The coating layer should be smooth and flat, free from scratches, cracks, pinholes and adhesion of foreign matter and other defects.
2. The outer coating of the steel pipe should be red (fire-fighting), black or gray (water delivery).
3. There should be a clear and durable mark on the coated steel pipe, and the content of the mark should at least include: product model, base pipe specification and wall thickness, implementation standard, manufacturer's name or trademark, production date or batch number, etc.
Introduction to the production process of plastic-coated composite steel pipe
Plastic-coated composite steel pipes are divided into: hot-dipping process, internal and external spraying process, rotational molding process, shower coating process, suction coating process, fusion winding process, etc.
1. Hot dipping method: fluidized bed dipping, one-time film forming method. Also known as the first generation of anti-corrosion plastic coated steel pipe, polyethylene inside and outside.
2. Internal and external spraying process: Using electrostatic adsorption theory, through pre-treatment of steel pipes, spray polyethylene or epoxy resin powder with a spray gun. Also known as the second-generation anti-corrosion plastic-coated steel pipe, epoxy composite steel pipe inside and outside.
3. Flow coating process: also known as the curtain method, through the sieve filled with powder, it is coated on the outer wall of the heated steel pipe by means of flow coating. This process can produce outer polyethylene inner epoxy composite steel pipe. Also known as the third-generation anti-corrosion of plastic-coated steel pipes.
4. Fusion winding process:
Using the thermal fusion winding method, the hot melt adhesive and polyethylene are wound on the heated steel pipe in the form of an extruder, and react to form a three-layer structure. The full name is fusion bonded epoxy/extruded polyethylene structural protective layer. This process can produce outer three-layer polyethylene inner fusion bonded epoxy composite steel pipe. Also known as the fourth generation of anti-corrosion plastic coated steel pipe
Previous:Round steel