Galvanized steel pipe has the dual advantages of strong corrosion resistance and low price, and its usage rate is getting higher and higher. However, in some cases, it is necessary to weld the galvanized pipe. How to ensure the quality of welding?
1. The weld seam must be ground before welding. The galvanized layer at the weld must be ground off, otherwise air bubbles, trachoma, false welding, etc. will occur. It will also make the weld brittle and reduce the rigidity.
2. Introduction of welding techniques: When welding the first layer of weld seam in multi-layer welding, try to melt the zinc layer and make it vaporize, evaporate and escape the weld seam, which can greatly reduce the liquid zinc remaining in the weld seam. When welding fillet welds, also try to melt the zinc layer on the first layer and make it vaporize, evaporate and escape the weld. The method is to move the end of the electrode forward about 5~7mm, and then return to the original position to continue welding forward after the zinc layer is melted. For horizontal welding and vertical welding, if short slag electrodes such as J427 are used, the tendency of undercutting will be small; if the back-and-forth forward and backward transport technology is used, defect-free welding quality can be obtained.
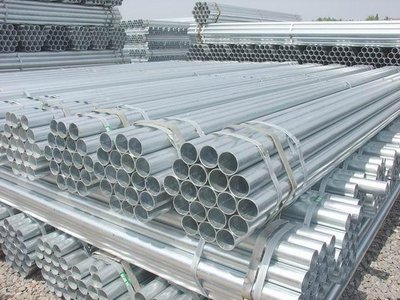
3. Analysis of welding characteristics of galvanized steel.
Galvanized steel is generally coated with a layer of zinc on the outside of low carbon steel, and the galvanized layer is generally 20um thick. Zinc has a melting point of 419°C and a boiling point of around 908°C. During welding, zinc melts into a liquid that floats on the surface of the molten pool or at the root of the weld. Zinc has a large solid solubility in iron, and zinc liquid will erode the weld metal deeply along the grain boundary, and zinc with a low melting point will form "liquid metal embrittlement".
At the same time, zinc and iron can form intermetallic brittle compounds, and these brittle phases reduce the plasticity of the weld metal and cause cracks under the action of tensile stress. If the fillet welds are welded, especially the fillet welds of T-joints, penetration cracks are most likely to occur. When galvanized steel is welded, the zinc layer on the groove surface and the edge will be oxidized, melted, evaporated and white smoke and steam will be volatilized under the action of arc heat, which will easily cause weld pores.
4. How to control the galvanized steel welding process?
The pre-welding preparation of galvanized steel is the same as that of ordinary low-carbon steel. It should be noted that the groove size and the nearby galvanized layer should be carefully handled. For penetration, the groove size should be appropriate, generally 60~65°, and a certain gap should be left, generally 1.5~2.5mm. In order to reduce the penetration of zinc into the weld, before welding, the galvanized layer in the groove can be removed before welding.
In the actual supervision work, centralized beveling, no blunt edge process is adopted for centralized control, and the two-layer welding process reduces the possibility of incomplete penetration. The welding rod should be selected according to the base material of the galvanized pipe.
1. The weld seam must be ground before welding. The galvanized layer at the weld must be ground off, otherwise air bubbles, trachoma, false welding, etc. will occur. It will also make the weld brittle and reduce the rigidity.
2. Introduction of welding techniques: When welding the first layer of weld seam in multi-layer welding, try to melt the zinc layer and make it vaporize, evaporate and escape the weld seam, which can greatly reduce the liquid zinc remaining in the weld seam. When welding fillet welds, also try to melt the zinc layer on the first layer and make it vaporize, evaporate and escape the weld. The method is to move the end of the electrode forward about 5~7mm, and then return to the original position to continue welding forward after the zinc layer is melted. For horizontal welding and vertical welding, if short slag electrodes such as J427 are used, the tendency of undercutting will be small; if the back-and-forth forward and backward transport technology is used, defect-free welding quality can be obtained.
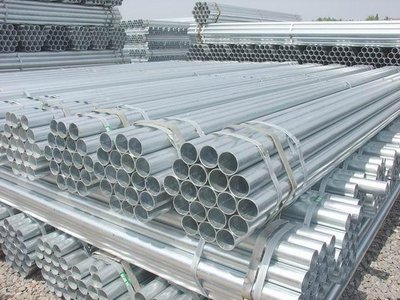
3. Analysis of welding characteristics of galvanized steel.
Galvanized steel is generally coated with a layer of zinc on the outside of low carbon steel, and the galvanized layer is generally 20um thick. Zinc has a melting point of 419°C and a boiling point of around 908°C. During welding, zinc melts into a liquid that floats on the surface of the molten pool or at the root of the weld. Zinc has a large solid solubility in iron, and zinc liquid will erode the weld metal deeply along the grain boundary, and zinc with a low melting point will form "liquid metal embrittlement".
At the same time, zinc and iron can form intermetallic brittle compounds, and these brittle phases reduce the plasticity of the weld metal and cause cracks under the action of tensile stress. If the fillet welds are welded, especially the fillet welds of T-joints, penetration cracks are most likely to occur. When galvanized steel is welded, the zinc layer on the groove surface and the edge will be oxidized, melted, evaporated and white smoke and steam will be volatilized under the action of arc heat, which will easily cause weld pores.
4. How to control the galvanized steel welding process?
The pre-welding preparation of galvanized steel is the same as that of ordinary low-carbon steel. It should be noted that the groove size and the nearby galvanized layer should be carefully handled. For penetration, the groove size should be appropriate, generally 60~65°, and a certain gap should be left, generally 1.5~2.5mm. In order to reduce the penetration of zinc into the weld, before welding, the galvanized layer in the groove can be removed before welding.
In the actual supervision work, centralized beveling, no blunt edge process is adopted for centralized control, and the two-layer welding process reduces the possibility of incomplete penetration. The welding rod should be selected according to the base material of the galvanized pipe.