Spiral steel pipe (SSAW) is a spiral seam steel pipe made of strip steel coil as raw material, extruded at regular temperature, and welded by automatic double-wire double-sided submerged arc welding process.
During the welding process of spiral steel pipe, there are many factors that affect welding. It is necessary to adjust the forming and welding height while adjusting the spatial dynamic welding curve. If the adjustment is proper, the occurrence of thermal cracks can be avoided and the welding quality of the welded pipe can be guaranteed.
The molding should be adjusted and controlled from the following aspects:
1. It is necessary to ensure that the calculation of the molding process parameters is accurate, and the exact position is properly adjusted when it is released;
2. Fine-tuning to control the deformation of the strip when forming is sufficient to reduce the curvature difference on the discharge side of the free edge
3. Correctly adjust the height of the backing roller during welding to avoid excessive local stress at the meshing point.
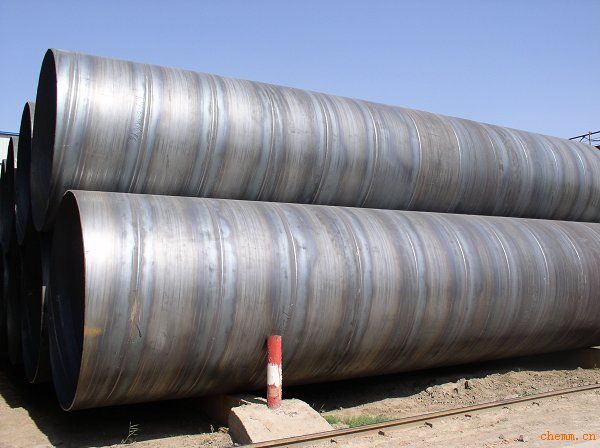
Control welding factors:
1. The welded pipe that cannot be used in the welding position actually has welding when welding uphill and downhill, because the welding spot itself in the spiral submerged arc welded pipe is not the main deformation zone. If uphill welding is used, the deformation of the welded pipe is seriously insufficient at this time, and the weld seam inside the welded pipe is most likely to be torn.
2. The joint cannot be too far from the center. Because it is so far from the center, it mushrooms when welded, and the saddle is taller than shown. Such a shape is not conducive to the discharge of impurities in the weld pool (induction of slag cracks), stress and poor health.
3. Under the premise of ensuring the amount of overlap, the parameters in the welding specification are not too large. For twin-wire welding, the distance between the welding wires is not too large, if it is too large or the distance between the specification parameters is too large, it will prolong the length of the molten pool. During the pre-processing of the pipe, it is inevitable that it will be affected by vibration, push, pull and other forces, and the probability of the increase in the pattern of the bath is slightly flat.
During the welding process of spiral steel pipe, there are many factors that affect welding. It is necessary to adjust the forming and welding height while adjusting the spatial dynamic welding curve. If the adjustment is proper, the occurrence of thermal cracks can be avoided and the welding quality of the welded pipe can be guaranteed.
The molding should be adjusted and controlled from the following aspects:
1. It is necessary to ensure that the calculation of the molding process parameters is accurate, and the exact position is properly adjusted when it is released;
2. Fine-tuning to control the deformation of the strip when forming is sufficient to reduce the curvature difference on the discharge side of the free edge
3. Correctly adjust the height of the backing roller during welding to avoid excessive local stress at the meshing point.
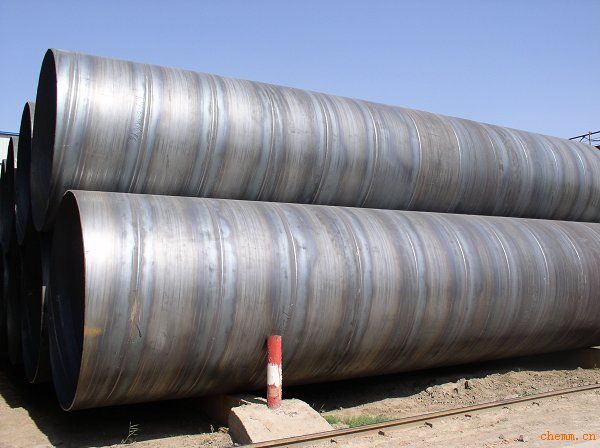
Control welding factors:
1. The welded pipe that cannot be used in the welding position actually has welding when welding uphill and downhill, because the welding spot itself in the spiral submerged arc welded pipe is not the main deformation zone. If uphill welding is used, the deformation of the welded pipe is seriously insufficient at this time, and the weld seam inside the welded pipe is most likely to be torn.
2. The joint cannot be too far from the center. Because it is so far from the center, it mushrooms when welded, and the saddle is taller than shown. Such a shape is not conducive to the discharge of impurities in the weld pool (induction of slag cracks), stress and poor health.
3. Under the premise of ensuring the amount of overlap, the parameters in the welding specification are not too large. For twin-wire welding, the distance between the welding wires is not too large, if it is too large or the distance between the specification parameters is too large, it will prolong the length of the molten pool. During the pre-processing of the pipe, it is inevitable that it will be affected by vibration, push, pull and other forces, and the probability of the increase in the pattern of the bath is slightly flat.