Thermally expanded seamless steel pipe is a steel pipe (seamless pipe) with low density but strong shrinkage. The waste pipe finishing rolling process that expands the pipe diameter by cross rolling or drawing method. The outer diameter of the steel pipe can be expanded in a relatively short period of time, and non-standard special specifications and special-shaped seamless steel pipes can be produced. The advantages are low cost and high production efficiency. This is the current development trend in the field of pipe rolling in the world.
There are two methods of hot-rolled pipe expansion: longitudinal rolling and oblique rolling. The quality defects of longitudinal rolling and expanding pipes mainly include surface cracks and cracks of the pipe body, uneven wall thickness, internal straight roads, internal hemp pits, wrinkles and bends of empty pipes. The quality defects of cross-rolling and expanding pipes are basically the same as those of waste pipes rolled by two-roll cross-rolling mills. Including uneven wall thickness, surface cracks and abrasions, rolling folds, spiral road and spiral inner folds, inner hemp pits, etc. of waste pipes.
The deformation process of longitudinal rolling tube expansion includes drawing type and push type tube expansion process. Its deformation process is divided into three stages:
(1) Under the action of the conical surface of the plug, the tube wall of the blank tube first bends and deforms;
(2) With the gradual increase of the diameter of the plug, expand the diameter and reduce the wall of the tube blank;
(3) Calibrate and straighten the expanded pipe from the cylindrical section of the plug. Clearly, diameter expansion mainly occurs in the second stage.
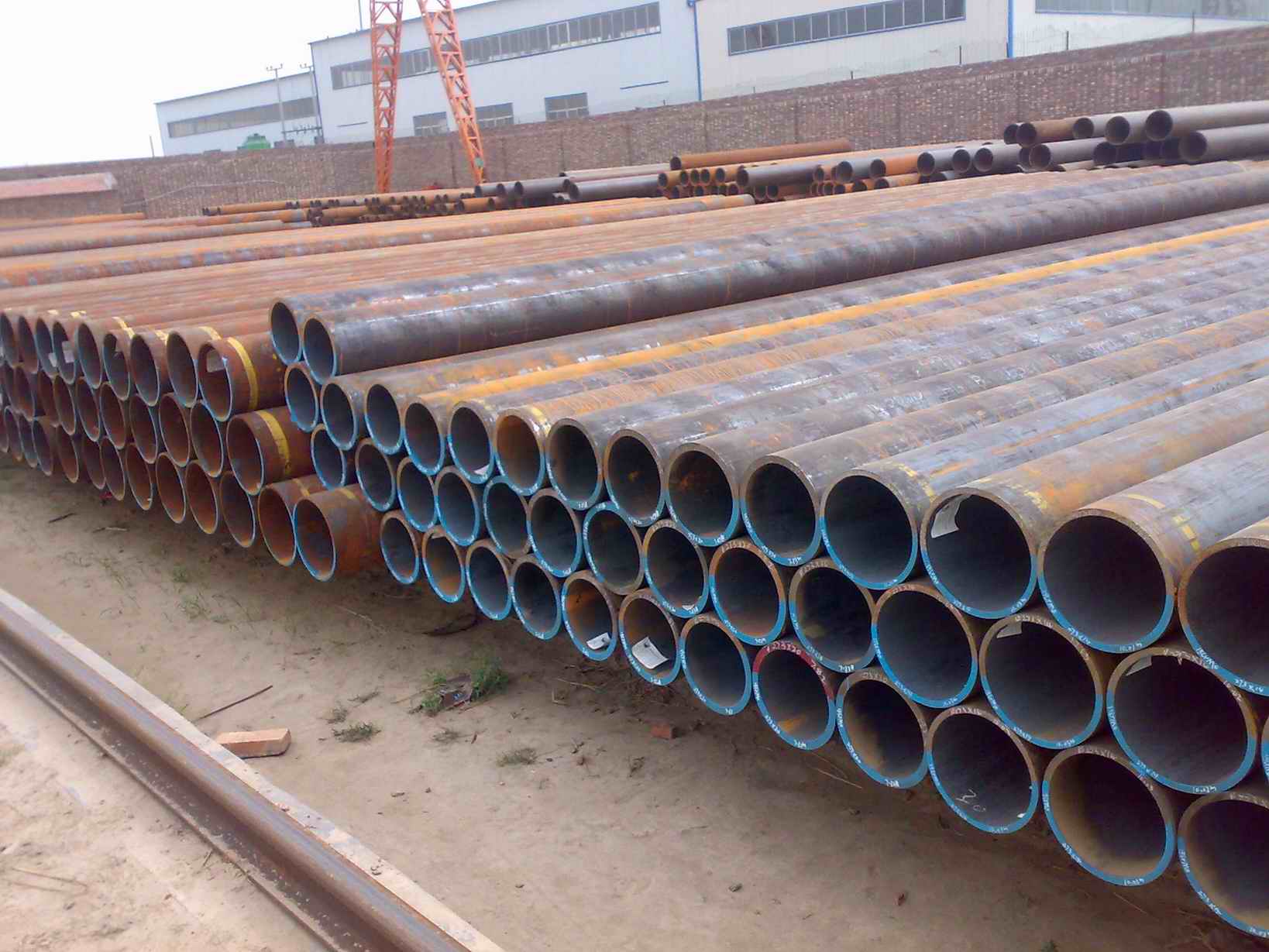
The cross-rolling pipe expansion process originated from the secondary piercing process. It is a skew rolling mill with two tapered rolls arranged horizontally. The diameter of the roll increases gradually from the entrance to the exit of the deformation zone. The roll axis and the rolling line intersect in space, forming the feeding angle and rolling angle. The two rollers are single-supported and driven by two motors separately, and the transmission mechanism is located at the exit side of the pipe rolling mill. The position of the rolls can be adjusted along the axis of the rolling line. The guide plates are arranged up and down. The deformation zone is divided into three parts: the flattening and reducing zone, the reducing zone and the rounding zone.
Due to the increase of raw material defects caused by the pipe expansion process, it is specially required that the steel pipe used for pipe expansion must meet the following requirements:
(1) All pipe materials are fed after eddy current testing.
(2) There are no defects such as hairlines and folds on the outer surface. There are no defects such as delamination on the inner surface.
(3) There are no burrs on the end face of the steel pipe, and the verticality requires that the end face cut slope is ≤1mm.
(4) The diameter tolerance of the steel pipe is controlled at ≤±0.8%
(5) The wall thickness tolerance of the steel pipe is controlled at ≤±10%
(6) The inner spiral of the steel pipe is ≤0.3mm, and there is no visible spiral path
(7) When expanding the pipe, the hot-rolled tail end is used as the front end of the expanded pipe, and the length of the cut end of the hot-rolled steel pipe must be guaranteed.
There are two methods of hot-rolled pipe expansion: longitudinal rolling and oblique rolling. The quality defects of longitudinal rolling and expanding pipes mainly include surface cracks and cracks of the pipe body, uneven wall thickness, internal straight roads, internal hemp pits, wrinkles and bends of empty pipes. The quality defects of cross-rolling and expanding pipes are basically the same as those of waste pipes rolled by two-roll cross-rolling mills. Including uneven wall thickness, surface cracks and abrasions, rolling folds, spiral road and spiral inner folds, inner hemp pits, etc. of waste pipes.
The deformation process of longitudinal rolling tube expansion includes drawing type and push type tube expansion process. Its deformation process is divided into three stages:
(1) Under the action of the conical surface of the plug, the tube wall of the blank tube first bends and deforms;
(2) With the gradual increase of the diameter of the plug, expand the diameter and reduce the wall of the tube blank;
(3) Calibrate and straighten the expanded pipe from the cylindrical section of the plug. Clearly, diameter expansion mainly occurs in the second stage.
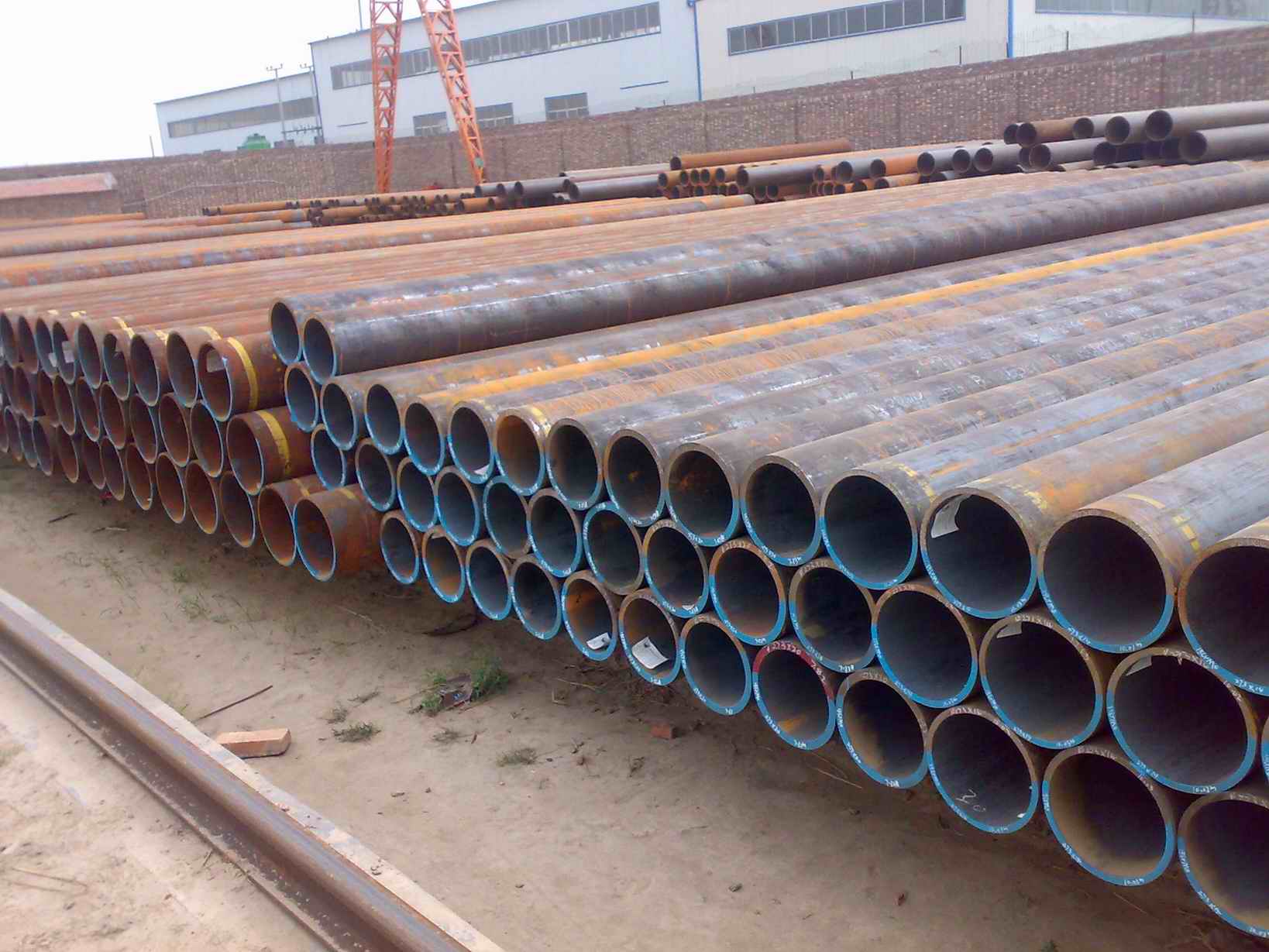
The cross-rolling pipe expansion process originated from the secondary piercing process. It is a skew rolling mill with two tapered rolls arranged horizontally. The diameter of the roll increases gradually from the entrance to the exit of the deformation zone. The roll axis and the rolling line intersect in space, forming the feeding angle and rolling angle. The two rollers are single-supported and driven by two motors separately, and the transmission mechanism is located at the exit side of the pipe rolling mill. The position of the rolls can be adjusted along the axis of the rolling line. The guide plates are arranged up and down. The deformation zone is divided into three parts: the flattening and reducing zone, the reducing zone and the rounding zone.
Due to the increase of raw material defects caused by the pipe expansion process, it is specially required that the steel pipe used for pipe expansion must meet the following requirements:
(1) All pipe materials are fed after eddy current testing.
(2) There are no defects such as hairlines and folds on the outer surface. There are no defects such as delamination on the inner surface.
(3) There are no burrs on the end face of the steel pipe, and the verticality requires that the end face cut slope is ≤1mm.
(4) The diameter tolerance of the steel pipe is controlled at ≤±0.8%
(5) The wall thickness tolerance of the steel pipe is controlled at ≤±10%
(6) The inner spiral of the steel pipe is ≤0.3mm, and there is no visible spiral path
(7) When expanding the pipe, the hot-rolled tail end is used as the front end of the expanded pipe, and the length of the cut end of the hot-rolled steel pipe must be guaranteed.