The manufacturing process of angle steel can be roughly divided into the following steps:
1. Raw material preparation: The main raw materials of angle steel are steel plates or billets. These raw materials need to undergo strict quality inspection to ensure that their chemical composition, mechanical properties and surface quality meet the production requirements.
2. Processing preparation: According to the specifications and size requirements of the angle steel, professional cutting equipment is used to cut the raw materials into appropriate sizes. The cut raw materials also need to be rust-free to remove surface oxides and impurities to improve the purity of the steel and the quality of subsequent processing.
3. Heating and pre-bending: The cut and rust-free raw materials are sent to the heating furnace and heated to the appropriate temperature to soften them and improve plasticity and machinability. After heating, the raw materials enter the pre-bending machine for pre-bending treatment, and initially present the shape of the angle steel.
4. Bending and shaping: The pre-bent raw materials enter the bending machine and are further bent into the standard shape of the angle steel through pressure and force. Depending on the specific needs of the product, multiple bending and shaping operations may be required to ensure that every angle and size of the angle steel meets the standard.
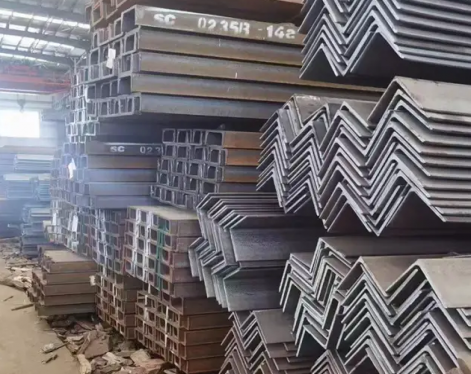
5. Cooling and straightening: The angle steel after bending and shaping has a high temperature and needs to be cooled quickly to fix its shape. Water cooling or air cooling is usually used to reduce the temperature. After cooling, the angle steel enters the straightening machine for straightening to eliminate possible bending and skewness and achieve ideal straightness.
6. Surface treatment: In order to improve the corrosion resistance and appearance quality of the angle steel, surface treatment is usually required. Common surface treatment methods include galvanizing, spraying and chrome plating. Galvanizing is one of the most common surface treatment methods. The zinc layer is evenly coated on the surface of the angle steel through the hot-dip galvanizing process to form a dense protective layer, which effectively prevents steel corrosion.
7. Inspection and quality control: The produced angle steel needs to undergo a strict inspection and quality control process, including appearance quality inspection, dimensional accuracy measurement, strength and hardness testing, etc., to ensure that the product meets the design requirements and quality standards.
8. Packaging: Pack the qualified angle steels for easy transportation and storage.
Common manufacturing methods of angle steel:
The production of angle steel is mainly carried out by hot rolling or cold bending.
Hot rolling is the main method for producing large-size angle steel. First, raw materials such as molten iron and scrap steel are put into a steelmaking furnace to melt into qualified molten steel, and then the molten steel is poured into a continuous casting machine to form a steel billet with a specific cross-section. After the billet is heated to the rolling temperature, it is put into the rolling mill for multiple rolling. The cross-sectional size is gradually reduced through repeated rolling until the angle steel with the desired cross-sectional shape is formed. The angle steel after rolling also needs to be straightened to eliminate stress and improve straightness. Finally, the finished angle steel is strictly inspected for quality, including size, surface quality and mechanical properties, to ensure that the product meets the standard requirements.
The cold bending process is suitable for the production of smaller-sized angle steel. In the cold bending process, the steel plate or steel strip is first pre-bent, and then gradually formed into an angle steel on the forming machine through steps such as rolling and bending. The cold bending process has high requirements for equipment and molds, and requires precise control of processing parameters to ensure the size and shape accuracy of the angle steel. Similarly, cold-bent angle steels also need to be quality tested to ensure product quality.
Whether it is hot rolling or cold bending, the production of angle steels requires strict control of the quality of raw materials and processing. High-quality raw materials and precise processing technology are the key to producing high-quality angle steels. In addition, heat treatment is also an important link in the production process of angle steels. Through heat treatment methods such as quenching and tempering, the strength and hardness of angle steels can be improved to meet the needs of different application scenarios.
In the production process of angle steels, attention should also be paid to environmental protection and safe production. For example, during the heat treatment process, exhaust gas emissions should be controlled to ensure that the production environment meets environmental protection requirements; during the processing process, operating procedures should be strictly followed to ensure the safety of personnel and equipment. At the same time, with the advancement of science and technology and the continuous optimization of processes, the production efficiency and product quality of angle steels will continue to improve.
1. Raw material preparation: The main raw materials of angle steel are steel plates or billets. These raw materials need to undergo strict quality inspection to ensure that their chemical composition, mechanical properties and surface quality meet the production requirements.
2. Processing preparation: According to the specifications and size requirements of the angle steel, professional cutting equipment is used to cut the raw materials into appropriate sizes. The cut raw materials also need to be rust-free to remove surface oxides and impurities to improve the purity of the steel and the quality of subsequent processing.
3. Heating and pre-bending: The cut and rust-free raw materials are sent to the heating furnace and heated to the appropriate temperature to soften them and improve plasticity and machinability. After heating, the raw materials enter the pre-bending machine for pre-bending treatment, and initially present the shape of the angle steel.
4. Bending and shaping: The pre-bent raw materials enter the bending machine and are further bent into the standard shape of the angle steel through pressure and force. Depending on the specific needs of the product, multiple bending and shaping operations may be required to ensure that every angle and size of the angle steel meets the standard.
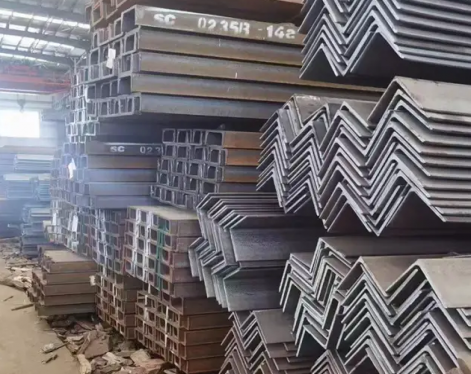
5. Cooling and straightening: The angle steel after bending and shaping has a high temperature and needs to be cooled quickly to fix its shape. Water cooling or air cooling is usually used to reduce the temperature. After cooling, the angle steel enters the straightening machine for straightening to eliminate possible bending and skewness and achieve ideal straightness.
6. Surface treatment: In order to improve the corrosion resistance and appearance quality of the angle steel, surface treatment is usually required. Common surface treatment methods include galvanizing, spraying and chrome plating. Galvanizing is one of the most common surface treatment methods. The zinc layer is evenly coated on the surface of the angle steel through the hot-dip galvanizing process to form a dense protective layer, which effectively prevents steel corrosion.
7. Inspection and quality control: The produced angle steel needs to undergo a strict inspection and quality control process, including appearance quality inspection, dimensional accuracy measurement, strength and hardness testing, etc., to ensure that the product meets the design requirements and quality standards.
8. Packaging: Pack the qualified angle steels for easy transportation and storage.
Common manufacturing methods of angle steel:
The production of angle steel is mainly carried out by hot rolling or cold bending.
Hot rolling is the main method for producing large-size angle steel. First, raw materials such as molten iron and scrap steel are put into a steelmaking furnace to melt into qualified molten steel, and then the molten steel is poured into a continuous casting machine to form a steel billet with a specific cross-section. After the billet is heated to the rolling temperature, it is put into the rolling mill for multiple rolling. The cross-sectional size is gradually reduced through repeated rolling until the angle steel with the desired cross-sectional shape is formed. The angle steel after rolling also needs to be straightened to eliminate stress and improve straightness. Finally, the finished angle steel is strictly inspected for quality, including size, surface quality and mechanical properties, to ensure that the product meets the standard requirements.
The cold bending process is suitable for the production of smaller-sized angle steel. In the cold bending process, the steel plate or steel strip is first pre-bent, and then gradually formed into an angle steel on the forming machine through steps such as rolling and bending. The cold bending process has high requirements for equipment and molds, and requires precise control of processing parameters to ensure the size and shape accuracy of the angle steel. Similarly, cold-bent angle steels also need to be quality tested to ensure product quality.
Whether it is hot rolling or cold bending, the production of angle steels requires strict control of the quality of raw materials and processing. High-quality raw materials and precise processing technology are the key to producing high-quality angle steels. In addition, heat treatment is also an important link in the production process of angle steels. Through heat treatment methods such as quenching and tempering, the strength and hardness of angle steels can be improved to meet the needs of different application scenarios.
In the production process of angle steels, attention should also be paid to environmental protection and safe production. For example, during the heat treatment process, exhaust gas emissions should be controlled to ensure that the production environment meets environmental protection requirements; during the processing process, operating procedures should be strictly followed to ensure the safety of personnel and equipment. At the same time, with the advancement of science and technology and the continuous optimization of processes, the production efficiency and product quality of angle steels will continue to improve.