1.Types of H-beam
Based on the requirements for use and the design characteristics of the cross-section, H-beam is generally divided into two main categories: one is H-beam steel used as a beam-type building component; the other is H-beam steel used as a column-type (or pile-type) building component. For beam-type components, the ratio of height to flange width is between 2:1 to 3:1, and the specifications generally range from 100mmx50mm to 900mmx300mm. For column-type components, the ratio of height to flange width is 1:1, and the specifications generally range from 100mmx100mm to 400mmx400mm. The height of H-beam steel ranges from 80 to 1100mm, the flange width from 46 to 454mm, the web thickness from 2.9 to 78mm, and the weight per meter from 6 to 1086kg.
2.Production technology of H section
The rolling methods of H-beam steel can be roughly divided into the following three categories in historical order:(1) Rolling method using ordinary two-roll or three-roll type steel mills;
(2) Rolling method using a universal mill;
(3) Rolling method using multiple sets of universal mills.
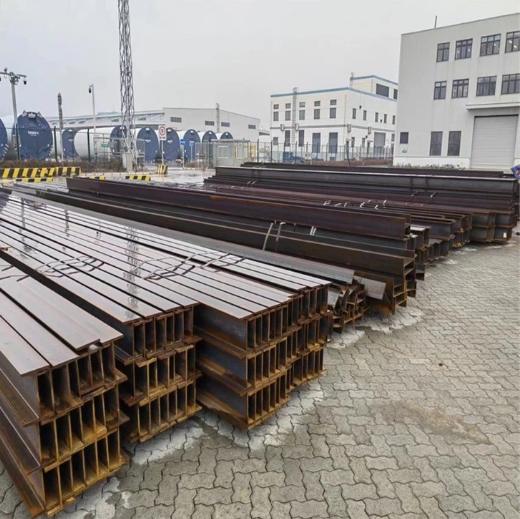
3.Modern production methods of H-beam
The rolling of H-beam steel with multiple sets of universal mills has been widely adopted worldwide, with specific methods including the Greiner method, the Saxby method, and the J. P. Poul method.(1) Greiner method
The main feature of the Greiner method is the use of an open universal pass design, where the web and flange are processed simultaneously in the open pass design. To effectively control the leg height and the quality of the leg processing, Greiner believes that the vertical pressure must act on the leg end, so the compression of the leg height is carried out in the two-roll mill stand that is connected to the universal mill stand. At present, most of the edge rolling mills in the world adopt the Greiner method.
The process of rolling H-beam steel using the Greiner method is roughly as follows: The steel ingot is rolled into a shaped billet by an initial rolling mill or a two-roll blooming mill, and then the shaped billet is sent to the universal rough rolling mill and edge rolling mill for back-and-forth continuous rolling, and then rolled into finished products on the universal finishing mill and edge rolling mill. When the Greiner method performs vertical pressing, only the horizontal rolls come into contact with the leg end of the rolled piece (the web does not come into contact with the horizontal rolls), which ensures that the leg end of the rolled piece remains straight. In this method, the vertical rolls are mostly cylindrical, and the sides of the horizontal rolls have a slight slope. In the rough rolling mill group, the side of the horizontal roll has an approximate slope of 9%. In the finishing mill group, the side of the horizontal roll has a slope of 2% to 5%, but the slope of the side of the horizontal roll in the finishing mill group should be as small as possible to roll out parallel legs.
In 1908, the Bethlehem Steel Corporation in the United States built a rolling mill using the above process, which consisted of a two-roll blooming mill and two universal mills spaced 90 meters apart. Each universal mill includes a universal stand and an edge rolling stand. Modern H-beam steel mills also widely adopt the Greiner method for design.
(2) Saxby method
The Saxby method uses a closed universal pass design, in which the legs are inclined. To finally roll out straight legs, a universal mill stand with cylindrical vertical rolls must be installed in the last pass. The vertical pressure of the Saxby method is different from the Greiner method; it applies pressure in the direction of the leg width, which is prone to cause the rolled piece to move, especially in the closed pass design, where the protruding part of the leg end is easily squeezed out to form ears, affecting the quality of the finished product.
In the rough rolling universal pass of the Saxby method, the side of the horizontal roll can adopt a larger slope, which can reduce the wear of the horizontal roll. At the same time, since the vertical roll is conical, it can simultaneously extend the web and legs with a large reduction ratio. This can reduce the number of rolling passes and the number of universal mill stands, which is conducive to saving equipment investment.
The main process of the Saxby method is: A two-roll blooming mill is used to roll the steel ingot into a billet with an I-shaped cross-section, and then the billet is sent to a reversible continuous rolling train composed of a four-roll universal mill stand and a two-roll vertical pressing mill stand for rough rolling, and finally rolled into finished products on a universal mill stand. The side of the horizontal roll in the rough rolling group has a slope of 8%, the side of the horizontal roll in the intermediate group has a slope of 4%, and only in the finishing universal mill stand is the leg of the I-beam rolled straight, with a finished I-beam leg slope of about 1.5%.
(3) J. P. Poul method
The J. P. Poul method combines the advantages of the Greiner method and the Saxby method, that is, it absorbs the Saxby method's inclined universal pass design to obtain a larger extension in one time and the Greiner method's use of vertical pressure pass design to facilitate the control of leg width processing. The main feature of the J. P. Poul method is that the rough rolling uses the Saxby method's inclined universal pass design, and the finishing rolling uses the Greiner method's open universal pass design. On the finishing universal rolling mill, the legs are first flattened with cylindrical vertical rolls and horizontal rolls, then the vertical rolls are lifted, and only the horizontal rolls are used to press the leg ends. Finally, on the second finishing universal mill, the rolled piece is fully processed with horizontal rolls and vertical rolls. The process is: A two-roll reversible blooming mill and two universal mill stands are used for rolling, with the horizontal rolls of the universal mill stand having a slope of 7%, and the conicity of the vertical rolls is also 7%. In the finishing universal mill, due to the different varieties of I-beams, the pass slope is also different, generally ranging from 1.5% to 9%. When the rolled piece passes through the first pass of the second universal mill stand, the cylindrical vertical rolls first flatten the legs of the rolled piece, and then in the return pass, the vertical rolls are lifted, and only the horizontal rolls are used to press the leg ends. On the last universal mill stand, the rolled piece is fully processed with horizontal rolls and vertical rolls.
4.Production process of H-beam steel
To produce H-beam steel with good quality and low cost, it is necessary to determine a reasonable production process first. Generally, small-sized H-beam steel mostly uses square billets, and large-sized H-beam steel mostly uses shaped billets. Both square billets and shaped billets can be supplied by continuous casting billets or directly by initial rolling. After the steel billet is finished and weighed, it is loaded into a step-type heating furnace and heated to 1200~1250°C and then taken out of the furnace. Most step-type furnaces use double insulating guide rails and axial flow burners, which can provide the best temperature control for different specifications of steel billets and save fuel. After the steel billet is taken out of the furnace, it is first descaled with high-pressure water at 1800MPa, and then sent to the blooming mill for rolling. The blooming mill is generally a two-roll reversible mill, and about 7 to 13 passes are needed on the blooming mill, and then the rolled piece is sent to the hot saw, which is only responsible for cutting off the unformed head and tail parts. Finally, the rolled piece is sent to the universal rough rolling mill for rolling, and after several passes, it is sent to the universal finishing mill for the final pass to form. At this time, the head and tail are cut off again, and the rolled piece is cut to the specified length according to the order requirements and then sent to the cooling bed for cooling.Due to the large ratio of leg thickness to web thickness of H-beam, if placed flat, it is easy to cause wavy webs due to the uneven cooling speed of the web and legs. Therefore, vertical cooling is generally used. Now, most use step-type cooling beds, which can not only reduce the defects caused by the original chain dragging mechanism but also easily control the cooling speed of the steel. After cooling, the H-beam steel is sent to the straightening machine for straightening. Due to the large cross-sectional modulus of H-beam steel, an 8-roll or 9-roll straightening machine is generally used for straightening, with the maximum distance between the straightening rolls being 2200mm, and additional straightening is also required with a horizontal straightener. After straightening, the steel is sent to the inspection platform for inspection of size, shape, and surface quality, and is marked according to the standard, then classified, stacked, and bundled according to different grades and lengths, and sent to the warehouse. For unqualified products, theyare re-straightened as reprocessing products, cut with a cold saw, or repaired and welded before being re-inspected.
To improve the utilization rate of the rolling mill and reduce the roll changing time, most factories use a quick roll changing system, that is, while producing, the next variety of rolls required are pre-assembled. When changing rolls, just pull out all the original frames and replace them with the assembled new frames. Each frame is equipped with an automatic electrical connection, as well as quick connectors for cooling water, thin oil, and dry oil pipes and connecting rods for positioning and connection. This device is convenient and fast to connect and disconnect, and the entire roll changing time is about 20 minutes. To effectively control the production process, modern H-beam steel mills all use computer control. There are generally three levels of control systems, the first level is used for production organization management, using large computers for DDC control (Direct Digital Control); the second level is for controlling the production process, that is, program control, and the program control computer is generally divided into two lines for control, one line controls the hot rolling operation area, and one line controls the finishing operation area; the third level is for controlling each process, including control of heating, rolling, sawing and other processes, and is generally controlled by a microcomputer. The production information of each process microcomputer is reflected to its respective program control machine through an intermediate computer, and after analysis and summary by the program control machine, it is reflected to the central control machine, which then issues the next adjustment and control instructions according to the production standard requirements.
In summary, due to the rapid response of the computer, it can collect and process quality information in a timely manner, so computer control is the best means for production process control.
5. Selection of H-beam steel production technology
In recent decades, with the progress of continuous casting technology and the improvement of online computer control and rolling automation, the production technology of H-beam steel has also become increasingly mature. According to the different billet materials used, the different pass system used, and the types of rolling mills, there are many different process combinations, and there are currently five available production processes for H-beam steel.The first production process uses traditional steel ingots as raw materials. First, the steel ingot is rolled into a rectangular billet or square billet on the primary mill, and then these rectangular billets or square billets are heated and sent to the blooming mill for rolling. There are two different pass system designs for the blooming mill, namely closed pass system and open pass system.
In the closed pass system, the material deformation is uniform, but this requires a larger number of passes and a longer roll length. For this reason, the closed pass system is widely used for producing medium-section steel. The open pass system is mainly used for producing large-section steel with larger web width and leg width. If you want to use the closed pass system to roll large-section steel, you need two blooming mills to achieve a technically satisfactory effect. The steel billet is rolled into a "dog bone" shaped billet on the blooming mill, and then sent to the universal rough rolling mill composed of 1~2 universal reversible rough rolling mill stands for rolling. The rolling of the horizontal rolls and the lateral pressure of the vertical rolls make the web thickness of the billet further thinned, and the legs become more pointed and flat. Usually, the compression amount of the leg thickness is greater than that of the web thickness, which can be explained by the contact length of the rolled piece with the rolls in the deformation zone, because the contact length of the driven vertical rolls with the rolled piece is longer than that of the horizontal rolls with the rolled piece. On the universal finishing mill stand, the rolled piece undergoes a small compression by the horizontal rolls and vertical rolls, as well as the correction of the leg end by the edge rolling mill.
The second production process uses continuous casting rectangular billets. The difference from the first production process is that there is no need for a primary mill, and the second process can obtain a higher yield, better finished product quality, and better economic benefits for producing H-beam steel than the first process. The only limitation of this process is that the legs of the H-beam steel produced are wider because the thickness of the continuous casting billet is limited by the equipment conditions of the continuous casting machine. The rolling process of the continuous casting billet in the steel mill is the same as the first one.
The third production process uses continuous casting shaped billets. The advantage of this process is that one or a few types of continuous casting shaped billets can be used to produce all sizes of H-beam steel, which can be achieved by using a wide flange method on the blooming mill, and the pass can be either closed or open. Compared with the first two processes, this production process has fewer pass numbers. The disadvantage of this process is that it is limited by the leg width of the continuous casting shaped billet. The rolling process after blooming is the same as the first two methods, which requires rough rolling by the universal rough rolling mill and forming by the universal finishing rolling mill.
The fourth production process uses continuous casting slabs as raw materials. Producing H-beam steel with continuous casting slabs is more economical than using primary billets and continuous casting shaped billets, but it requires a special pass design on the blooming mill. This pass is similar to the pass for rolling steel rails, and it is a wedge with a certain angle used to roll the slab into a "dog bone" shaped section. For this reason, the slab must first be rolled vertically in the first pass to form the required leg width, and then rolled into a "dog bone" shaped billet in the next shaped hole (either open or closed can be used). This production process is more uniform than the first three, and its advantage is that only one blooming mill plus a universal rough rolling mill plus a universal finishing rolling mill can be used to produce large-sized H-beam steel. There is also a modified process on the blooming mill, which is the blooming mill uses a universal slab blooming mill, and the lateral pressure formed by the horizontal rolls and vertical rolls at a certain angle can directly roll out a "dog bone" shaped section. The subsequent processes are the same as the first process.
The fifth production process uses continuous casting shaped billets with very thin web thickness as raw materials. This thin continuous casting shaped billet is close to the size of the finished H-beam steel, so it can be directly rough rolled and finished rolled on the universal mill stand without the need for a blooming mill. In this case, the direction for increasing output is to require the continuous casting machine to have a higher casting speed and to be able to cast thinner shaped sections. The characteristic of rolling is that the deformation of the entire rolling process is more uniform.