Submerged arc welding is a welding method in which an arc burns under a layer of flux. Its inherent advantages such as stable welding quality, high welding productivity, no arc light and little smoke make it the main welding method in the manufacture of important steel structures such as pressure vessels, pipe section manufacturing (such as SSAW pipe and LSAW pipe), and box-shaped beams and columns.
Advantages of Submerged Arc Welding
1. High production efficiency
This is because, on the one hand, the conductive length of the welding wire is shortened, and the current and current density are increased, so the penetration depth of the arc and the deposition efficiency of the welding wire are greatly improved. On the other hand, due to the heat insulation effect of flux and slag, there is basically no heat radiation loss on the arc, and there is less spatter. Although the heat loss for melting flux increases, the overall thermal efficiency is still greatly increased.
2. High weld quality
The slag has a good protective effect in insulating the air, the welding parameters can be kept stable through automatic adjustment, the technical level of the welder is not high, the weld composition is stable, and the mechanical properties are relatively good.
3. Good working conditions
In addition to reducing the labor intensity of manual welding operations, it has no arc radiation, which is a unique advantage of submerged arc welding.
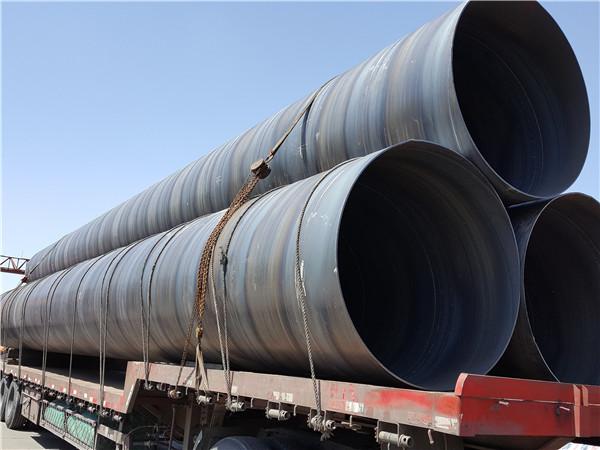
The main disadvantages of submerged arc welding:
1. Submerged arc welding is protected by granular flux, which is generally only suitable for welding in flat welding and fillet welding positions. For welding at other positions, special devices are required to ensure that the flux covers the weld area and prevent leakage of molten pool metal.
2. The relative position of the arc and the groove cannot be directly observed during welding, and an automatic welding seam tracking device is required to ensure that the welding torch is aligned with the welding seam without welding deviation.
3. Submerged arc welding uses a large current, and the electric field strength of the arc is high. When the current is less than 100A, the arc stability is poor, so it is not suitable for welding thin-walled pipes.
Advantages of Submerged Arc Welding
1. High production efficiency
This is because, on the one hand, the conductive length of the welding wire is shortened, and the current and current density are increased, so the penetration depth of the arc and the deposition efficiency of the welding wire are greatly improved. On the other hand, due to the heat insulation effect of flux and slag, there is basically no heat radiation loss on the arc, and there is less spatter. Although the heat loss for melting flux increases, the overall thermal efficiency is still greatly increased.
2. High weld quality
The slag has a good protective effect in insulating the air, the welding parameters can be kept stable through automatic adjustment, the technical level of the welder is not high, the weld composition is stable, and the mechanical properties are relatively good.
3. Good working conditions
In addition to reducing the labor intensity of manual welding operations, it has no arc radiation, which is a unique advantage of submerged arc welding.
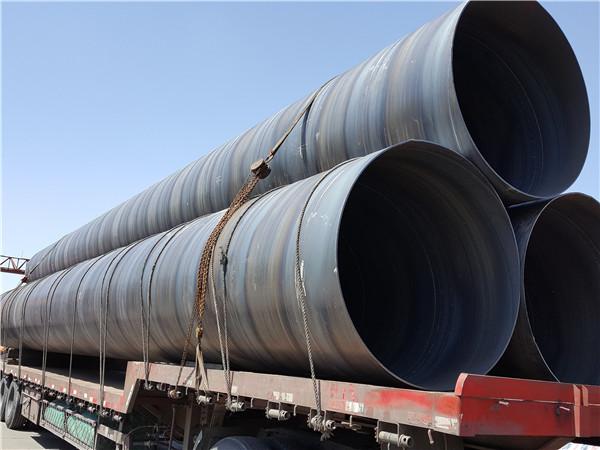
The main disadvantages of submerged arc welding:
1. Submerged arc welding is protected by granular flux, which is generally only suitable for welding in flat welding and fillet welding positions. For welding at other positions, special devices are required to ensure that the flux covers the weld area and prevent leakage of molten pool metal.
2. The relative position of the arc and the groove cannot be directly observed during welding, and an automatic welding seam tracking device is required to ensure that the welding torch is aligned with the welding seam without welding deviation.
3. Submerged arc welding uses a large current, and the electric field strength of the arc is high. When the current is less than 100A, the arc stability is poor, so it is not suitable for welding thin-walled pipes.