External fold is a common outer surface defect of seamless steel pipe, which is characterized by helical layered folds on the outer surface of the steel pipe. The outward folding of seamless steel pipes is mostly caused by the defects of the billet. During the rolling process of the steel pipe, because the billet is subjected to frequent alternating tensile stress, the stress state is relatively bad, and it is easy to expand the defects of the billet. The corresponding inner surface defect is the inward fold of the seamless steel pipe, which is characterized by straight line or helical or semi-spiral zigzag defects on the inner surface of the steel pipe.
The outer folding of seamless steel pipe is divided into steel outer folding and operation outer folding
1.Steel folding
There are two main types of steel outer folds: the first is the irregular sheet-like folds on the outer surface of the steel pipe, and the folded outer edges are serrated, or due to the influence of certain factors in the process of processing the ladle and baking the alloy material, a large number of bubbles may appear.However, after the steel pipe is billeted, the bubbles are rolled and leaked, and cracks are gradually formed. Another reason is that the cold skin generated by the billet during the casting process is not cleaned up.
The second is the regular large helical folds on the outer surface of the steel pipe. The main reason for such defects is generally that the surface of the billet is scratched by the edge of the limit roller during the continuous casting process, forming a straight track or forming a lug. Or there are cracks on the surface of the continuous casting billet, the straights are not cleaned up during the billet finishing, or the edges of the straights are not smoothly transitioned, resulting in folds on the outer surface during perforation.
2.Operation fold out
There are mainly two types of external folding: linear short line and spiral external folding. The short linear outward folds are mainly caused by the deep and steep grooves in the bite section of the piercing machine rolls; the spiral outward folds are mainly caused by the use of rolls with damaged surfaces or improper adjustment of the rolling type during rolling.
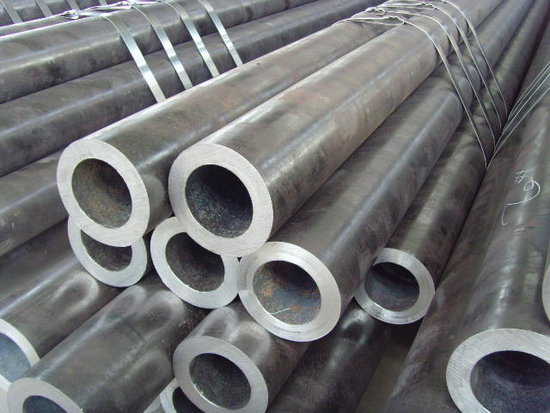
3.Methods and solutions for controlling external folds.
1)Guarantee the quality of the billet. And strengthen the clean-up work when making pipes
2)Appropriately improve the performance of mold slag to improve the rolling quality of seamless tubes, and by reasonably controlling the thickness of the liquid slag layer to ensure that a sufficient amount of liquid slag flows into the air gap between the solidification shell and the mold wall.
3)Reasonably adjust the piercing machine and rolling mill pass, if the surface of the roll is seriously worn, it should be replaced in time. The cooling water baffle is placed at the position of the rollers of the continuous rolling mill to avoid affecting the production quality of the steel billet due to the unshunted cooling water
The outer folding of seamless steel pipe is divided into steel outer folding and operation outer folding
1.Steel folding
There are two main types of steel outer folds: the first is the irregular sheet-like folds on the outer surface of the steel pipe, and the folded outer edges are serrated, or due to the influence of certain factors in the process of processing the ladle and baking the alloy material, a large number of bubbles may appear.However, after the steel pipe is billeted, the bubbles are rolled and leaked, and cracks are gradually formed. Another reason is that the cold skin generated by the billet during the casting process is not cleaned up.
The second is the regular large helical folds on the outer surface of the steel pipe. The main reason for such defects is generally that the surface of the billet is scratched by the edge of the limit roller during the continuous casting process, forming a straight track or forming a lug. Or there are cracks on the surface of the continuous casting billet, the straights are not cleaned up during the billet finishing, or the edges of the straights are not smoothly transitioned, resulting in folds on the outer surface during perforation.
2.Operation fold out
There are mainly two types of external folding: linear short line and spiral external folding. The short linear outward folds are mainly caused by the deep and steep grooves in the bite section of the piercing machine rolls; the spiral outward folds are mainly caused by the use of rolls with damaged surfaces or improper adjustment of the rolling type during rolling.
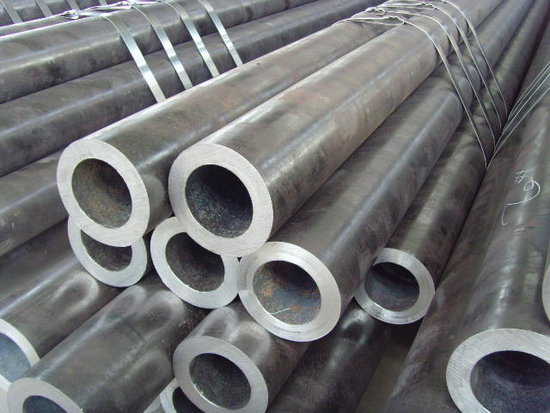
3.Methods and solutions for controlling external folds.
1)Guarantee the quality of the billet. And strengthen the clean-up work when making pipes
2)Appropriately improve the performance of mold slag to improve the rolling quality of seamless tubes, and by reasonably controlling the thickness of the liquid slag layer to ensure that a sufficient amount of liquid slag flows into the air gap between the solidification shell and the mold wall.
3)Reasonably adjust the piercing machine and rolling mill pass, if the surface of the roll is seriously worn, it should be replaced in time. The cooling water baffle is placed at the position of the rollers of the continuous rolling mill to avoid affecting the production quality of the steel billet due to the unshunted cooling water