Basic knowledge of seamless steel pipes
Seamless steel pipe is a widely used steel material and has been widely used in petroleum, natural gas, chemical industry, machinery manufacturing and other fields. It has the advantages of high strength, corrosion resistance and high temperature resistance, and is suitable for transportation and manufacturing in high pressure, high temperature and low temperature environments. The manufacturing process of seamless steel pipes is complex, and common defects include inner wall defects, outer wall defects, carbonization, inclusions, etc.
Seamless steel pipe quality requirements
b. Residual elements: brought in from steelmaking, properly controlled
c. Harmful elements: strictly controlled (As, Sn, Sb, Bi, Pb), gases (N, H, O)
Out-of-furnace refining or electroslag remelting: improve the uniformity of the chemical composition of the steel and the purity of the steel, reduce non-metallic inclusions in the tube blank and improve its distribution pattern.
2. steel pipe geometric size accuracy and shape
a. Steel pipe outer diameter accuracy: depends on the diameter determination (reduction) method, equipment operation conditions, process system, etc.
Allowable deviation of outer diameter δ=(D-Di)/Di ×100% D: Maximum or minimum outer diameter mm
Di: nominal outer diameter mm
b. Steel pipe wall thickness accuracy: It is related to the heating quality of the tube blank, the process design parameters and adjustment parameters of each deformation process, the tool quality and its lubrication quality, etc.
Allowable deviation of wall thickness: ρ=(S-Si)/Si×100% S: maximum or minimum wall thickness on cross section
Si: nominal wall thickness mm
c. Steel pipe ovality: indicates the degree of out-of-roundness of the steel pipe.
d. Steel pipe length: normal length, fixed (multiple) ruler length, length tolerance
e. Steel pipe curvature: Indicates the curvature of the steel pipe: curvature per meter of steel pipe length, curvature of the entire length of the steel pipe
f. Steel pipe end face slope: Indicates the degree of inclination between the steel pipe end face and the steel pipe cross section
g. Steel pipe end bevel angle and blunt edge
b. General defects: pockmarks, green lines, scratches, bruises, slight inside and outside straights, roller marks, etc.
5. Steel pipe process performance: flattening, flaring, curling, bending, welding, etc.
Acceptance specifications and standards for seamless steel pipes
The acceptance of seamless steel pipes should follow corresponding specifications and standards, mainly including appearance inspection, physical performance testing and chemical composition testing. The following are common acceptance specifications and standards for seamless steel pipes:
2. Physical performance testing
Physical performance testing mainly includes tensile test, flattening test, torsion test and pressure test. Tensile testing is the most basic test and uates the mechanical properties of steel pipes such as strength, toughness and elongation. The flattening test and torsion test mainly test the torque resistance and flattening resistance of seamless steel pipes. The pressure test is to uate the pressure resistance of the pipe. The test pressure shall not be less than 1.5 times the nominal pressure or design pressure.
3. Chemical composition testing
Chemical composition testing is an important indicator for uating the quality of seamless steel pipes. The main test elements include carbon (C), sulfur (S), copper (Cu), phosphorus (P), manganese (Mn), molybdenum (Mo), etc. Chemical composition testing should be conducted at appropriate temperature and pH, and the test results should comply with the requirements of relevant standards.
Precautions and common mistakes
During the acceptance process of seamless steel pipes, the following matters need to be paid attention to:
1. Acceptance must be carried out in strict accordance with relevant standards and specifications, and requirements shall not be violated.
2. Appearance inspection should be done carefully and no details should be overlooked.
3. Physical performance testing and chemical composition testing should be conducted under appropriate conditions, and the test results should be accurate and reliable.
4. After the acceptance is completed, the test results and defect conditions should be recorded in a timely manner, and corresponding records and reports should be made.
Common errors include: failure to conduct acceptance in accordance with corresponding standards and specifications, failure to carefully inspect the appearance, inappropriate test conditions or inaccurate test results, etc.
Seamless steel pipe is a widely used steel material and has been widely used in petroleum, natural gas, chemical industry, machinery manufacturing and other fields. It has the advantages of high strength, corrosion resistance and high temperature resistance, and is suitable for transportation and manufacturing in high pressure, high temperature and low temperature environments. The manufacturing process of seamless steel pipes is complex, and common defects include inner wall defects, outer wall defects, carbonization, inclusions, etc.
Seamless steel pipe quality requirements
1. Chemical composition of steel: The chemical composition of steel is one of the most important factors affecting the performance of seamless steel pipes. It is also the main basis for formulating pipe rolling process parameters and steel pipe heat treatment process parameters.
a. Alloying elements: intentionally added, according to purpose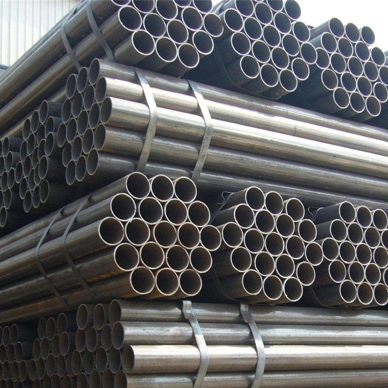
b. Residual elements: brought in from steelmaking, properly controlled
c. Harmful elements: strictly controlled (As, Sn, Sb, Bi, Pb), gases (N, H, O)
Out-of-furnace refining or electroslag remelting: improve the uniformity of the chemical composition of the steel and the purity of the steel, reduce non-metallic inclusions in the tube blank and improve its distribution pattern.
2. steel pipe geometric size accuracy and shape
a. Steel pipe outer diameter accuracy: depends on the diameter determination (reduction) method, equipment operation conditions, process system, etc.
Allowable deviation of outer diameter δ=(D-Di)/Di ×100% D: Maximum or minimum outer diameter mm
Di: nominal outer diameter mm
b. Steel pipe wall thickness accuracy: It is related to the heating quality of the tube blank, the process design parameters and adjustment parameters of each deformation process, the tool quality and its lubrication quality, etc.
Allowable deviation of wall thickness: ρ=(S-Si)/Si×100% S: maximum or minimum wall thickness on cross section
Si: nominal wall thickness mm
c. Steel pipe ovality: indicates the degree of out-of-roundness of the steel pipe.
d. Steel pipe length: normal length, fixed (multiple) ruler length, length tolerance
e. Steel pipe curvature: Indicates the curvature of the steel pipe: curvature per meter of steel pipe length, curvature of the entire length of the steel pipe
f. Steel pipe end face slope: Indicates the degree of inclination between the steel pipe end face and the steel pipe cross section
g. Steel pipe end bevel angle and blunt edge
3. Steel pipe surface quality: surface smoothness requirements
a. Dangerous defects: cracks, inward folds, outward folds, rolling breaks, delamination, scarring, dents, convex bulges, etc.
a. Dangerous defects: cracks, inward folds, outward folds, rolling breaks, delamination, scarring, dents, convex bulges, etc.
b. General defects: pockmarks, green lines, scratches, bruises, slight inside and outside straights, roller marks, etc.
4. Steel management properties: normal temperature mechanical properties, high temperature mechanical properties, low temperature properties, corrosion resistance. The physical and chemical properties of steel pipes mainly depend on the chemical composition of the steel, the organizational structure and the purity of the steel, as well as the heat treatment method of the steel pipe.
5. Steel pipe process performance: flattening, flaring, curling, bending, welding, etc.
6. Metallurgical structure of steel pipe: low-magnification structure (macro), high-magnification structure (micro) M, B, P, F, A, S
7. Special requirements for steel pipes: contract attachments and technical agreements.
7. Special requirements for steel pipes: contract attachments and technical agreements.
Acceptance specifications and standards for seamless steel pipes
The acceptance of seamless steel pipes should follow corresponding specifications and standards, mainly including appearance inspection, physical performance testing and chemical composition testing. The following are common acceptance specifications and standards for seamless steel pipes:
1. Appearance inspection
The appearance of seamless steel pipes should be flat and smooth, and the surface should be free of defects such as cracks, wrinkles, and folds. A small amount of minor scratches and oxide layers are allowed. The diameter, wall thickness, and verticality and flatness of the outer wall and end face should comply with the requirements of the corresponding standards.2. Physical performance testing
Physical performance testing mainly includes tensile test, flattening test, torsion test and pressure test. Tensile testing is the most basic test and uates the mechanical properties of steel pipes such as strength, toughness and elongation. The flattening test and torsion test mainly test the torque resistance and flattening resistance of seamless steel pipes. The pressure test is to uate the pressure resistance of the pipe. The test pressure shall not be less than 1.5 times the nominal pressure or design pressure.
3. Chemical composition testing
Chemical composition testing is an important indicator for uating the quality of seamless steel pipes. The main test elements include carbon (C), sulfur (S), copper (Cu), phosphorus (P), manganese (Mn), molybdenum (Mo), etc. Chemical composition testing should be conducted at appropriate temperature and pH, and the test results should comply with the requirements of relevant standards.
Precautions and common mistakes
During the acceptance process of seamless steel pipes, the following matters need to be paid attention to:
1. Acceptance must be carried out in strict accordance with relevant standards and specifications, and requirements shall not be violated.
2. Appearance inspection should be done carefully and no details should be overlooked.
3. Physical performance testing and chemical composition testing should be conducted under appropriate conditions, and the test results should be accurate and reliable.
4. After the acceptance is completed, the test results and defect conditions should be recorded in a timely manner, and corresponding records and reports should be made.
Common errors include: failure to conduct acceptance in accordance with corresponding standards and specifications, failure to carefully inspect the appearance, inappropriate test conditions or inaccurate test results, etc.