1. Seamless steel pipe expansion and contraction
This is a situation where there is a surface or inner layer of seamless steel pipe, which is vertical or spiral, continuous or discontinuous. The main cause of expansion and contraction is that the quality of the pipe material is poor, the pipe itself has expansion and contraction, or the surface is mixed, serious scratches and gaps, there are edges and corners on the grinding, and they widen after drawing to cause expansion and contraction. In order to prevent the formation of expansion and contraction, the quality of pipe materials should be improved and regular inspection and sharpening should be paid attention to.
2. Seamless steel pipe cracks
It refers to the vertical or spiral distribution of fine cracks on the inner and outer surfaces of seamless steel pipes. The depth is about 1mm or 1mm, and there are continuous and discontinuous cracks.
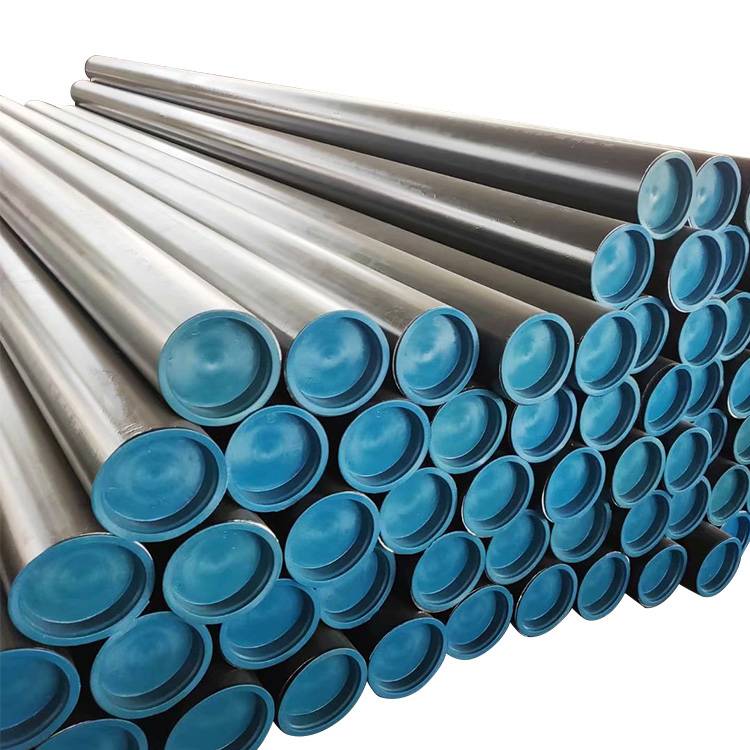
The reasons are: there are subcutaneous tissue bubbles and subcutaneous tissue inclusions in the hot-rolled tube blank, and there are cracks or deep black spots on the seamless steel pipe before drawing, which are formed during hot rolling or cold drawing process operations. Vertical scratches or scratches. To avoid the establishment of cracks, we also need to improve the quality of pipe materials and improve the regular inspection and sharpening of pipe materials. At the same time, efforts should be made to avoid black spots, scratches and scratches on the pipe during cold drawing production.
3. Seamless steel pipe scratched
The characteristic of the defect is that vertical linear scratches of varying lengths appear on the inner and outer surfaces of the seamless steel pipe, most often in the shape of grooves, but they may also be protruding patterns. The main causes of scratches (scratching) are: there are internal scratches on the pipe material, which cannot be removed during drawing, zinc ash remains on the seamless steel pipe and the steel is reinforced with abrasive tools, and the strength and hardness of the abrasive tools are insufficient or incorrect. Evenly, the grinding tool is broken and damaged, the drill bit is poor, and the sharp corners where the drill bit is connected damage the grinding tool, etc. In order to avoid scratches and scratches, the quality of the preparation process before drawing should be improved, and grinding tools with greater strength, hardness, and better smoothness should be used.
4. Seamless steel pipe dents
This is one of the more common surface defects of seamless steel pipes. There are partial dents of different areas distributed on the surface of seamless steel pipes, some with regularity and some with no regularity. The formation of dents is mainly due to zinc dust or other hard waste being pressed into the surface of the seamless steel pipe during the drawing or straightening process, or the original warped skin on the surface of the seamless steel pipe falling off. The editor emphasizes that the measures to avoid dents are to carefully inspect the pipe material and remove defects such as warped skin, keep the working environment and tool lubricants clean, and prevent zinc dust and waste from falling into the surface of the seamless steel pipe.
If there are round or sharp spiral scratches on the surface of the seamless steel pipe, the straightening machine should be inspected. Because the straightening roller is skewed and the viewing angle is wrong, the seamless steel pipe rubs the convex shoulder on the edge of the straightening roller during straightening. There are damaged concave grooves on the straightening roller. Excessive bending on both sides of the seamless steel pipe may cause damage. Create dents on the surface of seamless steel pipes.
This is a situation where there is a surface or inner layer of seamless steel pipe, which is vertical or spiral, continuous or discontinuous. The main cause of expansion and contraction is that the quality of the pipe material is poor, the pipe itself has expansion and contraction, or the surface is mixed, serious scratches and gaps, there are edges and corners on the grinding, and they widen after drawing to cause expansion and contraction. In order to prevent the formation of expansion and contraction, the quality of pipe materials should be improved and regular inspection and sharpening should be paid attention to.
2. Seamless steel pipe cracks
It refers to the vertical or spiral distribution of fine cracks on the inner and outer surfaces of seamless steel pipes. The depth is about 1mm or 1mm, and there are continuous and discontinuous cracks.
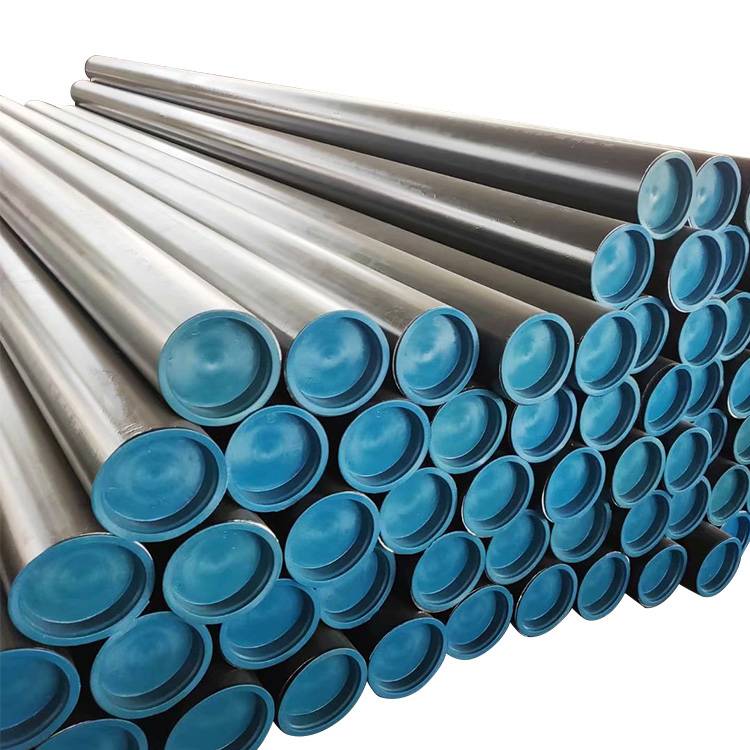
The reasons are: there are subcutaneous tissue bubbles and subcutaneous tissue inclusions in the hot-rolled tube blank, and there are cracks or deep black spots on the seamless steel pipe before drawing, which are formed during hot rolling or cold drawing process operations. Vertical scratches or scratches. To avoid the establishment of cracks, we also need to improve the quality of pipe materials and improve the regular inspection and sharpening of pipe materials. At the same time, efforts should be made to avoid black spots, scratches and scratches on the pipe during cold drawing production.
3. Seamless steel pipe scratched
The characteristic of the defect is that vertical linear scratches of varying lengths appear on the inner and outer surfaces of the seamless steel pipe, most often in the shape of grooves, but they may also be protruding patterns. The main causes of scratches (scratching) are: there are internal scratches on the pipe material, which cannot be removed during drawing, zinc ash remains on the seamless steel pipe and the steel is reinforced with abrasive tools, and the strength and hardness of the abrasive tools are insufficient or incorrect. Evenly, the grinding tool is broken and damaged, the drill bit is poor, and the sharp corners where the drill bit is connected damage the grinding tool, etc. In order to avoid scratches and scratches, the quality of the preparation process before drawing should be improved, and grinding tools with greater strength, hardness, and better smoothness should be used.
4. Seamless steel pipe dents
This is one of the more common surface defects of seamless steel pipes. There are partial dents of different areas distributed on the surface of seamless steel pipes, some with regularity and some with no regularity. The formation of dents is mainly due to zinc dust or other hard waste being pressed into the surface of the seamless steel pipe during the drawing or straightening process, or the original warped skin on the surface of the seamless steel pipe falling off. The editor emphasizes that the measures to avoid dents are to carefully inspect the pipe material and remove defects such as warped skin, keep the working environment and tool lubricants clean, and prevent zinc dust and waste from falling into the surface of the seamless steel pipe.
If there are round or sharp spiral scratches on the surface of the seamless steel pipe, the straightening machine should be inspected. Because the straightening roller is skewed and the viewing angle is wrong, the seamless steel pipe rubs the convex shoulder on the edge of the straightening roller during straightening. There are damaged concave grooves on the straightening roller. Excessive bending on both sides of the seamless steel pipe may cause damage. Create dents on the surface of seamless steel pipes.