1. The importance of bevel processing
(1) Achieve full penetration of the interface
Generally speaking, in order to ensure the stability of the welding position, the thickness of the deposited metal must be consistent with the pipe wall. The welds at the connection points can be formed on both sides to prevent the occurrence of false welding and false welding problems. However, it is difficult to control the welding quality inside the pipeline, and incomplete welding often occurs, which seriously affects the overall quality of the pipeline. The groove processing changes the design of the welding joint to enhance the stability of the interface in a more fitting way. Moreover, in thin-walled pipe projects such as energy transmission, full penetration is easier to achieve, and has gradually become a new standard for welding in the industry in recent years.
(2) Avoid steel pipe corrosion
There are many causes of pipeline corrosion, but most of them are caused by the local natural environment and oxidation reaction. Especially for some projects laid in the wild, precipitation and sunlight exposure will cause external rust. The reason is mainly due to the chemical reaction that occurs during high temperature welding, and the carbides in the steel pipe are discharged, which greatly reduces the rust resistance of the pipe. Not only that, traditional welding methods usually use partial welding, which may cause the welding joint to be susceptible to oxidation reactions. For bevel processing, geometric grooves are installed at the welding position to make the structure at both ends more stable. The more closed structure not only prevents oxidation reactions from occurring, but also prevents pollutants from entering the pipeline and causing damage to the inner wall.
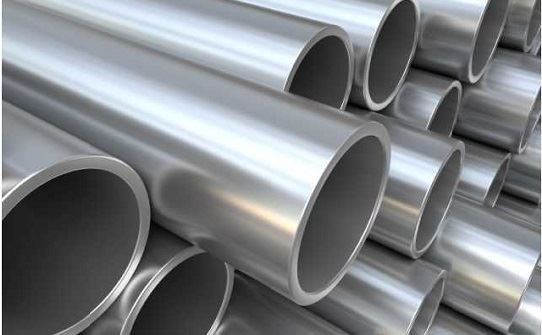
(3) Improve weld strength
In order to ensure the normal use of the pipeline, the strength of the weld must be higher than that of the base material, and even must be maintained at 150%-200%. However, welding work is more complicated, and the strength of the weld is affected by many factors. The groove design requires that the thickness of the weld be consistent with the base metal, and heat treatment must be performed immediately after high-temperature welding. This improves the fatigue resistance of the weld, and its performance even far exceeds that of the base material.
2. Current problems in seamless steel pipe bevel processing
(1) The technology is relatively weak
Since China's research on welding groove processing started late, the theoretical system and practical measures are not yet complete. The backwardness of the technology leads to the lack of guidance in specific welding, and quality problems such as misoperation often occur. For example, if technicians make errors in the design of the groove gap, it is easy for metal deposition to penetrate deep into the inner wall of the pipe during the welding process. This will not only cause internal blockage, but also lead to incomplete welding of the welding structure, seriously affecting the quality of the pipeline.
(2) Equipment needs to be improved
There are many methods of beveling processing, and the forms of beveling machines at this stage also show a diversified trend. However, judging from the current situation of the industry, the hardware equipment of pipe processing enterprises is generally relatively backward, and quality problems are naturally prone to occur in specific work. The introduction and purchase of beveling machines requires a large amount of money, and companies tend to pay more attention to short-term economic benefits. More attention is paid to the progress of the project, while the beveling machine equipment, which is closely related to quality, is ignored. After field research, the author found that some companies still use flame gas cutting and plasma cutting in bevel processing. Although these technologies can produce good results after grinding with a grinder, they are obviously out of date in today's large-diameter pipeline projects. Some projects are equipped with bevels due to the lack of machines, a combination of machining and traditional cutting methods must be used during the construction process. This is also a prominent problem at present.
3. Strategies to improve the quality of seamless steel pipe bevel processing
Currently, the most common ones in the industry are Y, V and U-shaped grooves. This symmetrical design ensures uniform heating. For example, in the V-shaped groove design, machining can be used to complete the cutting in one go. In this way, the input heat can be effectively controlled, and the final weld size error can also be guaranteed. U-shaped beveling has been highly praised by the industry for its simplicity and efficiency, and it is less dependent on beveling machines. This design form can be directly processed by flame gas cutting, and the entire process can be completed in a very short time. It can be seen that different design forms have different characteristics. During the specific construction process, technical personnel should make comprehensive considerations based on the project's usage standards and economic factors.
To sum up, in large-diameter, thick-walled seamless steel pipes and projects with high quality requirements, traditional welding technology is prone to cracking and corrosion. By making bevels during the welding process, we can effectively achieve the goal of welding penetration and ensure that the project can be put into production safely. This requires the industry to continuously innovate, popularize seamless welding groove technology, and improve construction practice measures.
(1) Achieve full penetration of the interface
Generally speaking, in order to ensure the stability of the welding position, the thickness of the deposited metal must be consistent with the pipe wall. The welds at the connection points can be formed on both sides to prevent the occurrence of false welding and false welding problems. However, it is difficult to control the welding quality inside the pipeline, and incomplete welding often occurs, which seriously affects the overall quality of the pipeline. The groove processing changes the design of the welding joint to enhance the stability of the interface in a more fitting way. Moreover, in thin-walled pipe projects such as energy transmission, full penetration is easier to achieve, and has gradually become a new standard for welding in the industry in recent years.
(2) Avoid steel pipe corrosion
There are many causes of pipeline corrosion, but most of them are caused by the local natural environment and oxidation reaction. Especially for some projects laid in the wild, precipitation and sunlight exposure will cause external rust. The reason is mainly due to the chemical reaction that occurs during high temperature welding, and the carbides in the steel pipe are discharged, which greatly reduces the rust resistance of the pipe. Not only that, traditional welding methods usually use partial welding, which may cause the welding joint to be susceptible to oxidation reactions. For bevel processing, geometric grooves are installed at the welding position to make the structure at both ends more stable. The more closed structure not only prevents oxidation reactions from occurring, but also prevents pollutants from entering the pipeline and causing damage to the inner wall.
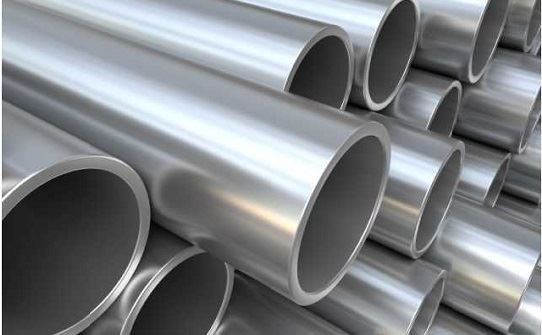
(3) Improve weld strength
In order to ensure the normal use of the pipeline, the strength of the weld must be higher than that of the base material, and even must be maintained at 150%-200%. However, welding work is more complicated, and the strength of the weld is affected by many factors. The groove design requires that the thickness of the weld be consistent with the base metal, and heat treatment must be performed immediately after high-temperature welding. This improves the fatigue resistance of the weld, and its performance even far exceeds that of the base material.
2. Current problems in seamless steel pipe bevel processing
(1) The technology is relatively weak
Since China's research on welding groove processing started late, the theoretical system and practical measures are not yet complete. The backwardness of the technology leads to the lack of guidance in specific welding, and quality problems such as misoperation often occur. For example, if technicians make errors in the design of the groove gap, it is easy for metal deposition to penetrate deep into the inner wall of the pipe during the welding process. This will not only cause internal blockage, but also lead to incomplete welding of the welding structure, seriously affecting the quality of the pipeline.
(2) Equipment needs to be improved
There are many methods of beveling processing, and the forms of beveling machines at this stage also show a diversified trend. However, judging from the current situation of the industry, the hardware equipment of pipe processing enterprises is generally relatively backward, and quality problems are naturally prone to occur in specific work. The introduction and purchase of beveling machines requires a large amount of money, and companies tend to pay more attention to short-term economic benefits. More attention is paid to the progress of the project, while the beveling machine equipment, which is closely related to quality, is ignored. After field research, the author found that some companies still use flame gas cutting and plasma cutting in bevel processing. Although these technologies can produce good results after grinding with a grinder, they are obviously out of date in today's large-diameter pipeline projects. Some projects are equipped with bevels due to the lack of machines, a combination of machining and traditional cutting methods must be used during the construction process. This is also a prominent problem at present.
3. Strategies to improve the quality of seamless steel pipe bevel processing
Currently, the most common ones in the industry are Y, V and U-shaped grooves. This symmetrical design ensures uniform heating. For example, in the V-shaped groove design, machining can be used to complete the cutting in one go. In this way, the input heat can be effectively controlled, and the final weld size error can also be guaranteed. U-shaped beveling has been highly praised by the industry for its simplicity and efficiency, and it is less dependent on beveling machines. This design form can be directly processed by flame gas cutting, and the entire process can be completed in a very short time. It can be seen that different design forms have different characteristics. During the specific construction process, technical personnel should make comprehensive considerations based on the project's usage standards and economic factors.
To sum up, in large-diameter, thick-walled seamless steel pipes and projects with high quality requirements, traditional welding technology is prone to cracking and corrosion. By making bevels during the welding process, we can effectively achieve the goal of welding penetration and ensure that the project can be put into production safely. This requires the industry to continuously innovate, popularize seamless welding groove technology, and improve construction practice measures.