The drainpipe generally adopts spiral steel pipe (SSAW pipe), and the welding method of the spiral steel pipe is submerged arc welding. Since the welded steel pipe is spiral, the received liquid pressure will be distributed on each side of the steel pipe to increase the strength of the spiral steel pipe. If straight seam steel pipes (such as ERW pipes) are used, the general large steel pipes are coiled and welded with steel plates, and the required steel plates are large, which greatly increases the difficulty and cost of manufacturing
In the production of spiral welded pipes, the stability of forming is closely related to the welding quality. Only by improving the forming quality can the welding quality be fully guaranteed. The size and change of the forming gap of the spiral welded pipe during the welding process. In order to ensure a good appearance and a certain depth of penetration of the spiral welded pipe weld, it is required that the gap between the steel plate joints is uniform, and at the same time, different welding specifications are adopted according to different weld gaps.
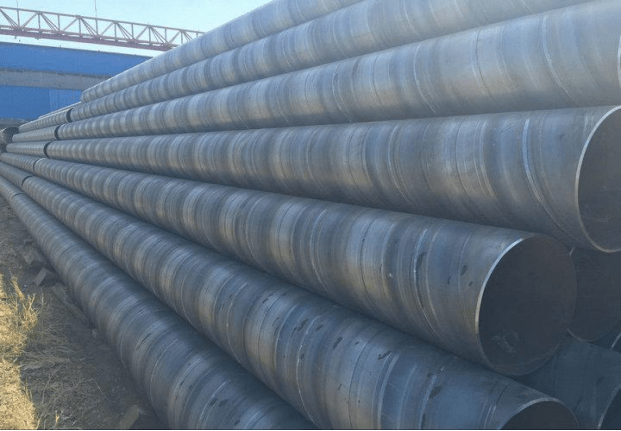
The production control of spiral welded steel pipes for drainage is first of all to improve the plasticity and toughness of steel pipes, improve the cleanliness of molten steel, reduce harmful inclusions, and improve the overall quality of steel pipes. A reasonable cooling system is adopted in the production process to avoid internal cracks and improve the quality of steel pipes from many aspects. The heating temperature of the spiral steel pipe is reasonably controlled during the production process, and the best heating temperature is selected by measuring the thermoplastic curve. It is also necessary to pay attention to sufficient heat preservation time when heating the tube billet to reduce the deformation resistance and improve the plastic toughness of the thick-walled spiral tube.
Corrosion Protection of Spiral Welded Pipes for Drainage
The anti-corrosion method of spiral welded pipes for drain pipes also starts from suppressing one of the processes. However, when the metal material with negative potential of the spiral welded pipe is connected to the spiral steel pipe, this protection law does not appear, so the anti-corrosion coating and sacrificial anode anti-corrosion method should be used in the main gas pipeline of the city. For other non-main pipelines with lower pressure, the anti-corrosion coating method is generally used directly.
At present, the external anti-corrosion layer commonly used for buried gas pipelines has a three-layer PE composite structure. Powdered Epoxy Resin (FBE), Coal Tar Enamel. Five categories such as epoxy coal tar pitch and PE tape. However, it should be noted that sacrificial anode protection should not be used when the soil resistance is too high and the protected pipeline is flooded. Different anti-corrosion methods have different anti-corrosion quality and cost, which should be determined according to the pressure of the spiral welded pipe to be protected.
In the production of spiral welded pipes, the stability of forming is closely related to the welding quality. Only by improving the forming quality can the welding quality be fully guaranteed. The size and change of the forming gap of the spiral welded pipe during the welding process. In order to ensure a good appearance and a certain depth of penetration of the spiral welded pipe weld, it is required that the gap between the steel plate joints is uniform, and at the same time, different welding specifications are adopted according to different weld gaps.
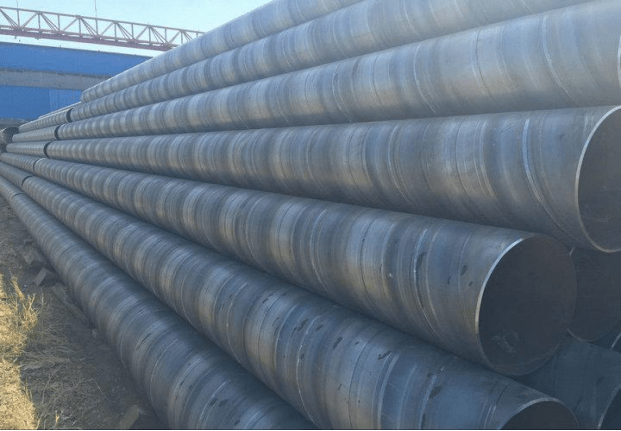
The production control of spiral welded steel pipes for drainage is first of all to improve the plasticity and toughness of steel pipes, improve the cleanliness of molten steel, reduce harmful inclusions, and improve the overall quality of steel pipes. A reasonable cooling system is adopted in the production process to avoid internal cracks and improve the quality of steel pipes from many aspects. The heating temperature of the spiral steel pipe is reasonably controlled during the production process, and the best heating temperature is selected by measuring the thermoplastic curve. It is also necessary to pay attention to sufficient heat preservation time when heating the tube billet to reduce the deformation resistance and improve the plastic toughness of the thick-walled spiral tube.
Corrosion Protection of Spiral Welded Pipes for Drainage
The anti-corrosion method of spiral welded pipes for drain pipes also starts from suppressing one of the processes. However, when the metal material with negative potential of the spiral welded pipe is connected to the spiral steel pipe, this protection law does not appear, so the anti-corrosion coating and sacrificial anode anti-corrosion method should be used in the main gas pipeline of the city. For other non-main pipelines with lower pressure, the anti-corrosion coating method is generally used directly.
At present, the external anti-corrosion layer commonly used for buried gas pipelines has a three-layer PE composite structure. Powdered Epoxy Resin (FBE), Coal Tar Enamel. Five categories such as epoxy coal tar pitch and PE tape. However, it should be noted that sacrificial anode protection should not be used when the soil resistance is too high and the protected pipeline is flooded. Different anti-corrosion methods have different anti-corrosion quality and cost, which should be determined according to the pressure of the spiral welded pipe to be protected.