1.What is steel casing pipe grouting?
Steel casing pipe grouting is a commonly used geological engineering construction method and is widely used in tunnels, bridges, water conservancy projects, drilling and other fields. Its main function is to reinforce and seal underground cavities and cracks to prevent geological disasters.During the casing pipe grouting construction process, certain processes and standards need to be followed to ensure construction quality and safety. The following is a detailed introduction to the construction process of octg casing pipe grouting.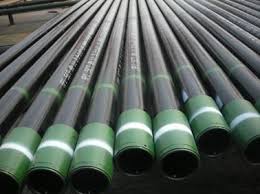