For decades, research on damage to steel casing pipes has never ceased, with significant manpower and resources being devoted to it in oilfields worldwide. Researchers have studied the forms, causes, numerical simulations, measurement methods, and mechanisms of API 5CT casing pipe damage from various perspectives such as petroleum geology, reservoir engineering, materials science and engineering, rock mechanics, material mechanics, geological mechanics, seepage mechanics, corrosion electrochemistry, and prevention.
However, due to the complexity of octg casing pipe failure issues, the aforementioned research is generally conducted for specific oilfields, blocks, and particular well conditions. Numerical simulations often rely on finite element analysis of limited local areas around individual wells, lacking comprehensive analysis of the aforementioned issues. Multidisciplinary, large-scale integrated considerations, which seem more suitable for analysis through numerical simulation, have not yet been summarized by anyone into an expert system. Therefore, the treatment of casing pipe damage remains ineffective, and incidents of casing pipe damage in oilfields still occur.
Damage to casing pipes in the field of petroleum engineering is commonly referred to as casing pipe damage and casing pipe deformation. Casing pipe failure in the petroleum industry refers to the collective term for the deformation, fracture, misalignment, and other forms of damage that occur when the load borne by the casing pipe exceeds its carrying capacity due to factors such as engineering, geological, and production dynamic changes. During the oilfield production process, casing pipe damage, especially in the later stages of oil and gas field development, is a chronic ailment that hampers not only the development of China's oil industry but also that of the world's. It is also one of the key issues affecting the development and profitability improvement of the petroleum industry.
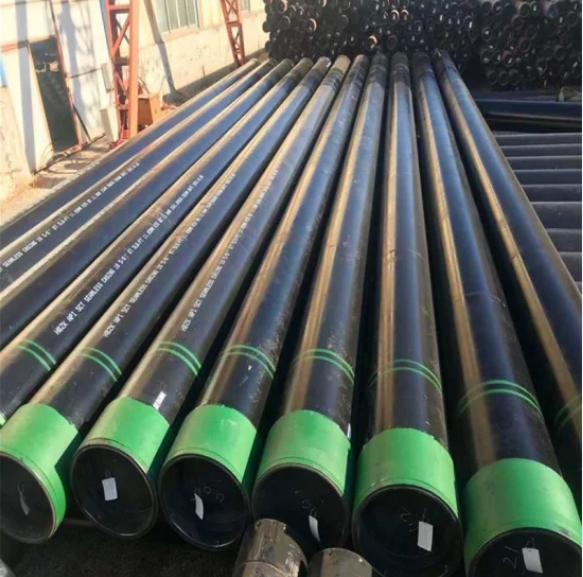
Therefore, from the vast amount of complex data and processes in oilfield geology, engineering, design, construction, production development, and well workover, it is crucial to quickly identify the main causes of steel casing pipe failure and accurately assess the failure mechanisms. However, early research and judgment on the causes and mechanisms of steel casing pipe damage were conducted by experts in the field. In recent years, with the development of computer technology, the widespread application of finite element methods, and the deepening understanding of rock mechanics, seepage mechanics, and elastoplastic mechanics, numerical simulation has been increasingly applied in the analysis of casing pipe deformation causes. A method combining knowledge analysis with numerical analysis has been formed to analyze casing faults. Partial wastage in any form cannot completely solve the problem of steel casing pipe damage. However, knowledge analysis is the primary method, and even though numerical analysis can be used, it cannot solve all the problems in this field, which is exactly where expert systems can demonstrate their capabilities.
So far, research on the destruction of casing pipes has mainly focused on knowledge analysis or numerical analysis of individual casing damage forms. No one has dedicated themselves to establishing a rapid expert system capable of covering the entire oilfield and addressing all casing failure issues. Establishing an expert system covering casing damage throughout the entire oilfield is of great theoretical and practical significance to the treatment of casing damage in China and even worldwide.
The analysis of mechanisms causing damage to steel casing pipes is a complex, arduous, and creative task. It involves oilfield geology, drilling engineering (drill pipe), formulation and adjustment of overall development plans, and implementation of production measures. Prevention, delay, and resolution of steel casing pipe damage are paramount. This work also has important guiding significance for the geological and engineering design of new wells, adjustment of oilfield development plans, and formulation of production measures. It can facilitate the rapid construction of a steel casing pipe fault detection system and provide convenience for monitoring casing faults.
However, due to the complexity of octg casing pipe failure issues, the aforementioned research is generally conducted for specific oilfields, blocks, and particular well conditions. Numerical simulations often rely on finite element analysis of limited local areas around individual wells, lacking comprehensive analysis of the aforementioned issues. Multidisciplinary, large-scale integrated considerations, which seem more suitable for analysis through numerical simulation, have not yet been summarized by anyone into an expert system. Therefore, the treatment of casing pipe damage remains ineffective, and incidents of casing pipe damage in oilfields still occur.
Damage to casing pipes in the field of petroleum engineering is commonly referred to as casing pipe damage and casing pipe deformation. Casing pipe failure in the petroleum industry refers to the collective term for the deformation, fracture, misalignment, and other forms of damage that occur when the load borne by the casing pipe exceeds its carrying capacity due to factors such as engineering, geological, and production dynamic changes. During the oilfield production process, casing pipe damage, especially in the later stages of oil and gas field development, is a chronic ailment that hampers not only the development of China's oil industry but also that of the world's. It is also one of the key issues affecting the development and profitability improvement of the petroleum industry.
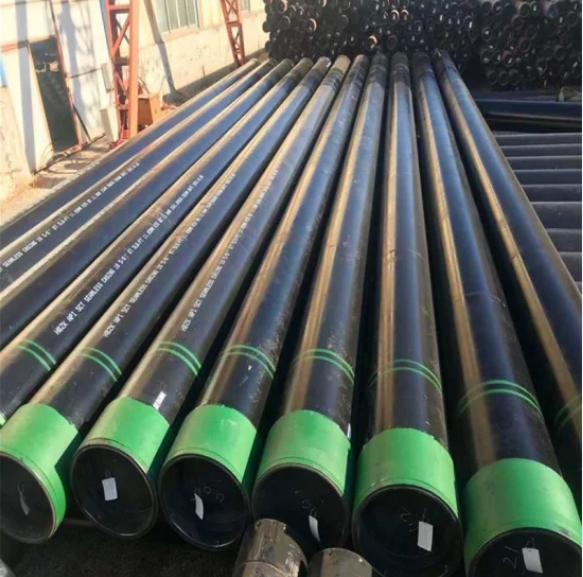
Therefore, from the vast amount of complex data and processes in oilfield geology, engineering, design, construction, production development, and well workover, it is crucial to quickly identify the main causes of steel casing pipe failure and accurately assess the failure mechanisms. However, early research and judgment on the causes and mechanisms of steel casing pipe damage were conducted by experts in the field. In recent years, with the development of computer technology, the widespread application of finite element methods, and the deepening understanding of rock mechanics, seepage mechanics, and elastoplastic mechanics, numerical simulation has been increasingly applied in the analysis of casing pipe deformation causes. A method combining knowledge analysis with numerical analysis has been formed to analyze casing faults. Partial wastage in any form cannot completely solve the problem of steel casing pipe damage. However, knowledge analysis is the primary method, and even though numerical analysis can be used, it cannot solve all the problems in this field, which is exactly where expert systems can demonstrate their capabilities.
So far, research on the destruction of casing pipes has mainly focused on knowledge analysis or numerical analysis of individual casing damage forms. No one has dedicated themselves to establishing a rapid expert system capable of covering the entire oilfield and addressing all casing failure issues. Establishing an expert system covering casing damage throughout the entire oilfield is of great theoretical and practical significance to the treatment of casing damage in China and even worldwide.
The analysis of mechanisms causing damage to steel casing pipes is a complex, arduous, and creative task. It involves oilfield geology, drilling engineering (drill pipe), formulation and adjustment of overall development plans, and implementation of production measures. Prevention, delay, and resolution of steel casing pipe damage are paramount. This work also has important guiding significance for the geological and engineering design of new wells, adjustment of oilfield development plans, and formulation of production measures. It can facilitate the rapid construction of a steel casing pipe fault detection system and provide convenience for monitoring casing faults.