Straightening is an important process in the production of seamless pipes and welded pipes. Especially API standard oil casing and oil and gas pipes, steel casing pipes and special pipes for mechanical equipment, which have high quality requirements. These kinds of steel pipes not only have strict requirements on steel grade and weld quality, but also have high requirements on straightness of steel pipes. Because the deviation of straightness is directly related to the processing, connection, and distortion of the pipe end threads and pipe collars of the oil casing and delivery pipe, as well as the distortion and deformation of the pipe during use.
Bending is the effect of the internal stress of the steel pipe. Simply put, bending is an imbalance of stress.
Steel pipe straightening adjustment principle:
1. The pipe is bent in the same direction as the weld seam
Reason: Insufficient normalizing treatment of the weld seam, thermal stress exists on the side of the pipe near the weld seam, so it bends in one direction after cooling.
Solution: (1) Adjust the middle roller and increase the deflection curve appropriately. (2) Straighten twice. (3) When it cannot be straightened directly, temper the pipe as a whole.
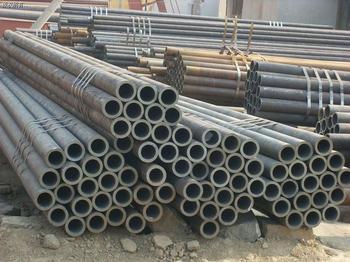
2. The pipe is bent irregularly
Reasons: (1) The pressure between the three rollers is inconsistent; (2) The wear of the straightening roller is relatively large
Solution: Check and adjust whether the upper straightening roller is loose, and use a sample stick to straighten the length of the contact line between the three lines.
3. The length of the pipe is shortened greatly
Reasons: (1) The rolling angle difference between the three straightening rollers is too large; (2) The straightening pressure is relatively large.
Solutions: (1) Adjust the radial pressure angle to be as consistent as possible; (2) Adjust the straightening pressure appropriately.
4. One end of the pipe is bent
Cause: The distance between the rollers is too large.
Solution: Choose a straightening machine with a smaller spacing suitable for the corresponding pipe diameter.
5. The head of the pipe is not round
Reason: The contact phase between the three straightening rollers is improperly distributed or overlapped, and the roller pressure is too large.
Solution: Properly adjust the angle between the rollers and adjust the pressure of the rollers on the pipe.
Bending is the effect of the internal stress of the steel pipe. Simply put, bending is an imbalance of stress.
Steel pipe straightening adjustment principle:
1. The pipe is bent in the same direction as the weld seam
Reason: Insufficient normalizing treatment of the weld seam, thermal stress exists on the side of the pipe near the weld seam, so it bends in one direction after cooling.
Solution: (1) Adjust the middle roller and increase the deflection curve appropriately. (2) Straighten twice. (3) When it cannot be straightened directly, temper the pipe as a whole.
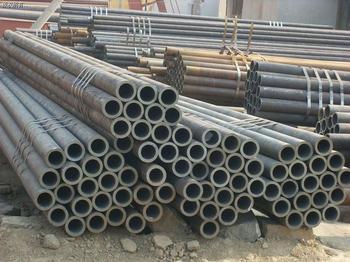
2. The pipe is bent irregularly
Reasons: (1) The pressure between the three rollers is inconsistent; (2) The wear of the straightening roller is relatively large
Solution: Check and adjust whether the upper straightening roller is loose, and use a sample stick to straighten the length of the contact line between the three lines.
3. The length of the pipe is shortened greatly
Reasons: (1) The rolling angle difference between the three straightening rollers is too large; (2) The straightening pressure is relatively large.
Solutions: (1) Adjust the radial pressure angle to be as consistent as possible; (2) Adjust the straightening pressure appropriately.
4. One end of the pipe is bent
Cause: The distance between the rollers is too large.
Solution: Choose a straightening machine with a smaller spacing suitable for the corresponding pipe diameter.
5. The head of the pipe is not round
Reason: The contact phase between the three straightening rollers is improperly distributed or overlapped, and the roller pressure is too large.
Solution: Properly adjust the angle between the rollers and adjust the pressure of the rollers on the pipe.