Decarburization is a phenomenon in which the surface carbon content of steel pipes (such as CS seamless pipes and welded steel tubes) decreases during heat treatment. The essence of decarburization is that the carbon atoms in the steel pipe react with the furnace atmosphere such as hydrogen or oxygen at high temperature to form methane or carbon monoxide.
Decarburization is the result of mutual diffusion between atoms during heat treatment. On the one hand, oxygen diffuses into the steel; on the other hand, carbon in the steel diffuses outward. The decarburization layer can only form when the rate of decarburization exceeds the rate of oxidation. When the oxidation rate is very high, no obvious decarburization phenomenon may occur, that is, iron is oxidized to form scale after the decarburization layer is formed. Therefore, a deep decarburized layer can be formed in an atmosphere with relatively weak oxidation.
The decarburization layer of steel pipe includes two parts: full decarburization layer and partial decarburization layer (transition layer). Partially decarburized layer refers to the structure where the steel carbon content is normal after the fully decarburized layer. In the case of not serious decarburization, sometimes only a part of the decarburization layer can be seen without a full decarburization layer.
The depth of the decarburization layer can be measured by various methods according to the changes of decarburization components, structures and properties. In the actual heat treatment production, it is most common to measure the decarburization layer of steel by metallographic method.
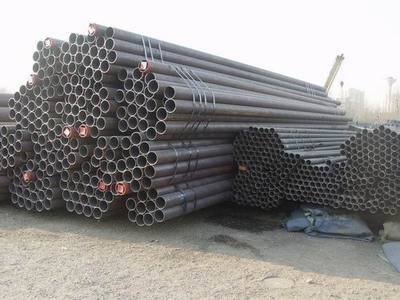
Countermeasures to prevent decarbonization mainly include the following aspects:
1) When the steel pipe is heated, the heating temperature and the residence time at high temperature should be reduced as much as possible; the heating speed should be reasonably selected to shorten the total heating time;
2) Control the appropriate heating atmosphere to make it appear neutral or use protective gas to heat;
3) During hot press processing, if the production is interrupted due to some accidental factors, the furnace temperature should be lowered to wait for the production to resume. If the pause time is very long, the billet should be taken out of the furnace or cooled with the furnace;
4) Reduce the number of intermediate annealing and the temperature of intermediate annealing as much as possible during cold deformation, or replace high temperature annealing with softening tempering. When performing intermediate annealing or softening and tempering, heating should be carried out in a protective medium;
5) When heating at high temperature, the surface of the steel is protected by covering and coating to prevent oxidation and decarburization;
6) Correct heat treatment process operation and increase the processing allowance of the steel pipe so that the decarburization layer can be completely removed during processing.
Decarburization is the result of mutual diffusion between atoms during heat treatment. On the one hand, oxygen diffuses into the steel; on the other hand, carbon in the steel diffuses outward. The decarburization layer can only form when the rate of decarburization exceeds the rate of oxidation. When the oxidation rate is very high, no obvious decarburization phenomenon may occur, that is, iron is oxidized to form scale after the decarburization layer is formed. Therefore, a deep decarburized layer can be formed in an atmosphere with relatively weak oxidation.
The decarburization layer of steel pipe includes two parts: full decarburization layer and partial decarburization layer (transition layer). Partially decarburized layer refers to the structure where the steel carbon content is normal after the fully decarburized layer. In the case of not serious decarburization, sometimes only a part of the decarburization layer can be seen without a full decarburization layer.
The depth of the decarburization layer can be measured by various methods according to the changes of decarburization components, structures and properties. In the actual heat treatment production, it is most common to measure the decarburization layer of steel by metallographic method.
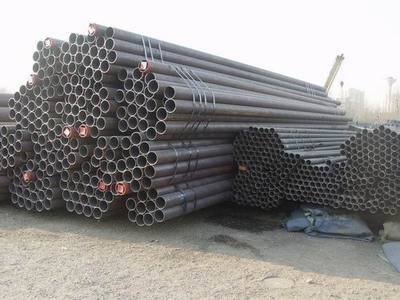
Countermeasures to prevent decarbonization mainly include the following aspects:
1) When the steel pipe is heated, the heating temperature and the residence time at high temperature should be reduced as much as possible; the heating speed should be reasonably selected to shorten the total heating time;
2) Control the appropriate heating atmosphere to make it appear neutral or use protective gas to heat;
3) During hot press processing, if the production is interrupted due to some accidental factors, the furnace temperature should be lowered to wait for the production to resume. If the pause time is very long, the billet should be taken out of the furnace or cooled with the furnace;
4) Reduce the number of intermediate annealing and the temperature of intermediate annealing as much as possible during cold deformation, or replace high temperature annealing with softening tempering. When performing intermediate annealing or softening and tempering, heating should be carried out in a protective medium;
5) When heating at high temperature, the surface of the steel is protected by covering and coating to prevent oxidation and decarburization;
6) Correct heat treatment process operation and increase the processing allowance of the steel pipe so that the decarburization layer can be completely removed during processing.