Angle steel, also known as angle iron due to its unique "L"-shaped cross-section, is an important steel material widely used in various fields. However, angle steel will inevitably suffer from various erosions during use. In a humid environment, it is easy to rust; in an industrial environment with a lot of chemical substances, it may be corroded. These problems not only affect the appearance, but also weaken the performance of the angle steel and shorten its service life. Therefore, in order to keep the angle steel in good performance in different environments and extend its service life, surface treatment is extremely critical. Next, we will introduce several common and practical angle steel surface treatment methods in detail.
1. Hot dip galvanizing
Principle: Immerse the angle steel in molten zinc liquid to form a zinc-iron alloy layer and a pure zinc layer on the surface of the angle steel, thereby playing an anti-corrosion role.
Advantages: The hot-dip galvanized layer has good corrosion resistance, can effectively prevent the corrosion of the angle steel in the atmospheric environment, water and other media, and has a long service life. Moreover, the zinc layer has strong adhesion and is not easy to fall off.
Disadvantages: The hot-dip galvanizing process may have a certain impact on the size and surface flatness of the angle steel, and the cost is relatively high.
Application scenarios: Widely used in construction, electricity, transportation and other fields, such as angle steel brackets in building structures, iron towers in transmission lines, etc.
Principle: Through electrolysis, a layer of zinc is deposited on the surface of the angle steel.
Advantages: The surface of the electrogalvanized layer is smooth and uniform, and a thinner zinc layer can be obtained, which is suitable for occasions with high requirements for appearance. At the same time, electrogalvanizing has high production efficiency and relatively low cost.
Disadvantages: The corrosion resistance of the electrogalvanized layer is not as good as that of the hot-dip galvanized layer, and its protection performance in harsh environments is poor.
Application scenarios: Commonly used in some fields that do not require high corrosion resistance but have high requirements for appearance quality, such as furniture, decoration and other industries.
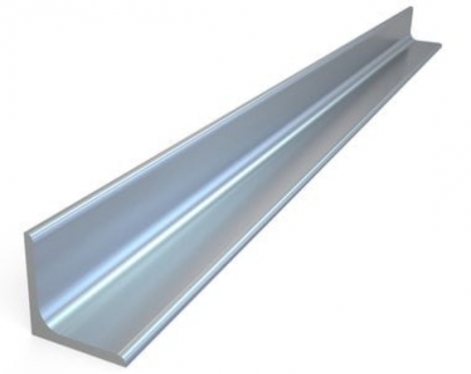
Advantages: The paint has a rich selection of colors and can be customized according to needs, with good decorative properties. At the same time, the painting process is simple and the cost is low.
Disadvantages: The adhesion and corrosion resistance of the paint layer are relatively poor, and regular maintenance and renewal are required. When exposed to harsh environments for a long time, the paint is easy to fall off and age.
Application scenarios: Suitable for some occasions that do not require high corrosion resistance but have requirements for aesthetics, such as interior decoration, general mechanical housing, etc.
Principle: Plastic powder is adsorbed on the surface of the angle steel by electrostatic spraying, and then baked at high temperature to solidify the powder to form a layer of plastic coating.
Advantages: The plastic spray coating has good corrosion resistance, wear resistance and decorative properties, the coating thickness is uniform, and it is not easy to have defects such as sagging and blistering.
Disadvantages: The plastic spraying process has high requirements for surface treatment and the cost is relatively high. In a high temperature environment, the plastic coating may deform, age and other problems.
Application scenarios: Commonly used in building doors and windows, guardrails and other fields, which can provide good protection performance and meet the requirements of aesthetics.
Principle: A layer of phosphate conversion film is formed on the surface of the angle steel through chemical reaction to improve the corrosion resistance of the angle steel and the adhesion of the paint.
Advantages: The phosphate film has good corrosion resistance and lubricity, and can improve the wear resistance and anti-adhesion of the angle steel. At the same time, phosphating can improve the adhesion of subsequent painting or plastic coating and extend the service life of the coating.
Disadvantages: The surface color of the angle steel after phosphating is darker, generally gray or black, which has a certain impact on the appearance. In addition, a certain amount of wastewater and waste residue will be generated during the phosphating process, which requires environmental protection treatment.
Application scenarios: Commonly used in machinery manufacturing, automotive industry and other fields as a pretreatment process before painting or plastic coating to improve the quality and durability of the coating.
Conclusion
There are many different surface treatment methods for angle steel, each with its own advantages. In practical applications, we need to comprehensively consider factors such as the specific use environment, cost budget, and aesthetic requirements, and accurately select the appropriate surface treatment method. Only in this way can we give full play to the performance advantages of angle steel, improve its durability and aesthetics, and allow angle steel to show its maximum value in various engineering projects.
Read more: Will Angle Steel Rust?
1. Hot dip galvanizing
Principle: Immerse the angle steel in molten zinc liquid to form a zinc-iron alloy layer and a pure zinc layer on the surface of the angle steel, thereby playing an anti-corrosion role.
Advantages: The hot-dip galvanized layer has good corrosion resistance, can effectively prevent the corrosion of the angle steel in the atmospheric environment, water and other media, and has a long service life. Moreover, the zinc layer has strong adhesion and is not easy to fall off.
Disadvantages: The hot-dip galvanizing process may have a certain impact on the size and surface flatness of the angle steel, and the cost is relatively high.
Application scenarios: Widely used in construction, electricity, transportation and other fields, such as angle steel brackets in building structures, iron towers in transmission lines, etc.
2. Electrogalvanizing
Principle: Through electrolysis, a layer of zinc is deposited on the surface of the angle steel.
Advantages: The surface of the electrogalvanized layer is smooth and uniform, and a thinner zinc layer can be obtained, which is suitable for occasions with high requirements for appearance. At the same time, electrogalvanizing has high production efficiency and relatively low cost.
Disadvantages: The corrosion resistance of the electrogalvanized layer is not as good as that of the hot-dip galvanized layer, and its protection performance in harsh environments is poor.
Application scenarios: Commonly used in some fields that do not require high corrosion resistance but have high requirements for appearance quality, such as furniture, decoration and other industries.
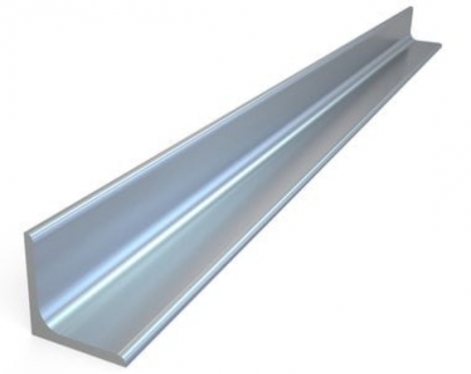
3. Painting
Principle: Paint is applied to the surface of the angle steel to form a protective film to isolate the contact between the angle steel and corrosive media such as air and water.Advantages: The paint has a rich selection of colors and can be customized according to needs, with good decorative properties. At the same time, the painting process is simple and the cost is low.
Disadvantages: The adhesion and corrosion resistance of the paint layer are relatively poor, and regular maintenance and renewal are required. When exposed to harsh environments for a long time, the paint is easy to fall off and age.
Application scenarios: Suitable for some occasions that do not require high corrosion resistance but have requirements for aesthetics, such as interior decoration, general mechanical housing, etc.
4. Plastic spraying
Principle: Plastic powder is adsorbed on the surface of the angle steel by electrostatic spraying, and then baked at high temperature to solidify the powder to form a layer of plastic coating.
Advantages: The plastic spray coating has good corrosion resistance, wear resistance and decorative properties, the coating thickness is uniform, and it is not easy to have defects such as sagging and blistering.
Disadvantages: The plastic spraying process has high requirements for surface treatment and the cost is relatively high. In a high temperature environment, the plastic coating may deform, age and other problems.
Application scenarios: Commonly used in building doors and windows, guardrails and other fields, which can provide good protection performance and meet the requirements of aesthetics.
5. Phosphating
Principle: A layer of phosphate conversion film is formed on the surface of the angle steel through chemical reaction to improve the corrosion resistance of the angle steel and the adhesion of the paint.
Advantages: The phosphate film has good corrosion resistance and lubricity, and can improve the wear resistance and anti-adhesion of the angle steel. At the same time, phosphating can improve the adhesion of subsequent painting or plastic coating and extend the service life of the coating.
Disadvantages: The surface color of the angle steel after phosphating is darker, generally gray or black, which has a certain impact on the appearance. In addition, a certain amount of wastewater and waste residue will be generated during the phosphating process, which requires environmental protection treatment.
Application scenarios: Commonly used in machinery manufacturing, automotive industry and other fields as a pretreatment process before painting or plastic coating to improve the quality and durability of the coating.
Conclusion
There are many different surface treatment methods for angle steel, each with its own advantages. In practical applications, we need to comprehensively consider factors such as the specific use environment, cost budget, and aesthetic requirements, and accurately select the appropriate surface treatment method. Only in this way can we give full play to the performance advantages of angle steel, improve its durability and aesthetics, and allow angle steel to show its maximum value in various engineering projects.
Read more: Will Angle Steel Rust?