Tension reduction rolling is the last hot rolling process in the production of seamless steel pipes, which plays a decisive role in the control of product quality. The tension reduction of seamless steel pipe is a continuous rolling process without mandrel. During the rolling process, the outer diameter and wall thickness of the rolled piece are changed by the radial pressure of the roll.The axial direction is affected by the friction force of the roll, which changes the wall thickness, and is also affected by various factors such as tangential stress and temperature changes.
Advantages of steel pipe tension reduction
(1) Reduce the specifications of the required tube blanks and improve the production efficiency of the tube rolling unit. The pipe rolling unit only produces a few specifications, and after tension reduction, various specifications of finished steel pipes can be obtained.
(2) It can reduce the number of production tools in the front process and improve the operation rate of the unit. Due to the reduction in the specifications of broken and obsolete pipes, tools, spare parts and replacement time are greatly reduced, and production is more stable, thereby increasing the operation time.
(3) The varieties and specifications can be expanded. The diameter reduction is as high as 80% and the wall reduction is up to 45%. Small diameter seamless steel pipes can be directly produced through tension reduction.
(4) The elongation coefficient of tension reduction is 6-9, which can produce steel pipes up to 165m.
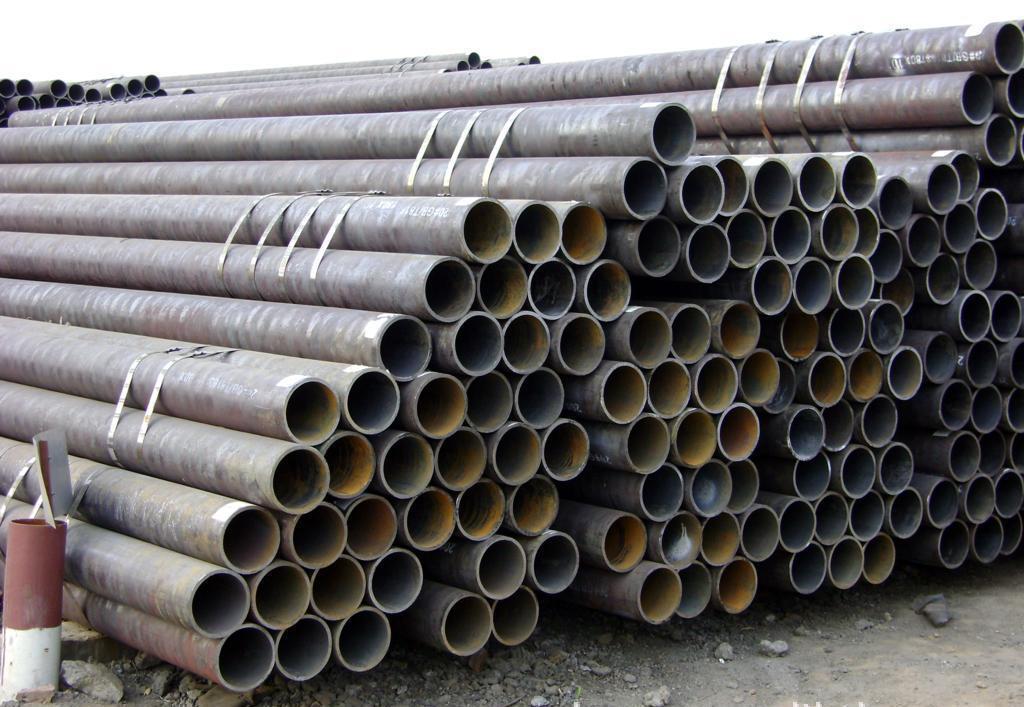
The process principle of steel pipe sizing and reducing
(1) Flattening. When biting in, local point contact is caused due to the incompatibility between the shape of the hole and the cross section of the capillary tube. The flattening starts here first.The characteristic is that only the shape of the section changes, and the circumference, thickness and thickness do not change, and there is no extension.
(2) Diameter reduction, with the development of flattening, the contact surface between the pass wall and the rolling piece increases continuously, and begins to reduce diameter under the action of radial contact stress to a certain extent. The characteristic is that the average diameter is reduced, the capillary tube is extended, and the wall thickness is increased or decreased. Because the resistance of the metal to flow in the radial direction at the opening of the hole is small, the wall thickness here is larger than that at the bottom of the groove, and the uneven wall thickness on the cross section begins to appear. For tension reduction, not only diameter reduction, but also wall reduction, greatly extending.
Due to the complexity of the tension reduction rolling process, it is easy to cause many kinds of product defects. Therefore, in the production process of the reducer, special attention should be paid to the formulation of the reducer process, especially the reduction rate and tension coefficient of a single frame should not be too large.The roundness coefficient should be matched with the reduction rate of the single frame to avoid the occurrence of steel pipe defects.
Advantages of steel pipe tension reduction
(1) Reduce the specifications of the required tube blanks and improve the production efficiency of the tube rolling unit. The pipe rolling unit only produces a few specifications, and after tension reduction, various specifications of finished steel pipes can be obtained.
(2) It can reduce the number of production tools in the front process and improve the operation rate of the unit. Due to the reduction in the specifications of broken and obsolete pipes, tools, spare parts and replacement time are greatly reduced, and production is more stable, thereby increasing the operation time.
(3) The varieties and specifications can be expanded. The diameter reduction is as high as 80% and the wall reduction is up to 45%. Small diameter seamless steel pipes can be directly produced through tension reduction.
(4) The elongation coefficient of tension reduction is 6-9, which can produce steel pipes up to 165m.
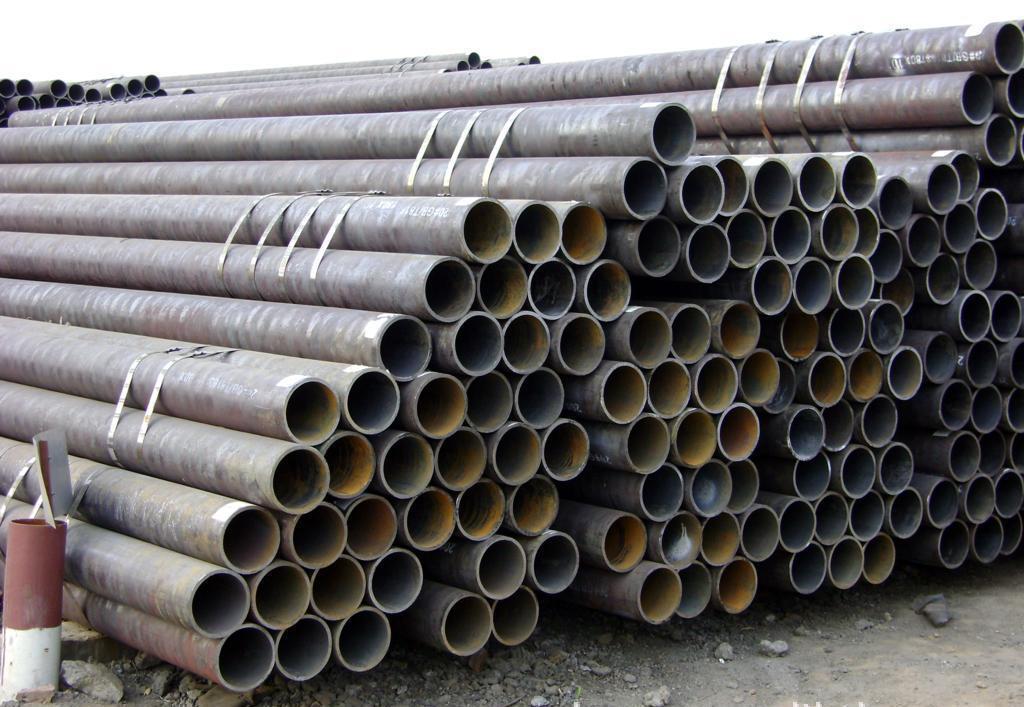
The process principle of steel pipe sizing and reducing
(1) Flattening. When biting in, local point contact is caused due to the incompatibility between the shape of the hole and the cross section of the capillary tube. The flattening starts here first.The characteristic is that only the shape of the section changes, and the circumference, thickness and thickness do not change, and there is no extension.
(2) Diameter reduction, with the development of flattening, the contact surface between the pass wall and the rolling piece increases continuously, and begins to reduce diameter under the action of radial contact stress to a certain extent. The characteristic is that the average diameter is reduced, the capillary tube is extended, and the wall thickness is increased or decreased. Because the resistance of the metal to flow in the radial direction at the opening of the hole is small, the wall thickness here is larger than that at the bottom of the groove, and the uneven wall thickness on the cross section begins to appear. For tension reduction, not only diameter reduction, but also wall reduction, greatly extending.
Due to the complexity of the tension reduction rolling process, it is easy to cause many kinds of product defects. Therefore, in the production process of the reducer, special attention should be paid to the formulation of the reducer process, especially the reduction rate and tension coefficient of a single frame should not be too large.The roundness coefficient should be matched with the reduction rate of the single frame to avoid the occurrence of steel pipe defects.