Mechanical properties are an important indicator to ensure the end-use performance of seamless steel pipes, which depend on the chemical composition and heat treatment system of the steel. In the standard of seamless steel pipe, according to different application requirements, the tensile properties (tensile strength, yield strength and yield point, elongation), hardness, toughness index, and high and low temperature performance required by users are specified.
(1) Tensile strength (Rm). During the stretching process, the stress obtained by dividing the maximum force (Fm) that the sample bears when it breaks by the original cross-sectional area (So) of the sample is called the tensile strength (Rm). It represents the maximum ability of metal materials to resist damage under tension.
(2) Yield point. For metal materials with yield phenomenon, the stress at which the sample can continue to elongate without increasing the force during the stretching process is called the yield point. If the force drops, the upper and lower yield points should be distinguished. The unit of yield point is N/mnA2 (MPa).
(3) Elongation after break (A). In the tensile test, the percentage of the increased length of the gauge length after the sample is broken to the original gauge length is called the elongation.
(4) Reduction of area (Z). In the tensile test, the percentage of the maximum reduction of the cross-sectional area at the reduced diameter of the sample after the sample is broken and the original cross-sectional area is called the reduction of area.
(5) Hardness index. The ability of metal materials to resist the indentation of the surface by hard objects is called hardness. According to different test methods and scope of application, hardness can be divided into Brinell hardness, Rockwell hardness, Vickers hardness, Shore hardness, microhardness and high temperature hardness.
(6) Impact toughness index. Impact toughness is the resistance of metal materials to external impact loads, generally expressed by impact energy (Ak), and its unit is J (joule). The impact energy test is divided into three types: normal temperature, low temperature and high temperature impact test due to different test temperatures.
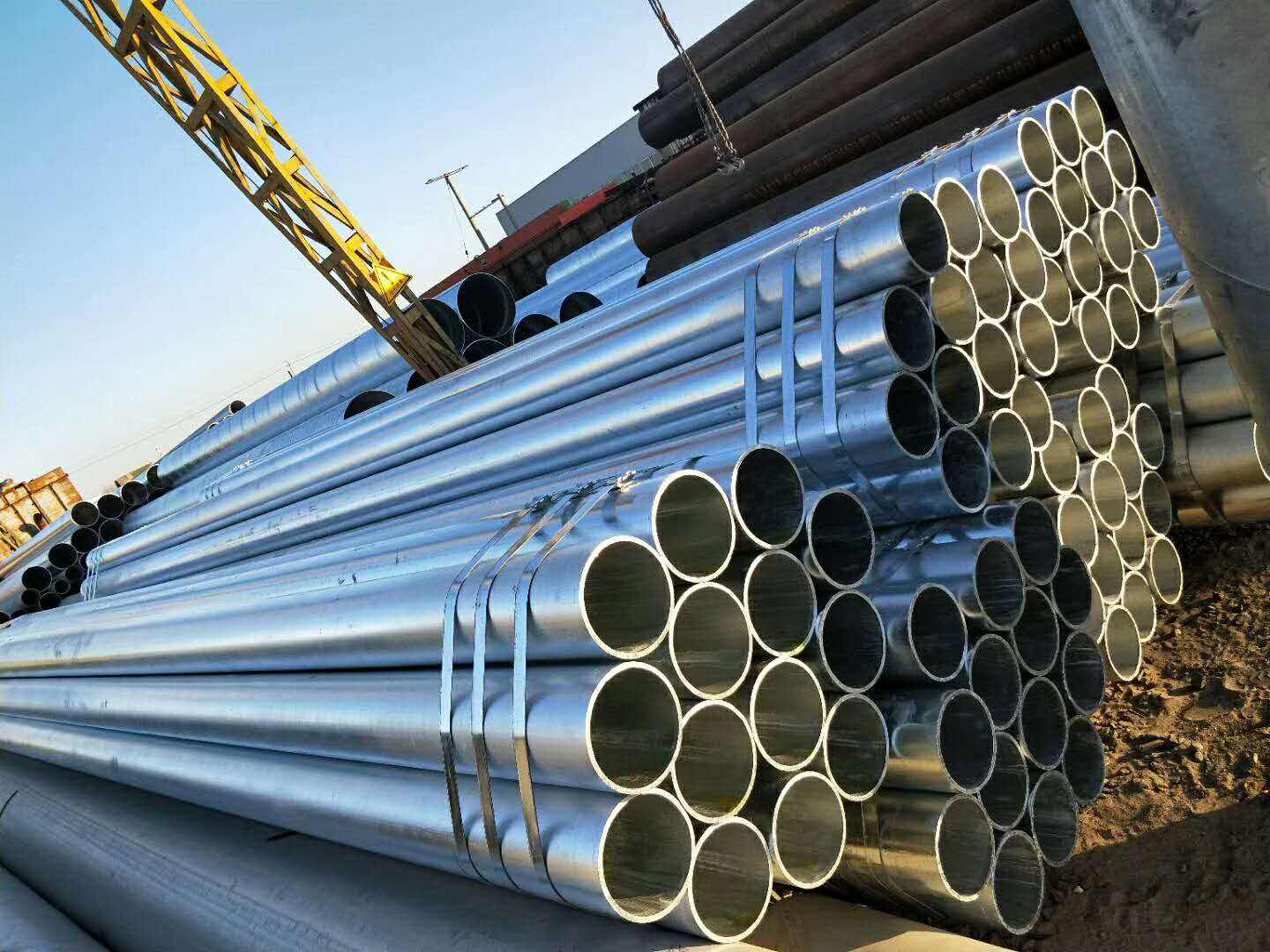
Chemical composition of seamless steel pipe
The chemical composition of the seamless steel pipe is one of the important factors related to the quality and end-use performance of the steel pipe, and even the main basis for the heat treatment system of the final product.
(1) The melting composition of steel. The chemical composition specified in the general standard refers to the smelting composition. It refers to the chemical composition of steel after smelting and mid-casting. In order to make it representative, that is, represent the average composition of the furnace or tank, it is stipulated in the sampling standard method:The molten steel is cast into a small ingot in the sample mold, and the sample chip is created or drilled on it, and analyzed according to the specified standard method.
2) Finished product composition. Also known as the acceptance analysis composition, it is the chemical composition obtained by drilling or creating sampling chips from the finished steel according to the specified method, and analyzing it according to the specified standard method. During the crystallization and subsequent plastic deformation of steel, due to the uneven distribution of alloying elements in the steel, there is a deviation between the composition of the finished product and the standard composition range.
(1) Tensile strength (Rm). During the stretching process, the stress obtained by dividing the maximum force (Fm) that the sample bears when it breaks by the original cross-sectional area (So) of the sample is called the tensile strength (Rm). It represents the maximum ability of metal materials to resist damage under tension.
(2) Yield point. For metal materials with yield phenomenon, the stress at which the sample can continue to elongate without increasing the force during the stretching process is called the yield point. If the force drops, the upper and lower yield points should be distinguished. The unit of yield point is N/mnA2 (MPa).
(3) Elongation after break (A). In the tensile test, the percentage of the increased length of the gauge length after the sample is broken to the original gauge length is called the elongation.
(4) Reduction of area (Z). In the tensile test, the percentage of the maximum reduction of the cross-sectional area at the reduced diameter of the sample after the sample is broken and the original cross-sectional area is called the reduction of area.
(5) Hardness index. The ability of metal materials to resist the indentation of the surface by hard objects is called hardness. According to different test methods and scope of application, hardness can be divided into Brinell hardness, Rockwell hardness, Vickers hardness, Shore hardness, microhardness and high temperature hardness.
(6) Impact toughness index. Impact toughness is the resistance of metal materials to external impact loads, generally expressed by impact energy (Ak), and its unit is J (joule). The impact energy test is divided into three types: normal temperature, low temperature and high temperature impact test due to different test temperatures.
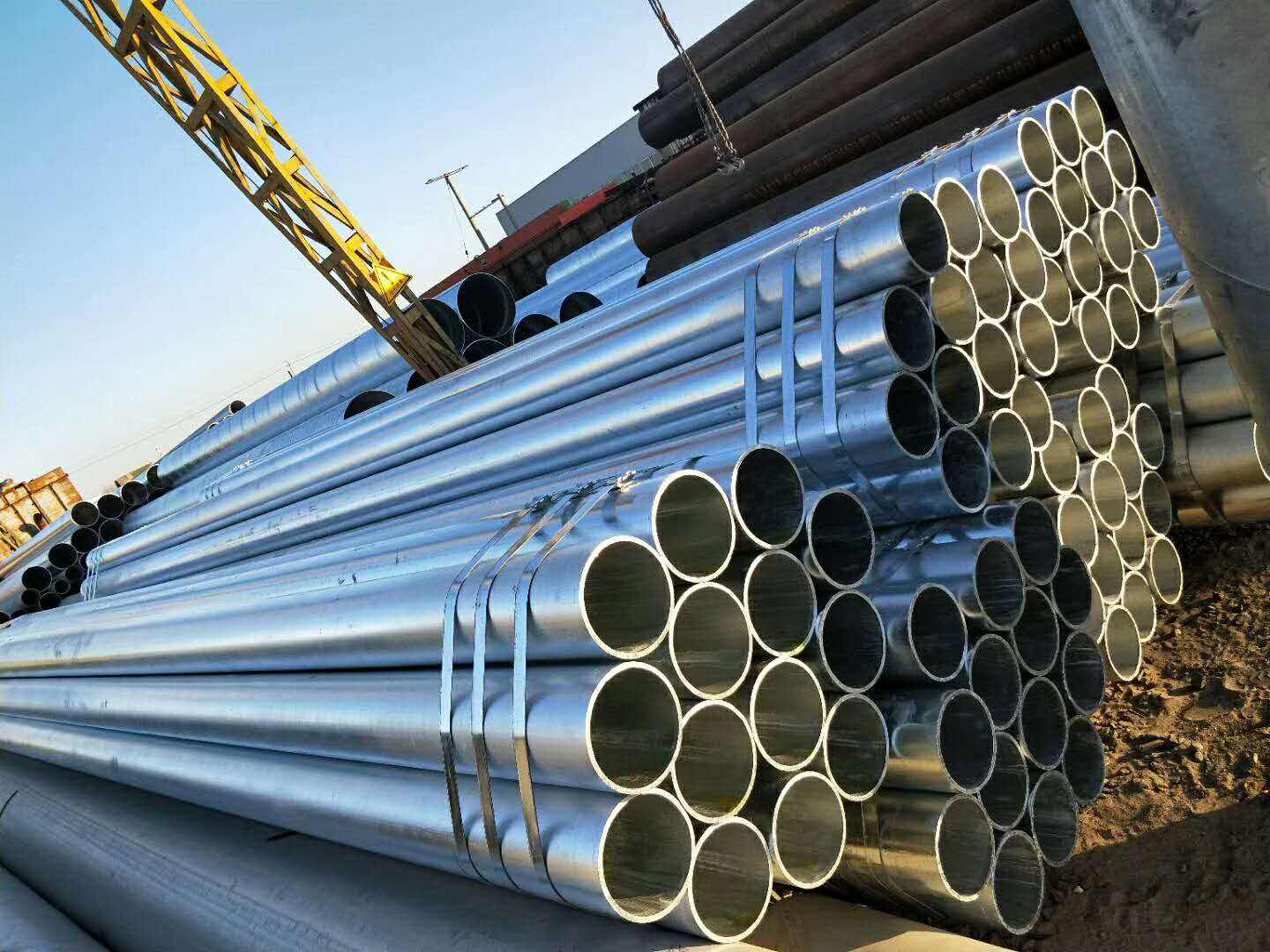
Chemical composition of seamless steel pipe
The chemical composition of the seamless steel pipe is one of the important factors related to the quality and end-use performance of the steel pipe, and even the main basis for the heat treatment system of the final product.
(1) The melting composition of steel. The chemical composition specified in the general standard refers to the smelting composition. It refers to the chemical composition of steel after smelting and mid-casting. In order to make it representative, that is, represent the average composition of the furnace or tank, it is stipulated in the sampling standard method:The molten steel is cast into a small ingot in the sample mold, and the sample chip is created or drilled on it, and analyzed according to the specified standard method.
2) Finished product composition. Also known as the acceptance analysis composition, it is the chemical composition obtained by drilling or creating sampling chips from the finished steel according to the specified method, and analyzing it according to the specified standard method. During the crystallization and subsequent plastic deformation of steel, due to the uneven distribution of alloying elements in the steel, there is a deviation between the composition of the finished product and the standard composition range.