Oil casing (octg pipe) is a steel pipe used to support the walls of oil and gas wells to ensure the normal operation of the entire oil well after the drilling process and completion. Each well uses several layers of casing according to different drilling depths and geological conditions. Cement cementing is used after the casing is lowered into the well. Unlike oil pipes and drill pipes, it cannot be reused and is a one-time consumable material. Therefore, the consumption of casing accounts for more than 70% of all oil well pipes.
Due to factors such as selection, quality, transportation, storage, and use, casing damage occurs from time to time, resulting in production reduction or even scrapping of oil and gas wells, which brings significant economic losses to oil and gas field enterprises. The following is an analysis of the quality control of the transportation and storage stages of the oil casing.
1. Pipe transportation link
After the pipes are signed by the factory supervisors and approved by the user, they will be loaded and sent by the manufacturer. The key control points are as follows.
(1) During the loading, unloading and transportation of pipes, knocking, bumping and impact damage should be avoided.
(2) It is not allowed to hang the pipe directly on the thread protector with the hook, and the sling should be used for loading and unloading.
(3) The pipes should be firmly fixed before transportation, and there should be no movement between the pipes, the pipes and the carriage.
(4) In principle, the length of the pipe should not exceed the length of the vehicle compartment by 1 meter. If the pipe body is too long, it will increase the possibility of slipping and bending and deformation due to up and down bumps.
(5) Sudden braking should be avoided during transportation to avoid pipe body and thread damage caused by back and forth movement and collision of the pipe body.
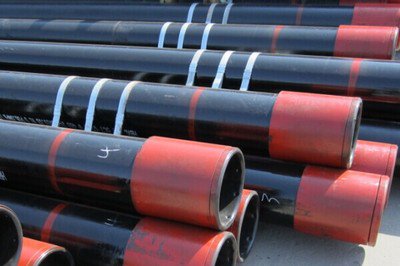
2. Pipe storage link
There are two acceptance and inspection procedures before warehousing, warehouse management personnel data review and appearance quality inspection and product quality sampling inspection by the testing department. Only pipes that pass the inspection can be put into storage. The key control points are as follows.
(1) Preliminary inspection of warehouse personnel. It is mainly to check whether the pipes meet the contract and order requirements; check whether the handover list, pipe material list, furnace batch number and material list, product quality certificate, and signature of the factory supervisor are complete, qualified, and valid. Check whether the appearance, quantity and specifications of the physical objects are intact and accurate.
(2) Sampling inspection by the testing department. Each user unit proposes a test plan according to the arrival situation, and the company's professional management department implements the key points or special circumstances according to the test-related requirements. The detection of key wells, special wells or special pipes that can expand the detection ratio must be carried out by qualified and authoritative testing institutions, and sampling physical and chemical tests are required.
3. Pipe storage link
After warehousing, arrange them neatly according to the regulations, so that the accounts are consistent and the accounts are consistent. The quality control points are as follows.
(1) The stacking needs to ensure the convenience of the next hoisting operation, and it is best to stack them in a cross stack.
(2) It needs to be stacked on the pipe rack. The pipe rack is recommended to be more than 50cm away from the ground. It is forbidden to stack the pipes directly on the ground, so as to avoid corrosion of the pipe body or thread due to rain soaking.
(3) The thread protector must be kept intact, tightened in place, and the thread must be coated with thread grease.
(4) Keep the paint color and marking of the pipe body intact.
4. Pipe delivery link
Pipe requisitioning implements the approval procedures for materials out of the warehouse, and makes corresponding records. The key control points are as follows.
(1) Loading, unloading, hoisting, and transportation control points are consistent with Article 1.
(2) Ensure that the quantity and specifications of the pipes issued are consistent with the requisition list. Mixing is strictly prohibited.
Due to factors such as selection, quality, transportation, storage, and use, casing damage occurs from time to time, resulting in production reduction or even scrapping of oil and gas wells, which brings significant economic losses to oil and gas field enterprises. The following is an analysis of the quality control of the transportation and storage stages of the oil casing.
1. Pipe transportation link
After the pipes are signed by the factory supervisors and approved by the user, they will be loaded and sent by the manufacturer. The key control points are as follows.
(1) During the loading, unloading and transportation of pipes, knocking, bumping and impact damage should be avoided.
(2) It is not allowed to hang the pipe directly on the thread protector with the hook, and the sling should be used for loading and unloading.
(3) The pipes should be firmly fixed before transportation, and there should be no movement between the pipes, the pipes and the carriage.
(4) In principle, the length of the pipe should not exceed the length of the vehicle compartment by 1 meter. If the pipe body is too long, it will increase the possibility of slipping and bending and deformation due to up and down bumps.
(5) Sudden braking should be avoided during transportation to avoid pipe body and thread damage caused by back and forth movement and collision of the pipe body.
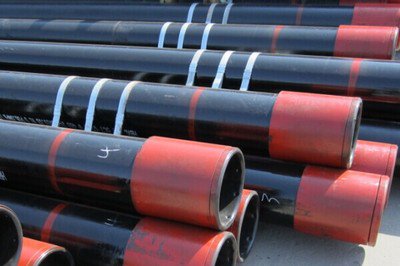
2. Pipe storage link
There are two acceptance and inspection procedures before warehousing, warehouse management personnel data review and appearance quality inspection and product quality sampling inspection by the testing department. Only pipes that pass the inspection can be put into storage. The key control points are as follows.
(1) Preliminary inspection of warehouse personnel. It is mainly to check whether the pipes meet the contract and order requirements; check whether the handover list, pipe material list, furnace batch number and material list, product quality certificate, and signature of the factory supervisor are complete, qualified, and valid. Check whether the appearance, quantity and specifications of the physical objects are intact and accurate.
(2) Sampling inspection by the testing department. Each user unit proposes a test plan according to the arrival situation, and the company's professional management department implements the key points or special circumstances according to the test-related requirements. The detection of key wells, special wells or special pipes that can expand the detection ratio must be carried out by qualified and authoritative testing institutions, and sampling physical and chemical tests are required.
3. Pipe storage link
After warehousing, arrange them neatly according to the regulations, so that the accounts are consistent and the accounts are consistent. The quality control points are as follows.
(1) The stacking needs to ensure the convenience of the next hoisting operation, and it is best to stack them in a cross stack.
(2) It needs to be stacked on the pipe rack. The pipe rack is recommended to be more than 50cm away from the ground. It is forbidden to stack the pipes directly on the ground, so as to avoid corrosion of the pipe body or thread due to rain soaking.
(3) The thread protector must be kept intact, tightened in place, and the thread must be coated with thread grease.
(4) Keep the paint color and marking of the pipe body intact.
4. Pipe delivery link
Pipe requisitioning implements the approval procedures for materials out of the warehouse, and makes corresponding records. The key control points are as follows.
(1) Loading, unloading, hoisting, and transportation control points are consistent with Article 1.
(2) Ensure that the quantity and specifications of the pipes issued are consistent with the requisition list. Mixing is strictly prohibited.