Influence and Control Method of Water Quenching Deformation of Steel Pipe
1. Influencing factors
Water quenching is a very common quenching agent for heat treatment of steel pipes (seamless pipes or welded pipes), which can rapidly reduce the temperature during high-temperature treatment to achieve cooling of steel pipe metal. But it is precisely because of this approach that the stress of the tissue changes during the cooling process, resulting in deformation problems. For example, the center line cannot be adjusted in time during water quenching, which causes misalignment between the idlers, nozzles and steel pipes. Or the distance between the inner nozzle and the pipe cannot be reasonably controlled. Once it exceeds the standard value, it will cause external spraying and interfere with the water spraying effect outside the pipe end. And if the distance between the two is too small, it will cause the water spray to be too concentrated and deformed. Not only that, there may also be "innate" defects in the design of the water quenching nozzle. For example, the flow rate of the internal spray does not meet the production standards, and the sprayed water volume is not enough to achieve the cooling effect. The delay design of the outer shower also fails to form a good cooperative relationship with the inner spray, which will also cause counterproductive effects.
2. Control method
In view of the deformation problem that is prone to occur in the water quenching process, technicians should focus on the control of water spraying. First of all, before water quenching, the position of the nozzle, roller and steel pipe should be adjusted to ensure that the error of the center line is less than 1mm. When installing the nozzle, it is necessary to refer to the position of the steel pipe, and the error also needs to be controlled within 2 mm. Secondly, technicians should also judge the rationality of the water quenching nozzle through multiple tests. If problems are found in the test, they can be adjusted in time to avoid more serious quality problems.
In addition, the cooperation with the outer shower should be considered when installing the nozzle. Generally speaking, the outer shower needs to spray water about 3 seconds in advance to make the outer structure of the steel pipe cool first. At this time, the inner spray can ensure that the overall straightness does not deviate. In terms of nozzle flow rate, it is also necessary to make it not less than 10m/s to achieve better cooling effect.
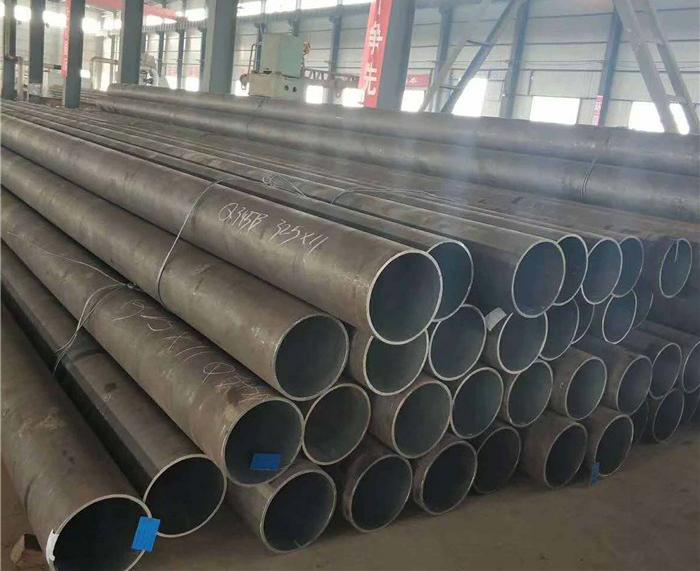
Optimization measures:
1) Reduce the quenching heating temperature of the steel pipe to 880°C to reduce the temperature stress.
2) Appropriately reduce the pressure of the water pump of the inner nozzle, reduce the flow velocity of water, and thereby reduce tissue stress.
3) Reduce the depth of quenching so that 1/4 of the steel pipes in the circumferential direction are on the water surface and 3/4 of the steel pipes are underwater to reduce tissue stress.
4) Reduce the cooling time of the steel pipe in water, and increase the outlet water temperature of the steel pipe to 120~160°C.
5) Use residual temperature self-tempering to reduce stress concentration.
6) The tempering process is still held at 735°C for 105 minutes.
1. Influencing factors
Water quenching is a very common quenching agent for heat treatment of steel pipes (seamless pipes or welded pipes), which can rapidly reduce the temperature during high-temperature treatment to achieve cooling of steel pipe metal. But it is precisely because of this approach that the stress of the tissue changes during the cooling process, resulting in deformation problems. For example, the center line cannot be adjusted in time during water quenching, which causes misalignment between the idlers, nozzles and steel pipes. Or the distance between the inner nozzle and the pipe cannot be reasonably controlled. Once it exceeds the standard value, it will cause external spraying and interfere with the water spraying effect outside the pipe end. And if the distance between the two is too small, it will cause the water spray to be too concentrated and deformed. Not only that, there may also be "innate" defects in the design of the water quenching nozzle. For example, the flow rate of the internal spray does not meet the production standards, and the sprayed water volume is not enough to achieve the cooling effect. The delay design of the outer shower also fails to form a good cooperative relationship with the inner spray, which will also cause counterproductive effects.
2. Control method
In view of the deformation problem that is prone to occur in the water quenching process, technicians should focus on the control of water spraying. First of all, before water quenching, the position of the nozzle, roller and steel pipe should be adjusted to ensure that the error of the center line is less than 1mm. When installing the nozzle, it is necessary to refer to the position of the steel pipe, and the error also needs to be controlled within 2 mm. Secondly, technicians should also judge the rationality of the water quenching nozzle through multiple tests. If problems are found in the test, they can be adjusted in time to avoid more serious quality problems.
In addition, the cooperation with the outer shower should be considered when installing the nozzle. Generally speaking, the outer shower needs to spray water about 3 seconds in advance to make the outer structure of the steel pipe cool first. At this time, the inner spray can ensure that the overall straightness does not deviate. In terms of nozzle flow rate, it is also necessary to make it not less than 10m/s to achieve better cooling effect.
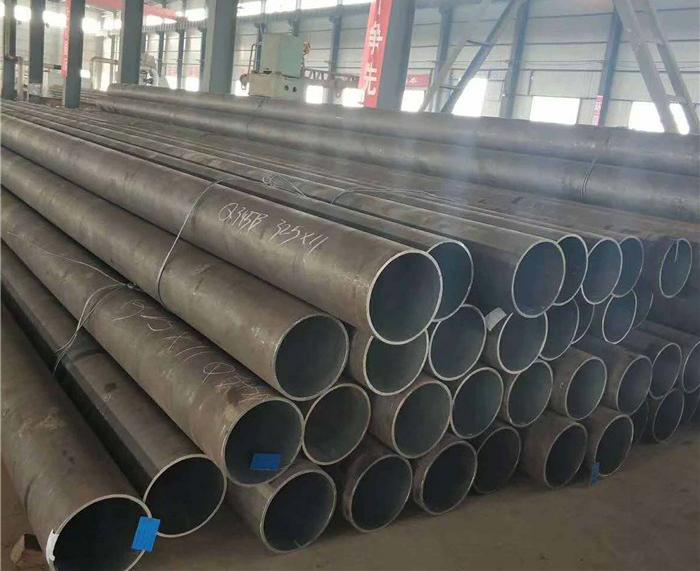
Optimization measures:
1) Reduce the quenching heating temperature of the steel pipe to 880°C to reduce the temperature stress.
2) Appropriately reduce the pressure of the water pump of the inner nozzle, reduce the flow velocity of water, and thereby reduce tissue stress.
3) Reduce the depth of quenching so that 1/4 of the steel pipes in the circumferential direction are on the water surface and 3/4 of the steel pipes are underwater to reduce tissue stress.
4) Reduce the cooling time of the steel pipe in water, and increase the outlet water temperature of the steel pipe to 120~160°C.
5) Use residual temperature self-tempering to reduce stress concentration.
6) The tempering process is still held at 735°C for 105 minutes.