Straight seam steel pipe is a welded pipe with the weld seam parallel to the longitudinal direction of the steel pipe. According to the production process, it is divided into ERW steel pipe and LSAW steel pipe. The production process of straight seam welded pipe is simple, the production efficiency is high, the cost is low, and the development is fast. The strength of the spiral welded pipe is generally higher than that of the straight seam welded pipe. However, compared with the same length of straight seam pipe, the length of the weld is increased by 30~100%, and the production speed is lower.
Large-diameter straight seam steel pipes generally refer to straight seam steel pipes with an outer diameter of more than 500mm. At present, the maximum diameter of double welds can reach 2020mm, and the maximum diameter of single welds can reach 1220mm. It is the best choice for large-scale pipeline projects, water and gas transmission projects, and urban pipeline network construction.
Most of the projects in which large-diameter straight seam steel pipes are used are high-pressure or piling steel structures, and the overall quality of the steel pipes and the welding seam are relatively strict, especially the welding seam inspection must be satisfied. There are two types of welding seam inspection: ultrasonic inspection and X-ray inspection
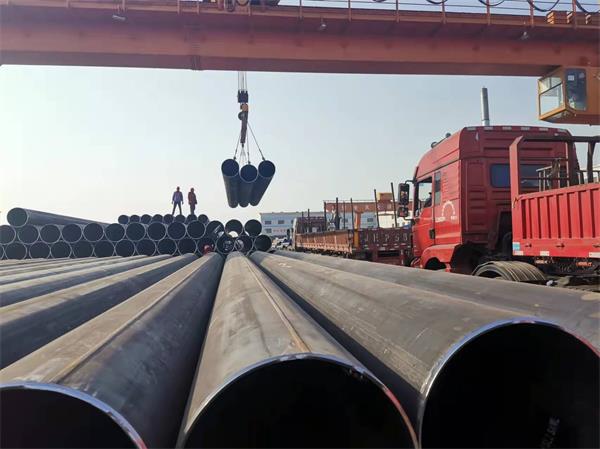
X-ray flaw detection is mainly used for some small-diameter or pipe fittings. It has special requirements for the site and must be detected in a dark space. Its operation is troublesome, it can only be operated at night, and the efficiency is relatively slow and the cost is high.Therefore, most of the large-diameter straight seam steel pipes use ultrasonic flaw detection. There is no requirement for the site of flaw detection. The operation can be carried out anytime, anywhere, and the efficiency is very high. About 100 tons of flaws can be detected a day.
Process standard for ultrasonic basic flaw detection of large-diameter straight seam steel pipes:
The large-diameter straight seam steel pipe needs to be cooled for 48 hours before the flaw detection can be carried out. The small particle weld around the weld is polished off, and then the probe penetrates into the feature of reflection at the edge of the interface to check the defect of the part.When the ultrasonic beam passes from the probe to the inside of the metal from the surface of the part, when it encounters the defect and the bottom surface of the part, reflected waves are generated respectively, and a pulse waveform is formed on the fluorescent screen.According to these pulse waveforms, the position and size of the defect can be judged. Cracks, scratches, pores in the weld, slag inclusions, cracks, incomplete penetration and other defects can be directly understood, and then the size of the defect is marked and repaired.
Large-diameter straight seam steel pipes generally refer to straight seam steel pipes with an outer diameter of more than 500mm. At present, the maximum diameter of double welds can reach 2020mm, and the maximum diameter of single welds can reach 1220mm. It is the best choice for large-scale pipeline projects, water and gas transmission projects, and urban pipeline network construction.
Most of the projects in which large-diameter straight seam steel pipes are used are high-pressure or piling steel structures, and the overall quality of the steel pipes and the welding seam are relatively strict, especially the welding seam inspection must be satisfied. There are two types of welding seam inspection: ultrasonic inspection and X-ray inspection
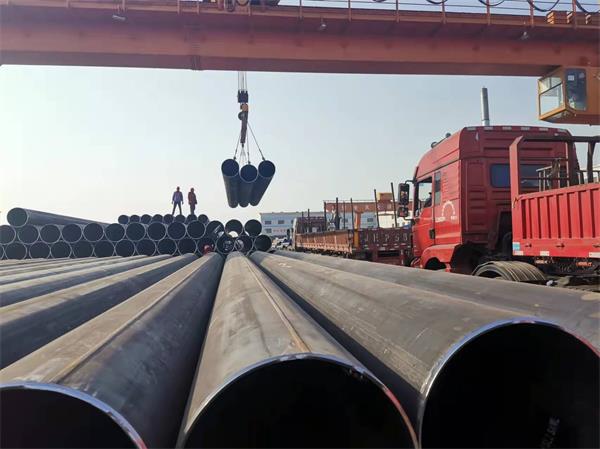
X-ray flaw detection is mainly used for some small-diameter or pipe fittings. It has special requirements for the site and must be detected in a dark space. Its operation is troublesome, it can only be operated at night, and the efficiency is relatively slow and the cost is high.Therefore, most of the large-diameter straight seam steel pipes use ultrasonic flaw detection. There is no requirement for the site of flaw detection. The operation can be carried out anytime, anywhere, and the efficiency is very high. About 100 tons of flaws can be detected a day.
Process standard for ultrasonic basic flaw detection of large-diameter straight seam steel pipes:
The large-diameter straight seam steel pipe needs to be cooled for 48 hours before the flaw detection can be carried out. The small particle weld around the weld is polished off, and then the probe penetrates into the feature of reflection at the edge of the interface to check the defect of the part.When the ultrasonic beam passes from the probe to the inside of the metal from the surface of the part, when it encounters the defect and the bottom surface of the part, reflected waves are generated respectively, and a pulse waveform is formed on the fluorescent screen.According to these pulse waveforms, the position and size of the defect can be judged. Cracks, scratches, pores in the weld, slag inclusions, cracks, incomplete penetration and other defects can be directly understood, and then the size of the defect is marked and repaired.