The welded steel pipe is a steel pipe made of steel plate or strip steel after being crimped and welded, generally with a length of 6 meters. The production process of welded steel pipe is simple, the production efficiency is high, there are many varieties and specifications, and the investment in equipment is small, but the general strength is lower than that of seamless steel pipe. Welded steel pipes are divided into straight seam welded pipes and spiral welded pipes (SSAW steel pipe) according to the form of welds. Classification by production method: process classification - arc welded pipe, electric resistance welded pipe (ERW pipe), (high frequency, low frequency) gas welded pipe, furnace welded pipe.
The parameters of the weld geometry of welded steel pipes include weld width, reinforcement, penetration depth,
(1) The width of the weld refers to the junction of the weld surface and the base metal, which is called the weld toe. In the cross-section of a single-run weld, the distance between two weld toes is called the weld width.
(2) Reinforcement refers to the height of the part of the weld metal that exceeds the weld toe line on the weld surface and is called reinforcement. The reinforcement of the weld seam increases the cross section of the weld seam, improves the bearing capacity, and increases the sensitivity of radiography, but causes stress concentration at the weld toe.
(3) Penetration On the cross section of the welded joint, the depth of melting of the base metal is called penetration. A certain penetration value ensures the bonding strength between the weld and the base metal. When the filler metal material (electrode or wire) is constant, the depth of penetration determines the chemical composition of the weld. Different welding methods require different penetration values.
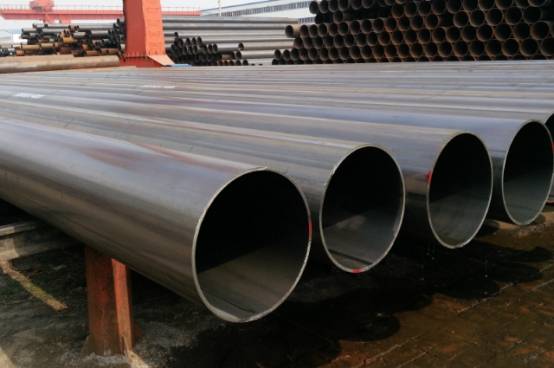
Influence of parameters on weld parameters of welded pipe
When welding steel pipes, the physical quantities selected to ensure welding quality (for example, welding current, arc voltage, welding speed, line energy, etc.) are collectively referred to as welding process parameters. The influence of process parameters on the weld shape is as follows:
(1) Welding current When other conditions remain unchanged, increasing the welding current increases the thickness and reinforcement of the weld seam, while the width of the weld seam remains almost unchanged (or increases slightly).
(2) Arc voltage When other conditions remain unchanged, the arc voltage increases, the width of the weld increases significantly, and the thickness and reinforcement of the weld decrease slightly
(3) Welding speed When other conditions remain unchanged, the welding speed increases, and the weld width, weld thickness and reinforcement all decrease.
Welding current, arc voltage and welding speed are the three major welding process parameters during welding. When selecting, the proper cooperation between the three should be considered to obtain a weld with good shape and meeting the requirements.
The parameters of the weld geometry of welded steel pipes include weld width, reinforcement, penetration depth,
(1) The width of the weld refers to the junction of the weld surface and the base metal, which is called the weld toe. In the cross-section of a single-run weld, the distance between two weld toes is called the weld width.
(2) Reinforcement refers to the height of the part of the weld metal that exceeds the weld toe line on the weld surface and is called reinforcement. The reinforcement of the weld seam increases the cross section of the weld seam, improves the bearing capacity, and increases the sensitivity of radiography, but causes stress concentration at the weld toe.
(3) Penetration On the cross section of the welded joint, the depth of melting of the base metal is called penetration. A certain penetration value ensures the bonding strength between the weld and the base metal. When the filler metal material (electrode or wire) is constant, the depth of penetration determines the chemical composition of the weld. Different welding methods require different penetration values.
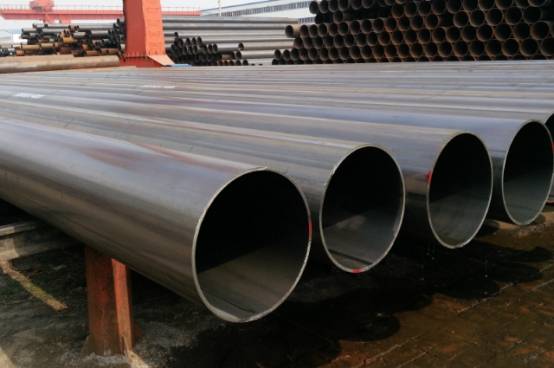
Influence of parameters on weld parameters of welded pipe
When welding steel pipes, the physical quantities selected to ensure welding quality (for example, welding current, arc voltage, welding speed, line energy, etc.) are collectively referred to as welding process parameters. The influence of process parameters on the weld shape is as follows:
(1) Welding current When other conditions remain unchanged, increasing the welding current increases the thickness and reinforcement of the weld seam, while the width of the weld seam remains almost unchanged (or increases slightly).
(2) Arc voltage When other conditions remain unchanged, the arc voltage increases, the width of the weld increases significantly, and the thickness and reinforcement of the weld decrease slightly
(3) Welding speed When other conditions remain unchanged, the welding speed increases, and the weld width, weld thickness and reinforcement all decrease.
Welding current, arc voltage and welding speed are the three major welding process parameters during welding. When selecting, the proper cooperation between the three should be considered to obtain a weld with good shape and meeting the requirements.