Galvanized steel is a corrosion-resistant steel plate covered with a layer of zinc. Galvanized sheets are commonly used to make building materials and industrial components such as roofs, walls, water pipes, cable trays, etc.
(1)Welding characteristics
Galvanized steel is generally coated with a layer of zinc on the outside of low carbon steel, and the zinc layer is generally 20um thick. The melting point of zinc is 419°C and the boiling point is around 908°C. During welding, zinc melts into a liquid and floats on the surface of the molten pool or at the root of the weld. Zinc has a large solid solubility in iron. The zinc liquid will etch the weld metal deeply along the grain boundaries, and the low melting point zinc will form "liquid metal embrittlement".
At the same time, zinc and iron can form intermetallic brittle compounds. These brittle phases reduce the plasticity of the weld metal and cause cracks under the action of tensile stress. If fillet welds are welded, especially those of T-shaped joints, they are most likely to produce penetration cracks. When welding galvanized steel, the zinc layer on the groove surface and edges will oxidize, melt, evaporate and even volatilize white smoke and steam under the action of arc heat, which can easily cause weld porosity.
ZnO formed due to oxidation has a high melting point, about 1800°C or above. If the parameters are too small during the welding process, ZnO slag inclusion will be caused. Because Zn becomes a deoxidizer. FeO-MnO or FeO-MnO-SiO2 low melting point oxide slag inclusions are produced. Secondly, due to the evaporation of zinc, a large amount of white smoke is emitted, which is irritating and harmful to the human body. Therefore, the galvanized layer at the welding joint must be polished away.
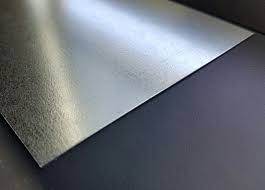
(2)Welding process control
The preparation before welding of steel plate galvanized is the same as that of ordinary low carbon steel. It should be noted that the groove size and nearby galvanized layer must be carefully processed. In order to achieve welding penetration, the groove size must be appropriate, usually 60~65°, and a certain gap must be left, usually 1.5~2.5mm; in order to reduce the penetration of zinc into the weld, before welding, the galvanized surface in the groove can be Do not weld until the layer is removed. In the actual supervision work, centralized beveling, centralized control without leaving blunt edges, and two-layer welding process were adopted to reduce the possibility of incomplete welding.
The welding rod should be selected according to the base material of the galvanized pipe. Generally, J422 is more commonly used for low carbon steel due to ease of operation.
(3)Welding techniques
When welding the first layer of multi-layer welding, try to melt the zinc layer and allow it to vaporize and evaporate to escape the weld, which can greatly reduce the amount of liquid zinc remaining in the weld.
When welding fillet welds, try to melt the zinc layer in the first layer and make it vaporize and evaporate to escape the weld. The method is to first move the end of the welding rod forward about 5~7mm. When the zinc layer After melting, return to the original position and continue welding forward.
In horizontal and vertical welding, if short slag electrodes such as J427 are used, the undercut tendency will be very small; if the back and forth rod transport technology is used, defect-free welding quality can be obtained.
The following points need to be noted when welding galvanized sheets:
(1) Before welding, the zinc layer must be cleaned to avoid the generation of toxic gases during welding. Solvents or other cleaning agents can be used for cleaning.
(2) Select the correct welding current and voltage to ensure welding quality and stability.
(3) Reduce the welding time as much as possible and avoid overheating the zinc layer to avoid damage and oxidation of the zinc layer.
(4) During welding, large amounts of heat should be avoided at the same location to avoid damaging the zinc layer and causing corrosion.
(5) When performing gas welding or arc welding, low-temperature welding rods should be used and avoid pointing the flame or arc directly at the zinc layer.
(6) For galvanized sheets after welding, rust removal and anti-corrosion treatment should be carried out on the welded parts to ensure the quality and anti-corrosion effect of the welding.
(7) Before welding, the surface of the galvanized sheet should be checked for cracks, bubbles or other defects to avoid quality problems during welding.
(8) When performing MIG or TIG welding, appropriate gases, such as argon or carbon dioxide gas, should be selected to ensure the stability of the welding process and welding quality.
(9) The thickness of the galvanized sheet is thin, so the welding current and voltage need to be controlled to avoid excessive welding.
(10) When performing gas welding or arc welding, you need to pay attention to the direction of sparks and flames, and avoid direct aiming at the zinc layer to avoid damaging the zinc layer and causing corrosion.
Galvanizing has become an important anti-corrosion method for steel plates, not only because zinc can form a dense protective layer on the surface of steel, but also because zinc has a cathodic protection effect. When the galvanized layer is damaged, it can still prevent iron matrix through cathodic protection. Material corrosion. Therefore, when cracks appear in galvanized sheets, how to weld becomes our primary concern. How to weld without zinc explosion, which also brings greater challenges to welding workers. The existence of the zinc layer brings certain difficulties to the welding of galvanized sheets.
Preventing zinc explosion, that is, preventing the explosion of zinc vapor, is an important safety measure when welding galvanized sheets.
The melting point of zinc is about 420℃, and the volatilization temperature is 908℃, which is not conducive to welding. It volatilizes as soon as the arc is ignited. The volatilization and oxidation of zinc can cause pores, lack of fusion and cracks and even affect arc stability. Therefore, the method for welding galvanized sheets is to reduce the heat input.
MIG arc brazing: In a sense, it also belongs to gas metal arc welding (MAG). It uses low melting point copper-based welding wire instead of carbon steel welding wire. The heat input during welding is low, the base metal will not melt, and the evaporation of zinc is minimized, improving the corrosion resistance of the weld (copper-based welding is also corrosion-resistant ). This ensures better and more efficient welding of galvanized sheets.
The usually recommended shielding gas is argon, but experiments have shown that CuSi3 can also be used as a shielding gas with a mixed gas containing a small amount of oxygen or carbon dioxide, so that the arc stability is better.
A feasible method is to use brazing materials to weld galvanized sheets. The most commonly used welding wires are copper-silicon alloys (such as CuSi3) and copper-aluminum alloys. Due to the high copper content in these welding wires, the melting point is relatively low, and the base metal has not yet melted. Such joints are actually brazed joints.
Galvanizing can effectively protect the incisions of the plate and micro-cracks caused by cold working, as well as the zinc burnt area near the weld, preventing rust from starting here. Correct welding methods can effectively protect the safety of the galvanized layer, thereby ensuring that the plate is not corroded.
The galvanized layer of the galvanized steel plate at the welding point may be damaged, which will have an adverse effect on subsequent anti-corrosion. Anti-corrosion treatment can be carried out in the following ways.
(1)Clean the surface
The first step in the post-weld anti-corrosion of galvanized steel sheets is to clean the welded parts. Use tools to clean them to remove welding slag, dust, impurities and other substances, so that the welded parts can easily adhere to the anti-corrosion coating.
(2) Anti-corrosion coating construction
At present, the anti-corrosion treatment of steel plates is mainly based on coating protection with various coatings. Choosing appropriate coatings is the key to pipeline anti-corrosion. Common anti-corrosion coatings include epoxy resin coatings, polyurethane coatings and acrylic coatings, etc. The appropriate coating should be selected according to actual needs.
Coating construction should be carried out in accordance with the instructions and operating instructions. Applying several thin coats will be more effective and provide a better protective layer. During the construction process, pay attention to the fact that the coating needs to evenly cover the welding area.
The coating methods of anti-corrosion coatings can be divided into four types: brushing, spraying, troweling and scraping. During the specific construction process, different coating methods should be selected according to the type, performance, consistency and different construction parts of the coating. construction methods. Thick paint should be applied with an iron trowel or a rubber board; thin paint can be applied manually with a brown brush, long-handled brush, round roller brush, etc., or mechanical spraying can be used.
(3) Pay attention to coating drying and curing:
After the construction of the anti-corrosion coating on the welded joint of the galvanized steel plate is completed, attention should be paid to allowing the coating to dry. During this process, attention should be paid to monitoring the humidity and temperature to prevent wasting all the efforts. After the coating construction is completed, the anti-corrosion condition of the steel plate should be regularly inspected and maintained. , removing surface impurities and repairing coatings are important ways to extend the life of steel plates.
1. Method of welding galvanized sheets
When welding galvanized sheets, it is best to use MIG (metal inert gas) welding or TIG (tungsten arc) welding methods. Both methods melt and join metal materials together at high temperatures, and they prevent zinc oxide from evaporating during the welding process and causing the release of toxic gases. Alternatively, galvanized sheets can be welded using arc or gas welding methods, but extra care needs to be taken to avoid heat damage to the zinc layer.
2. Welding process of gi steel plate
(1)Welding characteristicsGalvanized steel is generally coated with a layer of zinc on the outside of low carbon steel, and the zinc layer is generally 20um thick. The melting point of zinc is 419°C and the boiling point is around 908°C. During welding, zinc melts into a liquid and floats on the surface of the molten pool or at the root of the weld. Zinc has a large solid solubility in iron. The zinc liquid will etch the weld metal deeply along the grain boundaries, and the low melting point zinc will form "liquid metal embrittlement".
At the same time, zinc and iron can form intermetallic brittle compounds. These brittle phases reduce the plasticity of the weld metal and cause cracks under the action of tensile stress. If fillet welds are welded, especially those of T-shaped joints, they are most likely to produce penetration cracks. When welding galvanized steel, the zinc layer on the groove surface and edges will oxidize, melt, evaporate and even volatilize white smoke and steam under the action of arc heat, which can easily cause weld porosity.
ZnO formed due to oxidation has a high melting point, about 1800°C or above. If the parameters are too small during the welding process, ZnO slag inclusion will be caused. Because Zn becomes a deoxidizer. FeO-MnO or FeO-MnO-SiO2 low melting point oxide slag inclusions are produced. Secondly, due to the evaporation of zinc, a large amount of white smoke is emitted, which is irritating and harmful to the human body. Therefore, the galvanized layer at the welding joint must be polished away.
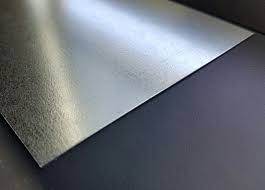
(2)Welding process control
The preparation before welding of steel plate galvanized is the same as that of ordinary low carbon steel. It should be noted that the groove size and nearby galvanized layer must be carefully processed. In order to achieve welding penetration, the groove size must be appropriate, usually 60~65°, and a certain gap must be left, usually 1.5~2.5mm; in order to reduce the penetration of zinc into the weld, before welding, the galvanized surface in the groove can be Do not weld until the layer is removed. In the actual supervision work, centralized beveling, centralized control without leaving blunt edges, and two-layer welding process were adopted to reduce the possibility of incomplete welding.
The welding rod should be selected according to the base material of the galvanized pipe. Generally, J422 is more commonly used for low carbon steel due to ease of operation.
(3)Welding techniques
When welding the first layer of multi-layer welding, try to melt the zinc layer and allow it to vaporize and evaporate to escape the weld, which can greatly reduce the amount of liquid zinc remaining in the weld.
When welding fillet welds, try to melt the zinc layer in the first layer and make it vaporize and evaporate to escape the weld. The method is to first move the end of the welding rod forward about 5~7mm. When the zinc layer After melting, return to the original position and continue welding forward.
In horizontal and vertical welding, if short slag electrodes such as J427 are used, the undercut tendency will be very small; if the back and forth rod transport technology is used, defect-free welding quality can be obtained.
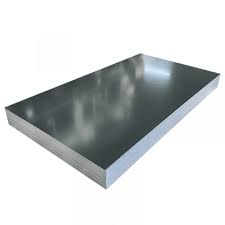
3. Precautions when welding galvanized steel plates
The following points need to be noted when welding galvanized sheets:(1) Before welding, the zinc layer must be cleaned to avoid the generation of toxic gases during welding. Solvents or other cleaning agents can be used for cleaning.
(2) Select the correct welding current and voltage to ensure welding quality and stability.
(3) Reduce the welding time as much as possible and avoid overheating the zinc layer to avoid damage and oxidation of the zinc layer.
(4) During welding, large amounts of heat should be avoided at the same location to avoid damaging the zinc layer and causing corrosion.
(5) When performing gas welding or arc welding, low-temperature welding rods should be used and avoid pointing the flame or arc directly at the zinc layer.
(6) For galvanized sheets after welding, rust removal and anti-corrosion treatment should be carried out on the welded parts to ensure the quality and anti-corrosion effect of the welding.
(7) Before welding, the surface of the galvanized sheet should be checked for cracks, bubbles or other defects to avoid quality problems during welding.
(8) When performing MIG or TIG welding, appropriate gases, such as argon or carbon dioxide gas, should be selected to ensure the stability of the welding process and welding quality.
(9) The thickness of the galvanized sheet is thin, so the welding current and voltage need to be controlled to avoid excessive welding.
(10) When performing gas welding or arc welding, you need to pay attention to the direction of sparks and flames, and avoid direct aiming at the zinc layer to avoid damaging the zinc layer and causing corrosion.
2. How to prevent zinc explosion when welding galvanized sheets?
Galvanizing has become an important anti-corrosion method for steel plates, not only because zinc can form a dense protective layer on the surface of steel, but also because zinc has a cathodic protection effect. When the galvanized layer is damaged, it can still prevent iron matrix through cathodic protection. Material corrosion. Therefore, when cracks appear in galvanized sheets, how to weld becomes our primary concern. How to weld without zinc explosion, which also brings greater challenges to welding workers. The existence of the zinc layer brings certain difficulties to the welding of galvanized sheets.Preventing zinc explosion, that is, preventing the explosion of zinc vapor, is an important safety measure when welding galvanized sheets.
The melting point of zinc is about 420℃, and the volatilization temperature is 908℃, which is not conducive to welding. It volatilizes as soon as the arc is ignited. The volatilization and oxidation of zinc can cause pores, lack of fusion and cracks and even affect arc stability. Therefore, the method for welding galvanized sheets is to reduce the heat input.
MIG arc brazing: In a sense, it also belongs to gas metal arc welding (MAG). It uses low melting point copper-based welding wire instead of carbon steel welding wire. The heat input during welding is low, the base metal will not melt, and the evaporation of zinc is minimized, improving the corrosion resistance of the weld (copper-based welding is also corrosion-resistant ). This ensures better and more efficient welding of galvanized sheets.
The usually recommended shielding gas is argon, but experiments have shown that CuSi3 can also be used as a shielding gas with a mixed gas containing a small amount of oxygen or carbon dioxide, so that the arc stability is better.
A feasible method is to use brazing materials to weld galvanized sheets. The most commonly used welding wires are copper-silicon alloys (such as CuSi3) and copper-aluminum alloys. Due to the high copper content in these welding wires, the melting point is relatively low, and the base metal has not yet melted. Such joints are actually brazed joints.
Galvanizing can effectively protect the incisions of the plate and micro-cracks caused by cold working, as well as the zinc burnt area near the weld, preventing rust from starting here. Correct welding methods can effectively protect the safety of the galvanized layer, thereby ensuring that the plate is not corroded.
4. Anti-corrosion treatment after welding of galvanized steel plates
The galvanized layer of the galvanized steel plate at the welding point may be damaged, which will have an adverse effect on subsequent anti-corrosion. Anti-corrosion treatment can be carried out in the following ways.(1)Clean the surface
The first step in the post-weld anti-corrosion of galvanized steel sheets is to clean the welded parts. Use tools to clean them to remove welding slag, dust, impurities and other substances, so that the welded parts can easily adhere to the anti-corrosion coating.
(2) Anti-corrosion coating construction
At present, the anti-corrosion treatment of steel plates is mainly based on coating protection with various coatings. Choosing appropriate coatings is the key to pipeline anti-corrosion. Common anti-corrosion coatings include epoxy resin coatings, polyurethane coatings and acrylic coatings, etc. The appropriate coating should be selected according to actual needs.
Coating construction should be carried out in accordance with the instructions and operating instructions. Applying several thin coats will be more effective and provide a better protective layer. During the construction process, pay attention to the fact that the coating needs to evenly cover the welding area.
The coating methods of anti-corrosion coatings can be divided into four types: brushing, spraying, troweling and scraping. During the specific construction process, different coating methods should be selected according to the type, performance, consistency and different construction parts of the coating. construction methods. Thick paint should be applied with an iron trowel or a rubber board; thin paint can be applied manually with a brown brush, long-handled brush, round roller brush, etc., or mechanical spraying can be used.
(3) Pay attention to coating drying and curing:
After the construction of the anti-corrosion coating on the welded joint of the galvanized steel plate is completed, attention should be paid to allowing the coating to dry. During this process, attention should be paid to monitoring the humidity and temperature to prevent wasting all the efforts. After the coating construction is completed, the anti-corrosion condition of the steel plate should be regularly inspected and maintained. , removing surface impurities and repairing coatings are important ways to extend the life of steel plates.