Galvanized pipe has the dual advantages of corrosion resistance and long service life, and the price is corresponding to that of carbon steel seamless pipe or welded pipe, which is relatively cheap and has an increasing usage rate. However, some users do not pay attention when welding galvanized pipes, resulting in steel pipe defects. So what issues should we pay attention to when welding galvanized pipes?
1. The premise is to polish
The galvanized layer at the welding joint must be polished off, otherwise bubbles, trachoma, false welding, etc. will occur. It will also make the weld brittle and reduce its rigidity.
2. Characteristics of galvanized steel pipes
Galvanized steel is generally coated with a layer of zinc on the outside of low carbon steel, and the zinc layer is generally 20um thick. The melting point of zinc is 419°C and the boiling point is around 908°C. During welding, zinc melts into a liquid and floats on the surface of the molten pool or at the root of the weld. Zinc has a large solid solubility in iron. The zinc liquid will etch the weld metal deeply along the grain boundaries, and the low melting point zinc will form "liquid metal embrittlement". At the same time, zinc and iron can form intermetallic brittle compounds. These brittle phases reduce the plasticity of the weld metal and cause cracks under the action of tensile stress.
When welding galvanized steel, the zinc layer on the groove surface and edges will oxidize, melt, evaporate and even volatilize white smoke and steam under the action of arc heat, which can easily cause weld porosity. ZnO formed due to oxidation has a high melting point, about 1800°C or above. If the parameters are too small during the welding process, ZnO slag inclusion will be caused. Because Zn becomes a deoxidizer. FeO-MnO or FeO-MnO-SiO2 low melting point oxide slag inclusions are produced. Secondly, due to the evaporation of zinc, a large amount of white smoke is emitted, which is irritating and harmful to the human body. Therefore, the galvanized layer at the welding joint must be polished away.
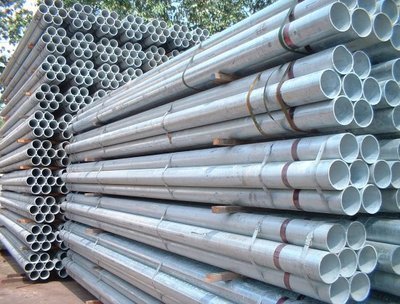
3. Welding process control
The preparation before welding of galvanized steel is the same as that of ordinary low carbon steel. It should be noted that the groove size and nearby galvanized layer must be carefully processed. In order to achieve welding penetration, the groove size must be appropriate, generally 60~65°. There should be a certain gap, usually 1.5~2.5mm. In order to reduce the penetration of zinc into the weld, the galvanized layer in the groove can be removed before welding.
In actual work, centralized beveling, centralized control without leaving blunt edges, and two-layer welding process were used to reduce the possibility of incomplete welding.
4. Welding techniques
When welding the first layer of multi-layer welding, try to melt the zinc layer and allow it to vaporize and evaporate to escape the weld, which can greatly reduce the amount of liquid zinc remaining in the weld. When welding fillet welds, try to melt the zinc layer in the first layer and allow it to vaporize and evaporate to escape the weld. The method is to first move the end of the welding rod forward about 5~7mm, and then return to the original position after the zinc layer is melted to continue welding forward.
Galvanized pipes are widely used, in addition to being used as pipeline pipes for conveying water, gas, oil and other general low-pressure fluids. It is also used as oil well pipes and oil pipelines in the petroleum industry, especially offshore oil fields, oil heaters, condensation coolers, coal distillate oil exchanger pipes for chemical coking equipment, and pipes for trestle pipe piles and support frames of mine tunnels. Therefore, we must pay attention to using the correct method when welding to ensure the service life of the steel pipe.
1. The premise is to polish
The galvanized layer at the welding joint must be polished off, otherwise bubbles, trachoma, false welding, etc. will occur. It will also make the weld brittle and reduce its rigidity.
2. Characteristics of galvanized steel pipes
Galvanized steel is generally coated with a layer of zinc on the outside of low carbon steel, and the zinc layer is generally 20um thick. The melting point of zinc is 419°C and the boiling point is around 908°C. During welding, zinc melts into a liquid and floats on the surface of the molten pool or at the root of the weld. Zinc has a large solid solubility in iron. The zinc liquid will etch the weld metal deeply along the grain boundaries, and the low melting point zinc will form "liquid metal embrittlement". At the same time, zinc and iron can form intermetallic brittle compounds. These brittle phases reduce the plasticity of the weld metal and cause cracks under the action of tensile stress.
When welding galvanized steel, the zinc layer on the groove surface and edges will oxidize, melt, evaporate and even volatilize white smoke and steam under the action of arc heat, which can easily cause weld porosity. ZnO formed due to oxidation has a high melting point, about 1800°C or above. If the parameters are too small during the welding process, ZnO slag inclusion will be caused. Because Zn becomes a deoxidizer. FeO-MnO or FeO-MnO-SiO2 low melting point oxide slag inclusions are produced. Secondly, due to the evaporation of zinc, a large amount of white smoke is emitted, which is irritating and harmful to the human body. Therefore, the galvanized layer at the welding joint must be polished away.
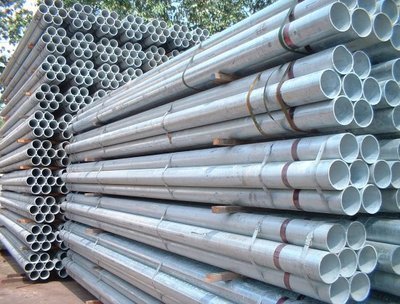
3. Welding process control
The preparation before welding of galvanized steel is the same as that of ordinary low carbon steel. It should be noted that the groove size and nearby galvanized layer must be carefully processed. In order to achieve welding penetration, the groove size must be appropriate, generally 60~65°. There should be a certain gap, usually 1.5~2.5mm. In order to reduce the penetration of zinc into the weld, the galvanized layer in the groove can be removed before welding.
In actual work, centralized beveling, centralized control without leaving blunt edges, and two-layer welding process were used to reduce the possibility of incomplete welding.
4. Welding techniques
When welding the first layer of multi-layer welding, try to melt the zinc layer and allow it to vaporize and evaporate to escape the weld, which can greatly reduce the amount of liquid zinc remaining in the weld. When welding fillet welds, try to melt the zinc layer in the first layer and allow it to vaporize and evaporate to escape the weld. The method is to first move the end of the welding rod forward about 5~7mm, and then return to the original position after the zinc layer is melted to continue welding forward.
Galvanized pipes are widely used, in addition to being used as pipeline pipes for conveying water, gas, oil and other general low-pressure fluids. It is also used as oil well pipes and oil pipelines in the petroleum industry, especially offshore oil fields, oil heaters, condensation coolers, coal distillate oil exchanger pipes for chemical coking equipment, and pipes for trestle pipe piles and support frames of mine tunnels. Therefore, we must pay attention to using the correct method when welding to ensure the service life of the steel pipe.