The following is the welding process of the octg casing
1. Preparation
(1) Determine the welding method: according to the usage requirements of octg casing, select the appropriate welding method. Common ones include manual arc welding, gas shielded welding, resistance welding, etc.
(2) Prepare materials and equipment: including pipeline materials, welding power sources, welding electrodes, gas protection devices, welding auxiliary tools, etc.
(3) Clean the work area: make sure the welding area is clean and remove debris and oil.
2. Pipeline preparation
(1) Cutting the pipe: use appropriate cutting tools to cut the pipe to the required length according to the design requirements and measurement results.
(2) Groove processing:according to the requirements of the welding method and the pipe material, adopt appropriate groove forms, such as V-shaped groove, U-shaped groove, etc.
(3) Clean the pipe surface: use brushes, empty cloth and other tools to clean the pipe surface to ensure that there is no oil, oxides and other impurities.
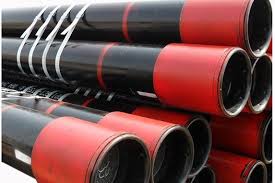
3. Welding preparation
(1) Welding power supply settings: set parameters such as welding current, voltage and welding speed according to the pipe material and welding method.
(2) Prepare welding electrodes: select appropriate welding electrodes, and bake and dry them as required to improve welding quality.
(3) Preheat the pipe.
4. Welding operations
(1) Fix the pipe: use clamps, brackets and other tools to fix the pipe in the welding position to ensure the accurate position of the pipe.
(2) Welding joint: according to the welding method, the welding electrode or welding rod is welded at the groove position to control the welding speed and welding quality.
(3) Inspect the welds: after the welding is completed, use visual inspection, radioactive testing and other methods to inspect the welds to ensure that there are no obvious defects or cracks.
(4) Trimming welds: for defective welds, trimming tools can be used to trim them to improve the welding quality.
Precautions for octg casing welding
1. Before connecting the pipes, clear the debris in the pipes and seal them with blocking plates when stopping work to reduce the workload of pipe flushing.
2. Before welding, the oil stains and other debris on the pipe mouth should be polished away to expose the metallic luster.
3. Before assembling the pipe, the groove and its internal and external surfaces should be cleaned manually or mechanically to remove dirt, rust, burrs, etc. within 100 mm of the edge of the pipe. Temporary blind plates should be added to both ends of the pipe before the end of the work.
4. In order to prevent cracks in welding and reduce internal stress, no forced alignment is allowed.
5. When welding multiple layers, the root of the first layer of welding seam should be welded through and must not be burned through.
6. Unqualified welds must be repaired no more than 3 times.
7. The starting point of the weld bead between adjacent layers should be staggered by 20~30 mm. The welding arc should be started within the groove. It is strictly prohibited to start the arc on the pipe wall.
8. On rainy days or in environments where the wind speed exceeds 8 m/s, effective protective measures such as building a weatherproof shed must be taken, otherwise welding should not be carried out.
1. Preparation
(1) Determine the welding method: according to the usage requirements of octg casing, select the appropriate welding method. Common ones include manual arc welding, gas shielded welding, resistance welding, etc.
(2) Prepare materials and equipment: including pipeline materials, welding power sources, welding electrodes, gas protection devices, welding auxiliary tools, etc.
(3) Clean the work area: make sure the welding area is clean and remove debris and oil.
2. Pipeline preparation
(1) Cutting the pipe: use appropriate cutting tools to cut the pipe to the required length according to the design requirements and measurement results.
(2) Groove processing:according to the requirements of the welding method and the pipe material, adopt appropriate groove forms, such as V-shaped groove, U-shaped groove, etc.
(3) Clean the pipe surface: use brushes, empty cloth and other tools to clean the pipe surface to ensure that there is no oil, oxides and other impurities.
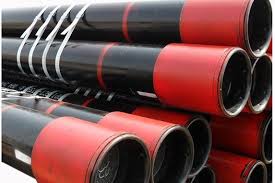
3. Welding preparation
(1) Welding power supply settings: set parameters such as welding current, voltage and welding speed according to the pipe material and welding method.
(2) Prepare welding electrodes: select appropriate welding electrodes, and bake and dry them as required to improve welding quality.
(3) Preheat the pipe.
4. Welding operations
(1) Fix the pipe: use clamps, brackets and other tools to fix the pipe in the welding position to ensure the accurate position of the pipe.
(2) Welding joint: according to the welding method, the welding electrode or welding rod is welded at the groove position to control the welding speed and welding quality.
(3) Inspect the welds: after the welding is completed, use visual inspection, radioactive testing and other methods to inspect the welds to ensure that there are no obvious defects or cracks.
(4) Trimming welds: for defective welds, trimming tools can be used to trim them to improve the welding quality.
Precautions for octg casing welding
1. Before connecting the pipes, clear the debris in the pipes and seal them with blocking plates when stopping work to reduce the workload of pipe flushing.
2. Before welding, the oil stains and other debris on the pipe mouth should be polished away to expose the metallic luster.
3. Before assembling the pipe, the groove and its internal and external surfaces should be cleaned manually or mechanically to remove dirt, rust, burrs, etc. within 100 mm of the edge of the pipe. Temporary blind plates should be added to both ends of the pipe before the end of the work.
4. In order to prevent cracks in welding and reduce internal stress, no forced alignment is allowed.
5. When welding multiple layers, the root of the first layer of welding seam should be welded through and must not be burned through.
6. Unqualified welds must be repaired no more than 3 times.
7. The starting point of the weld bead between adjacent layers should be staggered by 20~30 mm. The welding arc should be started within the groove. It is strictly prohibited to start the arc on the pipe wall.
8. On rainy days or in environments where the wind speed exceeds 8 m/s, effective protective measures such as building a weatherproof shed must be taken, otherwise welding should not be carried out.
Previous:Larson steel sheet pile