Galvanized steel pipe is widely used in all walks of life. The advantage of using galvanized steel is to protect the internal steel structure with metallic zinc that can form a dense oxide protective layer in the air. In the case of being welded or scratched, due to the existence of Zn-Fe primary battery, the relatively active galvanized part can be used as a sacrificial anode, delaying the corrosion of steel and having good corrosion resistance. However, due to the existence of the galvanized layer, cracks, pores, and slag inclusions are easily generated during welding, and it is difficult to obtain good welding quality.
Galvanized steel pipe is generally coated with a layer of zinc on the low carbon steel, and the galvanized layer is generally 20um thick. The melting point of zinc is 419°C and the boiling point is about 908°C. During welding, zinc melts into a liquid that floats on the surface of the weld pool or at the root of the weld. Zinc has a large solid solubility in iron, and the zinc liquid will deeply erode the weld metal along the grain boundary, and the low melting point zinc will form "liquid metal embrittlement".At the same time, zinc and iron can form intermetallic brittle compounds, such as Fe3Zn10, FeZn10 and so on. These brittle phases reduce the plasticity of the weld metal and cause cracks under the action of tensile stress.
If the fillet weld is welded, especially the fillet weld of the T-joint is most prone to penetration cracks. When galvanized steel pipe is welded, the zinc layer on the groove surface and the edge will oxidize, melt, evaporate and even volatilize white smoke and steam under the action of arc heat, which can easily cause weld pores.The ZnO formed by oxidation has a high melting point, about 1800° or more. If the parameters are too small during the welding process, it will cause ZnO slag inclusion.At the same time, FeO-MnO or FeO-MnO-SiO2 low melting point oxide slag inclusions are produced because Zn becomes a deoxidizer.
If the selection of welding specification is not appropriate and the operation method is improper, it is easy to melt the galvanized layer at the green edge of the weld and expand the melting area, which may damage the galvanized layer.Especially in the case of elongated arc and large swing operation, the melting area is widened, and the damage to the galvanized layer is more serious.At the same time, due to the evaporation of zinc, a large amount of white smoke and dust is volatilized, which has stimulating and harmful effects on the human body. Therefore, the selection of welding methods and materials that generate a lower amount of smoke and dust is also a factor that must be considered.
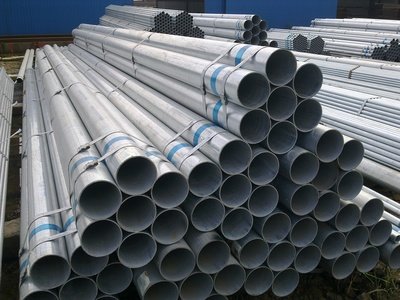
Welding Quality Assurance Measures
Control from five aspects: people, materials, machines, methods, and environment.
1 The human factor is the control focus of welding. Therefore, before welding, a skilled welder with a welder certificate should be selected to carry out necessary technical training and disclosure. It should not be replaced at will, to ensure that the welding personnel of the pipeline are relatively stable.
2 Welding consumables control: ensure that the purchased welding consumables are from regular channels, have quality assurance certificates and certificates of conformity, and meet the process requirements;Strictly control the recycling of fire sticks to ensure the flow direction and dosage;Welding consumables should be baked strictly according to the process, and the dosage should not exceed half a day at a time.
3 Welding machine: The welding machine must ensure reliable performance and meet the needs of the process; the welding machine must have a qualified current and voltmeter to ensure the correct implementation of the welding process. The welding cable should not be too long, and the welding parameters should be adjusted when it is longer.
4. Welding process method: ensure the strict implementation of the special operation method of galvanized pipe, check the welding process parameters before welding, control the operation method, check the appearance quality after welding, and increase the post-weld non-destructive testing if necessary. Control the welding level and the amount of welding consumables per pass.
5 Welding environment control: ensure that the temperature, humidity and wind speed during welding meet the process requirements.
Galvanized steel pipe is generally coated with a layer of zinc on the low carbon steel, and the galvanized layer is generally 20um thick. The melting point of zinc is 419°C and the boiling point is about 908°C. During welding, zinc melts into a liquid that floats on the surface of the weld pool or at the root of the weld. Zinc has a large solid solubility in iron, and the zinc liquid will deeply erode the weld metal along the grain boundary, and the low melting point zinc will form "liquid metal embrittlement".At the same time, zinc and iron can form intermetallic brittle compounds, such as Fe3Zn10, FeZn10 and so on. These brittle phases reduce the plasticity of the weld metal and cause cracks under the action of tensile stress.
If the fillet weld is welded, especially the fillet weld of the T-joint is most prone to penetration cracks. When galvanized steel pipe is welded, the zinc layer on the groove surface and the edge will oxidize, melt, evaporate and even volatilize white smoke and steam under the action of arc heat, which can easily cause weld pores.The ZnO formed by oxidation has a high melting point, about 1800° or more. If the parameters are too small during the welding process, it will cause ZnO slag inclusion.At the same time, FeO-MnO or FeO-MnO-SiO2 low melting point oxide slag inclusions are produced because Zn becomes a deoxidizer.
If the selection of welding specification is not appropriate and the operation method is improper, it is easy to melt the galvanized layer at the green edge of the weld and expand the melting area, which may damage the galvanized layer.Especially in the case of elongated arc and large swing operation, the melting area is widened, and the damage to the galvanized layer is more serious.At the same time, due to the evaporation of zinc, a large amount of white smoke and dust is volatilized, which has stimulating and harmful effects on the human body. Therefore, the selection of welding methods and materials that generate a lower amount of smoke and dust is also a factor that must be considered.
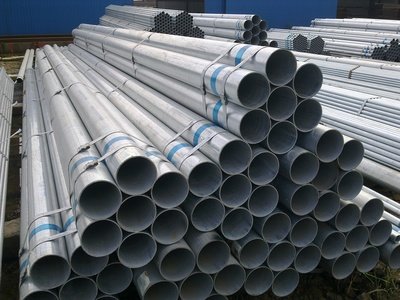
Welding Quality Assurance Measures
Control from five aspects: people, materials, machines, methods, and environment.
1 The human factor is the control focus of welding. Therefore, before welding, a skilled welder with a welder certificate should be selected to carry out necessary technical training and disclosure. It should not be replaced at will, to ensure that the welding personnel of the pipeline are relatively stable.
2 Welding consumables control: ensure that the purchased welding consumables are from regular channels, have quality assurance certificates and certificates of conformity, and meet the process requirements;Strictly control the recycling of fire sticks to ensure the flow direction and dosage;Welding consumables should be baked strictly according to the process, and the dosage should not exceed half a day at a time.
3 Welding machine: The welding machine must ensure reliable performance and meet the needs of the process; the welding machine must have a qualified current and voltmeter to ensure the correct implementation of the welding process. The welding cable should not be too long, and the welding parameters should be adjusted when it is longer.
4. Welding process method: ensure the strict implementation of the special operation method of galvanized pipe, check the welding process parameters before welding, control the operation method, check the appearance quality after welding, and increase the post-weld non-destructive testing if necessary. Control the welding level and the amount of welding consumables per pass.
5 Welding environment control: ensure that the temperature, humidity and wind speed during welding meet the process requirements.