Anti-corrosion measures need to be installed during the use of carbon steel pipes to extend the service life of the pipes. Among them, the commonly used anti-corrosion methods are as follows:
1. Hot-dip galvanizing
Hot-dip galvanizing is a treatment method for coating a zinc layer on the surface of carbon steel pipes. By immersing the carbon steel pipe in high-temperature molten zinc liquid, the zinc reacts with the carbon steel surface to form a zinc layer with uniform thickness, good adhesion and high corrosion resistance, thereby protecting the steel pipe from rust and achieving a long-lasting anti-corrosion effect.
2. Polyethylene anti-corrosion
Polyethylene anti-corrosion is to spray a polyethylene powder soluble in hot water or solvent on the surface of the carbon steel pipe to form a uniform, dense, strong adhesion, good corrosion resistance and weather resistance protective layer. It has very good high and low temperature performance, can be used for a long time at room temperature, and also has self-healing function.
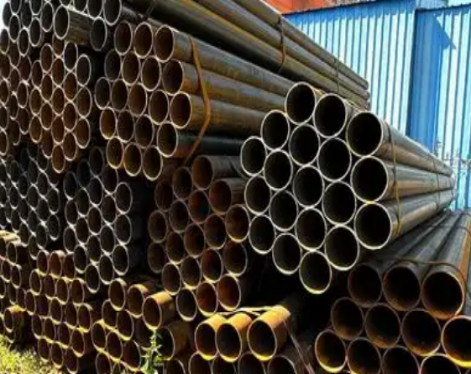
3. Coal tar asphalt anti-corrosion
Coal tar asphalt anti-corrosion is to use coal tar asphalt film to coat the surface of the carbon steel pipe, thereby achieving various tasks of preventing corrosion and chemical resistance. Pipes treated with coal tar pitch have high corrosion resistance to water, oil, etc. They can be used not only at room temperature, but also for a long time in high temperature environments.
4. FRP anti-corrosion
It is well known that fiberglass reinforced plastic (FRP) has good corrosion resistance. It is a material that uses glass fiber to strengthen and reinforce plastic, thereby reducing temperature and corrosion resistance and extending service life. FRP anti-corrosion products are widely used in chemical, petroleum, pharmaceutical, metallurgical, electric power, pulp and other industries and urban water supply and drainage.
How to avoid rusting of carbon steel pipes?
1. Choose a suitable anti-corrosion coating
In order to avoid rusting of carbon steel pipes, an anti-corrosion coating can be added to the surface of the pipe. At present, common anti-corrosion coatings on the market include epoxy paint, polyurethane paint, silicone coating, etc. When choosing an anti-corrosion coating, factors such as the use environment, medium, and working temperature of the pipeline should be considered to select a suitable coating. At the same time, when applying the coating, the thickness and uniformity of the coating should be ensured to ensure complete protection of the pipeline.
2. Clean the pipeline regularly
Pipes will accumulate various corrosive media and impurities during long-term use, which can easily lead to rust. Therefore, the pipeline should be cleaned regularly to ensure the cleanliness of the inside of the pipeline. Before cleaning the pipeline, all the residual media in the pipeline should be removed to avoid secondary contamination of the media during the washing process. In addition, professional washing tools and methods should be used when cleaning the pipeline to ensure that the pipeline is clean and thorough.
3. Strengthen pipeline maintenance
For pipeline maintenance, on the one hand, it is necessary to monitor the use environment of the pipeline, promptly detect abnormal conditions in the pipeline environment, and take measures to reduce the impact of the pipeline on the environment; on the other hand, it is necessary to regularly inspect the pipeline, promptly detect corrosion and wear inside the pipeline, and take measures to repair it. By strengthening pipeline maintenance, the pipeline can be effectively protected, its service life can be extended, and the pipeline can be prevented from rusting.
In summary, underground carbon steel anti-corrosion pipelines often encounter corrosion during use, and appropriate anti-corrosion measures should be selected to extend the service life. The anti-corrosion methods listed above are effective and widely used anti-corrosion measures.
1. Hot-dip galvanizing
Hot-dip galvanizing is a treatment method for coating a zinc layer on the surface of carbon steel pipes. By immersing the carbon steel pipe in high-temperature molten zinc liquid, the zinc reacts with the carbon steel surface to form a zinc layer with uniform thickness, good adhesion and high corrosion resistance, thereby protecting the steel pipe from rust and achieving a long-lasting anti-corrosion effect.
2. Polyethylene anti-corrosion
Polyethylene anti-corrosion is to spray a polyethylene powder soluble in hot water or solvent on the surface of the carbon steel pipe to form a uniform, dense, strong adhesion, good corrosion resistance and weather resistance protective layer. It has very good high and low temperature performance, can be used for a long time at room temperature, and also has self-healing function.
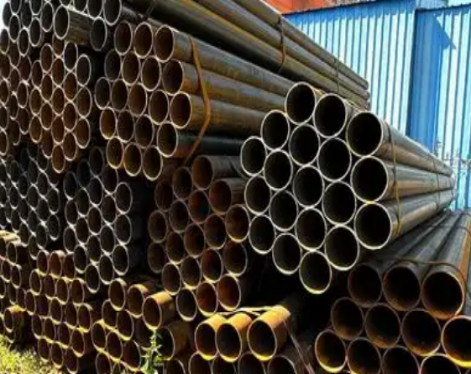
3. Coal tar asphalt anti-corrosion
Coal tar asphalt anti-corrosion is to use coal tar asphalt film to coat the surface of the carbon steel pipe, thereby achieving various tasks of preventing corrosion and chemical resistance. Pipes treated with coal tar pitch have high corrosion resistance to water, oil, etc. They can be used not only at room temperature, but also for a long time in high temperature environments.
4. FRP anti-corrosion
It is well known that fiberglass reinforced plastic (FRP) has good corrosion resistance. It is a material that uses glass fiber to strengthen and reinforce plastic, thereby reducing temperature and corrosion resistance and extending service life. FRP anti-corrosion products are widely used in chemical, petroleum, pharmaceutical, metallurgical, electric power, pulp and other industries and urban water supply and drainage.
How to avoid rusting of carbon steel pipes?
1. Choose a suitable anti-corrosion coating
In order to avoid rusting of carbon steel pipes, an anti-corrosion coating can be added to the surface of the pipe. At present, common anti-corrosion coatings on the market include epoxy paint, polyurethane paint, silicone coating, etc. When choosing an anti-corrosion coating, factors such as the use environment, medium, and working temperature of the pipeline should be considered to select a suitable coating. At the same time, when applying the coating, the thickness and uniformity of the coating should be ensured to ensure complete protection of the pipeline.
2. Clean the pipeline regularly
Pipes will accumulate various corrosive media and impurities during long-term use, which can easily lead to rust. Therefore, the pipeline should be cleaned regularly to ensure the cleanliness of the inside of the pipeline. Before cleaning the pipeline, all the residual media in the pipeline should be removed to avoid secondary contamination of the media during the washing process. In addition, professional washing tools and methods should be used when cleaning the pipeline to ensure that the pipeline is clean and thorough.
3. Strengthen pipeline maintenance
For pipeline maintenance, on the one hand, it is necessary to monitor the use environment of the pipeline, promptly detect abnormal conditions in the pipeline environment, and take measures to reduce the impact of the pipeline on the environment; on the other hand, it is necessary to regularly inspect the pipeline, promptly detect corrosion and wear inside the pipeline, and take measures to repair it. By strengthening pipeline maintenance, the pipeline can be effectively protected, its service life can be extended, and the pipeline can be prevented from rusting.
In summary, underground carbon steel anti-corrosion pipelines often encounter corrosion during use, and appropriate anti-corrosion measures should be selected to extend the service life. The anti-corrosion methods listed above are effective and widely used anti-corrosion measures.