Seamless steel pipe is a steel pipe that is perforated from a whole round steel and has no welds on the surface. It is mainly used as petroleum geological drilling pipe, cracking pipe for petrochemical industry, boiler pipe, bearing pipe and high-precision structural steel pipe for automobile, tractor, aviation, etc. Compared with solid steel such as round steel, when the bending and torsional strength is the same , light weight, is an economical section steel.
The production process of seamless steel pipe includes pre-rolling preparation of billet → billet heating → piercing → rolling → diameter reduction → steel pipe cooling → steel pipe cutting head and tail → segmenting → straightening → flaw detection → manual inspection → marking printing → marking Basic processes such as bale packaging. There are three main deformation processes in the production of seamless steel pipes today: perforation, pipe rolling and diameter reduction. Their respective technological purposes and requirements are as follows:
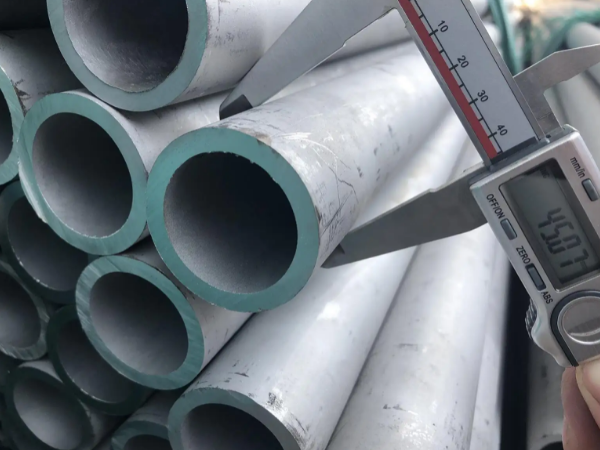
1. Perforation
Perforation is to pass a solid pipe blank into a hollow capillary, and its equipment is called a perforator. The requirements for the perforation process are:
1) It is necessary to ensure that the capillary wall thickness is uniform, the ovality is small, and the geometric dimension accuracy is high;
2) The inner and outer surfaces of the capillary tube are relatively smooth, and there should be no defects such as scarring, folding, and cracks;
3) There must be a corresponding piercing speed and rolling cycle to adapt to the production rhythm of the entire unit, so that the final rolling temperature of the capillary can meet the requirements of the rolling mill.
2. Pipe rolling
Pipe rolling is the process of pressing the perforated thick-walled capillary into a thin-walled steel pipe to achieve the required thermal size and uniformity of the finished pipe. That is, the wall thickness of the steel pipe is determined according to the reduction amount of the subsequent process and the empirical formula to process the wall thickness. This equipment is called a pipe rolling mill. The requirements for the rolling process are:
1) When turning a thick-walled capillary pipe into a thin-walled steel pipe (reduced wall extension), it is first necessary to ensure that the steel pipe has a high wall thickness uniformity;
2) The steel pipe has good inner and outer surface quality. The selection of the pipe rolling mill and the reasonable matching of the deformation amount between the piercing process are the keys to determine the product quality, output and technical and economic indicators of the unit.
3. Determination of diameter reduction (including tension reduction)
The main function of fixing and reducing the diameter is to eliminate the different outer diameters of the steel pipes caused by the rolling process of the previous process, so as to improve the outer diameter accuracy and roundness of the hot-rolled finished pipes. Reduction is the reduction of a large pipe diameter to the required seamless pipe sizes and accuracy.
The production process of seamless steel pipe includes pre-rolling preparation of billet → billet heating → piercing → rolling → diameter reduction → steel pipe cooling → steel pipe cutting head and tail → segmenting → straightening → flaw detection → manual inspection → marking printing → marking Basic processes such as bale packaging. There are three main deformation processes in the production of seamless steel pipes today: perforation, pipe rolling and diameter reduction. Their respective technological purposes and requirements are as follows:
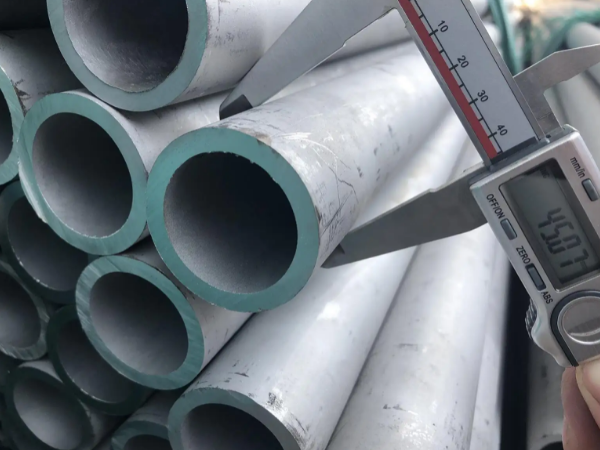
1. Perforation
Perforation is to pass a solid pipe blank into a hollow capillary, and its equipment is called a perforator. The requirements for the perforation process are:
1) It is necessary to ensure that the capillary wall thickness is uniform, the ovality is small, and the geometric dimension accuracy is high;
2) The inner and outer surfaces of the capillary tube are relatively smooth, and there should be no defects such as scarring, folding, and cracks;
3) There must be a corresponding piercing speed and rolling cycle to adapt to the production rhythm of the entire unit, so that the final rolling temperature of the capillary can meet the requirements of the rolling mill.
2. Pipe rolling
Pipe rolling is the process of pressing the perforated thick-walled capillary into a thin-walled steel pipe to achieve the required thermal size and uniformity of the finished pipe. That is, the wall thickness of the steel pipe is determined according to the reduction amount of the subsequent process and the empirical formula to process the wall thickness. This equipment is called a pipe rolling mill. The requirements for the rolling process are:
1) When turning a thick-walled capillary pipe into a thin-walled steel pipe (reduced wall extension), it is first necessary to ensure that the steel pipe has a high wall thickness uniformity;
2) The steel pipe has good inner and outer surface quality. The selection of the pipe rolling mill and the reasonable matching of the deformation amount between the piercing process are the keys to determine the product quality, output and technical and economic indicators of the unit.
3. Determination of diameter reduction (including tension reduction)
The main function of fixing and reducing the diameter is to eliminate the different outer diameters of the steel pipes caused by the rolling process of the previous process, so as to improve the outer diameter accuracy and roundness of the hot-rolled finished pipes. Reduction is the reduction of a large pipe diameter to the required seamless pipe sizes and accuracy.