Preparation before welding
Preheating before welding is a key link in high-pressure boiler tube welding and is very necessary. Because high-pressure boiler tubes are mostly made of alloy materials, such as 12Cr1MoV steel, which has a high carbon content and alloy element content, preheating can slow down the cooling rate of the weld and heat-affected zone, avoid the formation of hardened structure, and also help the escape of hydrogen in the welding area to prevent welding cracks.
The preheating temperature is generally controlled at 200-300℃, and the preheating area is centered on the weld and at least 100mm on both sides.
In terms of the selection of welding materials, manual tungsten inert gas arc welding commonly uses welding wire ER55-B2-MnV, whose weld metal has excellent plasticity and toughness, beautiful weld formation, and good welding performance in all positions; manual arc welding can choose welding rod R317, which is suitable for welding high-temperature and high-pressure pressure-bearing equipment and can meet the welding requirements of high-pressure boiler tubes.
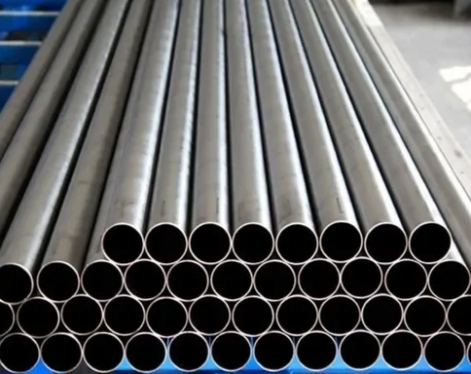
Welding operation steps
1. Argon arc welding primer
After fixing the pipe fitting horizontally, select the appropriate welding current, voltage and argon gas flow rate. Generally, the welding current is 80-120A and the argon gas flow rate is 5-8L/min. Use a short arc when welding, and keep the welding gun as perpendicular to the workpiece surface as possible, with an angle of 75°-85°, which is conducive to the protection of the welding pool by argon gas. The welding gun and welding wire can be slightly swung horizontally, and the swing amplitude is controlled within 2-3mm to ensure that both sides of the groove are melted through.
At the same time, the temperature of the molten pool must be strictly controlled to avoid defects such as welding through due to excessively high temperature or incomplete fusion due to too low temperature. At the joint, the arc pit needs to be polished with an angle grinder. After the arc-closing cracks, pores and other welding defects at the arc pit are cleaned up, the arc welding can be continued.
2. Arc welding filling
When filling welding, short arc is also used, and the heat input should not be too large. If long arc welding is used, not only will there be problems such as unstable arc burning, shallow melting depth, large metal splashes and increased burning loss of alloy elements, but it is also easy to produce defects such as undercut and incomplete penetration.
When welding, a small crescent-shaped wire feeding method can be used, staying on both sides of the groove for 0.5-1 second to ensure that both sides of the groove are fully fused. The welding slag must be thoroughly cleaned between welding layers. Once welding defects such as pores are found, the defective parts must be removed with an angle grinder. When closing the arc, the arc pit must be filled to prevent arc pit cracks. The joints between layers should be staggered to avoid overlap.
3. Arc welding capping
When capping, the welding current should be slightly lower than that of filling, generally reduced by 10-20A. The correct electrode angle should be selected, and the angle with the workpiece surface should be maintained at 70°-80°. The electrode should be moved evenly to prevent undercut defects at the edge of the groove. The weld excess height should be strictly controlled within 1-3mm to avoid stress concentration caused by excessive excess height during use.
Post-weld treatment
After welding, the high-pressure boiler tube needs to be subjected to stress relief heat treatment. Heat the weld as a whole to 720-760℃, keep the temperature constant for 1-2h, and then immediately cover the weld and the near-seam area with insulation material to allow the joint to slowly cool to room temperature. This step is very critical.
On the one hand, it can eliminate or reduce the hardened structure in the heat-affected zone and increase the plasticity and toughness of the joint; on the other hand, it can effectively reduce welding residual stress, and at the same time facilitate the escape of diffused hydrogen, reduce the tendency of cold cracks, and ensure that the high-pressure boiler tube can operate stably under harsh working conditions such as high pressure and high temperature.
Read more: How to Remove Rust from High-Pressure Boiler Tubes
Preheating before welding is a key link in high-pressure boiler tube welding and is very necessary. Because high-pressure boiler tubes are mostly made of alloy materials, such as 12Cr1MoV steel, which has a high carbon content and alloy element content, preheating can slow down the cooling rate of the weld and heat-affected zone, avoid the formation of hardened structure, and also help the escape of hydrogen in the welding area to prevent welding cracks.
The preheating temperature is generally controlled at 200-300℃, and the preheating area is centered on the weld and at least 100mm on both sides.
In terms of the selection of welding materials, manual tungsten inert gas arc welding commonly uses welding wire ER55-B2-MnV, whose weld metal has excellent plasticity and toughness, beautiful weld formation, and good welding performance in all positions; manual arc welding can choose welding rod R317, which is suitable for welding high-temperature and high-pressure pressure-bearing equipment and can meet the welding requirements of high-pressure boiler tubes.
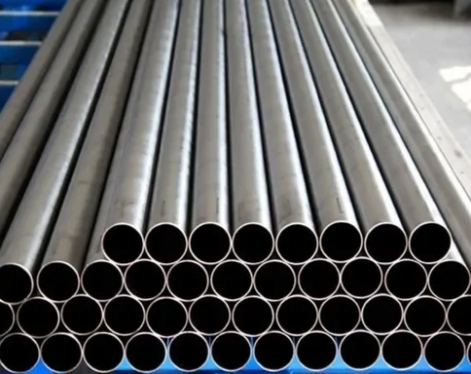
Welding operation steps
1. Argon arc welding primer
After fixing the pipe fitting horizontally, select the appropriate welding current, voltage and argon gas flow rate. Generally, the welding current is 80-120A and the argon gas flow rate is 5-8L/min. Use a short arc when welding, and keep the welding gun as perpendicular to the workpiece surface as possible, with an angle of 75°-85°, which is conducive to the protection of the welding pool by argon gas. The welding gun and welding wire can be slightly swung horizontally, and the swing amplitude is controlled within 2-3mm to ensure that both sides of the groove are melted through.
At the same time, the temperature of the molten pool must be strictly controlled to avoid defects such as welding through due to excessively high temperature or incomplete fusion due to too low temperature. At the joint, the arc pit needs to be polished with an angle grinder. After the arc-closing cracks, pores and other welding defects at the arc pit are cleaned up, the arc welding can be continued.
2. Arc welding filling
When filling welding, short arc is also used, and the heat input should not be too large. If long arc welding is used, not only will there be problems such as unstable arc burning, shallow melting depth, large metal splashes and increased burning loss of alloy elements, but it is also easy to produce defects such as undercut and incomplete penetration.
When welding, a small crescent-shaped wire feeding method can be used, staying on both sides of the groove for 0.5-1 second to ensure that both sides of the groove are fully fused. The welding slag must be thoroughly cleaned between welding layers. Once welding defects such as pores are found, the defective parts must be removed with an angle grinder. When closing the arc, the arc pit must be filled to prevent arc pit cracks. The joints between layers should be staggered to avoid overlap.
3. Arc welding capping
When capping, the welding current should be slightly lower than that of filling, generally reduced by 10-20A. The correct electrode angle should be selected, and the angle with the workpiece surface should be maintained at 70°-80°. The electrode should be moved evenly to prevent undercut defects at the edge of the groove. The weld excess height should be strictly controlled within 1-3mm to avoid stress concentration caused by excessive excess height during use.
Post-weld treatment
After welding, the high-pressure boiler tube needs to be subjected to stress relief heat treatment. Heat the weld as a whole to 720-760℃, keep the temperature constant for 1-2h, and then immediately cover the weld and the near-seam area with insulation material to allow the joint to slowly cool to room temperature. This step is very critical.
On the one hand, it can eliminate or reduce the hardened structure in the heat-affected zone and increase the plasticity and toughness of the joint; on the other hand, it can effectively reduce welding residual stress, and at the same time facilitate the escape of diffused hydrogen, reduce the tendency of cold cracks, and ensure that the high-pressure boiler tube can operate stably under harsh working conditions such as high pressure and high temperature.
Read more: How to Remove Rust from High-Pressure Boiler Tubes