Common welding methods for stainless steel pipes include TIG welding and MIG welding. TIG welding is a form of manual welding that requires a high degree of technical skill but can result in very high quality welds. MIG welding is an automated welding method that is fast and easy to operate. Choosing the appropriate welding method can ensure the welding quality of stainless steel pipes and make them strong and durable.
What is Tungsten Inert Gas (GTAW or TIG) Welding?
"TIG (Tungsten Inert Gas) welding" stands for "inert gas welding". This is a kind of arc welding that does not splash sparks and supports the welding of stainless steel, aluminum, iron and other metals. It uses tungsten, which is not consumed as a discharge electrode, and uses inert gases such as argon and helium as protective gases. An arc is generated in an inert gas, and the base metal is melted by the heat of the arc for welding. Although welding materials are also used, since the welding part is surrounded by inert gas, the arc is also very stable and almost no sputtering occurs.
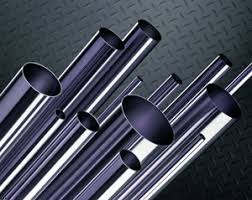
Advantages of TIG welding
(1) Almost all metals or alloys can be welded;
(2) The welding quality is good (the weld is clean, well-shaped, and the heat-affected zone is small);
(3) Suitable for thin plates and bottoming/all-position welding;
(4) No splashing.
What are the main disadvantages of TIG welding?
1) Welding efficiency is lower than other methods. to
2) Argon gas has no deoxidation or dehydrogenation effect, so the preparation work such as oil removal, rust removal, and water removal before welding is strictly required, otherwise it is easy to produce pores and affect the quality of the weld.
3) A small amount of tungsten electrode melts and evaporates during welding. If tungsten particles enter the molten pool, they will cause tungsten inclusion, which will affect the quality of the weld, especially when the current is too large.
4) A small amount of tungsten electrode melts and evaporates during welding. If tungsten particles enter the molten pool, tungsten will be trapped, which will affect the quality of the weld, especially when the current is too large.
What does MIG stand for in welding?
"MIG (Metal Inert Gas) welding" is arc welding. Like TIG welding, inert gas is used as a protective gas, but MIG welding is an electrode consumption welding method that melts the discharge electrode. It is usually used for joining stainless steel and aluminum alloys, and the shielding gas can be used according to the welding materials.
What is the difference between TIG and MIG?
1. Differences in shielding gas: MIG welding is generally protected by argon gas; TIG generally uses carbon dioxide active gas mixed with argon gas.
2. Difference between tungsten arc and TIG welding: TIG welding can still burn stably even at a very small welding current (<10A); MIG welding does not use tungsten electrode, and the cost is lower than TIG welding.
3. Applicable differences: TIG welding is especially suitable for welding thin plates and ultra-thin plate materials; MIG welding is suitable for welding aluminum and aluminum alloys, copper and copper alloys, stainless steel and other materials.
Is MIG or TIG better for stainless steel welded tube?
To sum up, MIG welding is more suitable for welding stainless steel pipes. During the welding process of stainless steel pipes, you need to pay attention to several skills. First of all, be sure to ensure that the welding surface is clean. Any oil, oxidation or rust must be removed. Secondly, we must strictly follow the welding process requirements of stainless steel pipes to ensure welding quality. Finally, after welding, the weld seam needs to be processed, such as grinding, cutting, etc., to ensure the quality of the welding surface.
What is Tungsten Inert Gas (GTAW or TIG) Welding?
"TIG (Tungsten Inert Gas) welding" stands for "inert gas welding". This is a kind of arc welding that does not splash sparks and supports the welding of stainless steel, aluminum, iron and other metals. It uses tungsten, which is not consumed as a discharge electrode, and uses inert gases such as argon and helium as protective gases. An arc is generated in an inert gas, and the base metal is melted by the heat of the arc for welding. Although welding materials are also used, since the welding part is surrounded by inert gas, the arc is also very stable and almost no sputtering occurs.
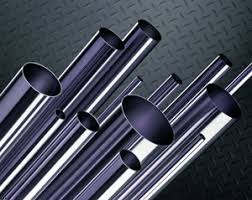
Advantages of TIG welding
(1) Almost all metals or alloys can be welded;
(2) The welding quality is good (the weld is clean, well-shaped, and the heat-affected zone is small);
(3) Suitable for thin plates and bottoming/all-position welding;
(4) No splashing.
What are the main disadvantages of TIG welding?
1) Welding efficiency is lower than other methods. to
2) Argon gas has no deoxidation or dehydrogenation effect, so the preparation work such as oil removal, rust removal, and water removal before welding is strictly required, otherwise it is easy to produce pores and affect the quality of the weld.
3) A small amount of tungsten electrode melts and evaporates during welding. If tungsten particles enter the molten pool, they will cause tungsten inclusion, which will affect the quality of the weld, especially when the current is too large.
4) A small amount of tungsten electrode melts and evaporates during welding. If tungsten particles enter the molten pool, tungsten will be trapped, which will affect the quality of the weld, especially when the current is too large.
What does MIG stand for in welding?
"MIG (Metal Inert Gas) welding" is arc welding. Like TIG welding, inert gas is used as a protective gas, but MIG welding is an electrode consumption welding method that melts the discharge electrode. It is usually used for joining stainless steel and aluminum alloys, and the shielding gas can be used according to the welding materials.
What is the difference between TIG and MIG?
1. Differences in shielding gas: MIG welding is generally protected by argon gas; TIG generally uses carbon dioxide active gas mixed with argon gas.
2. Difference between tungsten arc and TIG welding: TIG welding can still burn stably even at a very small welding current (<10A); MIG welding does not use tungsten electrode, and the cost is lower than TIG welding.
3. Applicable differences: TIG welding is especially suitable for welding thin plates and ultra-thin plate materials; MIG welding is suitable for welding aluminum and aluminum alloys, copper and copper alloys, stainless steel and other materials.
Is MIG or TIG better for stainless steel welded tube?
To sum up, MIG welding is more suitable for welding stainless steel pipes. During the welding process of stainless steel pipes, you need to pay attention to several skills. First of all, be sure to ensure that the welding surface is clean. Any oil, oxidation or rust must be removed. Secondly, we must strictly follow the welding process requirements of stainless steel pipes to ensure welding quality. Finally, after welding, the weld seam needs to be processed, such as grinding, cutting, etc., to ensure the quality of the welding surface.
Previous:Welded pipe nipple/Welded nipples
Next:ERW pipe meaning