In the manufacturing process of welded pipes such as stainless steel welded pipes, welded nipple refers to the joint where two or more parts are combined by welding. It also refers to a joint where two or more parts are connected by welding, including welds, fusion zones and heat-affected zones.
forms of welded nipples
Classified according to the mutual structural position of the two metal parts to be welded. There are four main types of welded nipples: butt nipples, T-shaped nipples, corner nipples and lap nipples.
1. Butt nipple
Butt nipples are the most common and reasonable form of joints. A joint in which the surfaces of two weldments are relatively parallel is called a butt joint, which is the most commonly used joint form in welded structures today. According to conditions such as the thickness of the weldment, welding method and groove preparation, butt joints can be divided into two types: butt joints without grooves and butt joints with grooves.
(1)Butt nipple without bevel
When the thickness of the steel plate is less than 6mm, generally no beveling is required, leaving only an assembly gap of 1-2mm. But this is not absolute. In important welding structures, when the thickness of the workpiece is greater than 3mm, beveling is required.
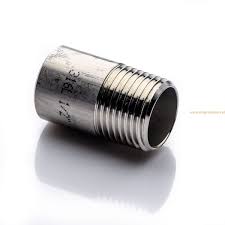
(2) Beveled butt nipple
Beveling is a joint that uses machinery, flame or arc methods to process the welding joint into a certain geometric shape (bevel) and then weld it. The purpose of beveling is to ensure that the arc can reach the root of the joint, so that the root of the joint can be welded through and the slag can be easily removed, so as to obtain a good weld shape. Moreover, the groove can play a role in adjusting the proportion of base metal and filler metal in the weld metal. The blunt edge (when the weldment is beveled, the end face portion is left along the thickness direction of the weldment) is to ensure penetration of the root of the joint.
The groove is divided into the following V, X and U-shaped interfaces
a. V-shaped groove
When the thickness of the steel plate exceeds 7mm, V-shaped grooves are generally used. There are four types of V-shaped bevels: V-shaped bevels without blunt edges, V-shaped bevels with blunt edges, single-sided blunt-edge V-shaped bevels and single-sided bevels. The V-shaped groove is characterized by easy processing, but the corner deformation is large after welding.
b. X-shaped groove
When the thickness of the steel plate exceeds 12mm, an X-shaped groove, also known as a double-sided V-shaped groove, must be used. Compared with a V-shaped groove, an X-shaped groove can reduce the amount of welded metal by about 1/2. The deformation and internal stress generated after welding are also small. Therefore, this kind of groove is mostly used in structures with large thickness and where the amount of welding deformation needs to be controlled.
c.U-shaped groove
U-shaped grooves can be divided into single-sided, single-sided U-shaped grooves and double-sided U-shaped grooves. U-shaped groove When the maximum thickness of the steel plate is 20-60mm, a single-sided U-shaped groove is used. When the board thickness is 40--60mm, double-sided U-shaped grooves are used. The U-shaped groove is characterized by a small amount of filler metal, small deformation of the weldment, and a small proportion of the base metal in the weld metal. However, this type of groove is difficult to process and is generally used in more important welding structures.
2. T-shaped nipple
A joint in which the end face of a weldment forms a right angle or a nearly right angle with the plane of another weldment is called a T-shaped joint. T-shaped joints are widely used in steel structural parts. According to the thickness of the weldment, they can be divided into four forms: no groove, single-sided V-shaped, K-shaped and double V-shaped grooves.
As a general connection weld, the T-shaped nipple does not need to be grooved when the steel plate thickness is 2-30mm, thus omitting the preparation and processing of the groove. When the weld of T-shaped nipple is required to bear load, V-shaped, K-shaped, or double V-shaped grooves should be selected according to the steel plate thickness and structural strength requirements to ensure the strength of the joint.
3. Corner connection nipple
The end faces of two welding parts form a joint with an included angle greater than 30° and less than 135°, which is called a nipple. It is generally used in unimportant welding structures.
4.Overlap nipple
The nipple formed by the partial overlap of two welding parts is called an overlap nipple. The overlap nipple is generally used for steel plates below 12mm. The overlapping portion is generally 3-5 times the thickness of the plate and is welded on both sides. This kind of nipple has low assembly requirements and is easy to weld and construct. However, the load-bearing capacity is low, so it can only be used in unimportant structures. In chemical containers, opening reinforcement, support linings and other structures generally adopt the lapped nipple form.
forms of welded nipples
Classified according to the mutual structural position of the two metal parts to be welded. There are four main types of welded nipples: butt nipples, T-shaped nipples, corner nipples and lap nipples.
1. Butt nipple
Butt nipples are the most common and reasonable form of joints. A joint in which the surfaces of two weldments are relatively parallel is called a butt joint, which is the most commonly used joint form in welded structures today. According to conditions such as the thickness of the weldment, welding method and groove preparation, butt joints can be divided into two types: butt joints without grooves and butt joints with grooves.
(1)Butt nipple without bevel
When the thickness of the steel plate is less than 6mm, generally no beveling is required, leaving only an assembly gap of 1-2mm. But this is not absolute. In important welding structures, when the thickness of the workpiece is greater than 3mm, beveling is required.
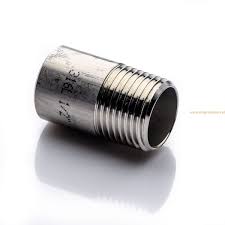
(2) Beveled butt nipple
Beveling is a joint that uses machinery, flame or arc methods to process the welding joint into a certain geometric shape (bevel) and then weld it. The purpose of beveling is to ensure that the arc can reach the root of the joint, so that the root of the joint can be welded through and the slag can be easily removed, so as to obtain a good weld shape. Moreover, the groove can play a role in adjusting the proportion of base metal and filler metal in the weld metal. The blunt edge (when the weldment is beveled, the end face portion is left along the thickness direction of the weldment) is to ensure penetration of the root of the joint.
The groove is divided into the following V, X and U-shaped interfaces
a. V-shaped groove
When the thickness of the steel plate exceeds 7mm, V-shaped grooves are generally used. There are four types of V-shaped bevels: V-shaped bevels without blunt edges, V-shaped bevels with blunt edges, single-sided blunt-edge V-shaped bevels and single-sided bevels. The V-shaped groove is characterized by easy processing, but the corner deformation is large after welding.
b. X-shaped groove
When the thickness of the steel plate exceeds 12mm, an X-shaped groove, also known as a double-sided V-shaped groove, must be used. Compared with a V-shaped groove, an X-shaped groove can reduce the amount of welded metal by about 1/2. The deformation and internal stress generated after welding are also small. Therefore, this kind of groove is mostly used in structures with large thickness and where the amount of welding deformation needs to be controlled.
c.U-shaped groove
U-shaped grooves can be divided into single-sided, single-sided U-shaped grooves and double-sided U-shaped grooves. U-shaped groove When the maximum thickness of the steel plate is 20-60mm, a single-sided U-shaped groove is used. When the board thickness is 40--60mm, double-sided U-shaped grooves are used. The U-shaped groove is characterized by a small amount of filler metal, small deformation of the weldment, and a small proportion of the base metal in the weld metal. However, this type of groove is difficult to process and is generally used in more important welding structures.
2. T-shaped nipple
A joint in which the end face of a weldment forms a right angle or a nearly right angle with the plane of another weldment is called a T-shaped joint. T-shaped joints are widely used in steel structural parts. According to the thickness of the weldment, they can be divided into four forms: no groove, single-sided V-shaped, K-shaped and double V-shaped grooves.
As a general connection weld, the T-shaped nipple does not need to be grooved when the steel plate thickness is 2-30mm, thus omitting the preparation and processing of the groove. When the weld of T-shaped nipple is required to bear load, V-shaped, K-shaped, or double V-shaped grooves should be selected according to the steel plate thickness and structural strength requirements to ensure the strength of the joint.
3. Corner connection nipple
The end faces of two welding parts form a joint with an included angle greater than 30° and less than 135°, which is called a nipple. It is generally used in unimportant welding structures.
4.Overlap nipple
The nipple formed by the partial overlap of two welding parts is called an overlap nipple. The overlap nipple is generally used for steel plates below 12mm. The overlapping portion is generally 3-5 times the thickness of the plate and is welded on both sides. This kind of nipple has low assembly requirements and is easy to weld and construct. However, the load-bearing capacity is low, so it can only be used in unimportant structures. In chemical containers, opening reinforcement, support linings and other structures generally adopt the lapped nipple form.