ERW pipe is a common metal pipe material, which is processed into round or square pipes. ERW welded pipe has the advantages of strong bearing capacity, convenient processing and light weight, so it is widely used in automobile manufacturing. At present, ERW welded pipe is mainly used in automobile body structure and chassis suspension. The application of ERW pipe can reduce the weight of the whole vehicle, improve the performance and fuel economy of the vehicle, and also reduce the generation of waste and environmental pollution.
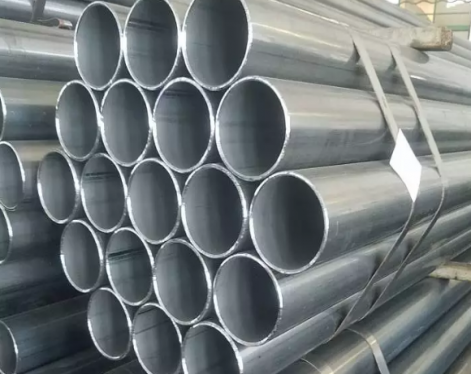
Application of ERW pipe in automobile manufacturing:
In automobile manufacturing, ERW welded pipe has a wide range of applications.
First, ERW welded pipe can be used for structural parts such as automobile frame and chassis. These parts need to bear large loads and stresses, and the high strength and good welding performance of straight seam welded pipe can meet the requirements.
Secondly, ERW welded pipe can be used in pipeline systems such as automobile exhaust pipes and fuel pipes. These pipes need to have good sealing and corrosion resistance, and the welded pipe can meet the requirements through surface treatment and other methods.
Furthermore, ERW welded pipe can also be used for interior parts such as automobile seat frames and armrests. ERW welded pipes have strong machinability and can be bent, welded and other processing operations according to design requirements to meet different interior design requirements.
In addition to its application in automobile manufacturing, ERW welded pipes are also widely used in the production of automobile parts. For example, some automobile parts, such as exhaust pipes, front suspension systems, etc., are made of welded pipes. The advantages of these parts are light weight, good durability, high reliability, and can improve the overall performance of the car.
Advantages and disadvantages of ERW welded pipes in the automotive industry:
Advantages:
1. High production efficiency: The production process of ERW welded pipes has a high degree of automation, significant production efficiency, and is suitable for large-scale production.
2. Low cost: Due to the high material utilization rate in the production process and the absence of additional filler metal, the overall cost is low.
3. High dimensional accuracy: The geometric dimensional accuracy of ERW welded pipes is high, and the surface is smooth, flat and beautiful.
4. Good welding quality: By optimizing the welding process and automated detection technology, the welding quality of ERW welded pipes is high and the probability of missed defects is low.
5. Wide range of applications: ERW welded pipes are widely used in oil and natural gas pipelines, especially in submarine pipelines, which shows their superiority.
Disadvantages:
1. Weld performance problems: Due to the fast heating speed and large temperature gradient during welding, ERW welded pipes may cause hardening phase and tissue stress in the weld area, affecting the mechanical properties of the weld.
2. Poor low-temperature toughness: Some ERW welded pipes have poor low-temperature toughness and high FATT values, which limits their use in cold areas.
3. Applicable caliber restrictions: ERW welded pipes are mainly suitable for small and medium-sized diameter pipelines, and the production and application of large-diameter pipelines are relatively small.
Future development trend of ERW welded pipes in the automotive industry:
With the development of the automotive industry and the increasing requirements of society for environmental protection, ERW welded pipes are being used more and more widely in the automotive industry. In the future, the design and production technology of welded pipes will be further improved and developed, and the quality and performance of welded pipes will become better and better. At the same time, the production process of welded pipes will become more environmentally friendly and energy-saving to meet people's requirements for environmental protection. It is expected that the application scope of welded pipes in the automotive industry will be further expanded in the future.
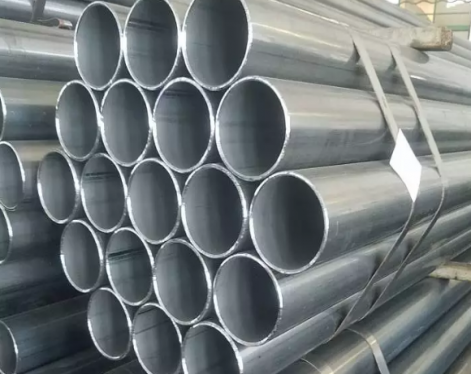
Application of ERW pipe in automobile manufacturing:
In automobile manufacturing, ERW welded pipe has a wide range of applications.
First, ERW welded pipe can be used for structural parts such as automobile frame and chassis. These parts need to bear large loads and stresses, and the high strength and good welding performance of straight seam welded pipe can meet the requirements.
Secondly, ERW welded pipe can be used in pipeline systems such as automobile exhaust pipes and fuel pipes. These pipes need to have good sealing and corrosion resistance, and the welded pipe can meet the requirements through surface treatment and other methods.
Furthermore, ERW welded pipe can also be used for interior parts such as automobile seat frames and armrests. ERW welded pipes have strong machinability and can be bent, welded and other processing operations according to design requirements to meet different interior design requirements.
In addition to its application in automobile manufacturing, ERW welded pipes are also widely used in the production of automobile parts. For example, some automobile parts, such as exhaust pipes, front suspension systems, etc., are made of welded pipes. The advantages of these parts are light weight, good durability, high reliability, and can improve the overall performance of the car.
Advantages and disadvantages of ERW welded pipes in the automotive industry:
Advantages:
1. High production efficiency: The production process of ERW welded pipes has a high degree of automation, significant production efficiency, and is suitable for large-scale production.
2. Low cost: Due to the high material utilization rate in the production process and the absence of additional filler metal, the overall cost is low.
3. High dimensional accuracy: The geometric dimensional accuracy of ERW welded pipes is high, and the surface is smooth, flat and beautiful.
4. Good welding quality: By optimizing the welding process and automated detection technology, the welding quality of ERW welded pipes is high and the probability of missed defects is low.
5. Wide range of applications: ERW welded pipes are widely used in oil and natural gas pipelines, especially in submarine pipelines, which shows their superiority.
Disadvantages:
1. Weld performance problems: Due to the fast heating speed and large temperature gradient during welding, ERW welded pipes may cause hardening phase and tissue stress in the weld area, affecting the mechanical properties of the weld.
2. Poor low-temperature toughness: Some ERW welded pipes have poor low-temperature toughness and high FATT values, which limits their use in cold areas.
3. Applicable caliber restrictions: ERW welded pipes are mainly suitable for small and medium-sized diameter pipelines, and the production and application of large-diameter pipelines are relatively small.
Future development trend of ERW welded pipes in the automotive industry:
With the development of the automotive industry and the increasing requirements of society for environmental protection, ERW welded pipes are being used more and more widely in the automotive industry. In the future, the design and production technology of welded pipes will be further improved and developed, and the quality and performance of welded pipes will become better and better. At the same time, the production process of welded pipes will become more environmentally friendly and energy-saving to meet people's requirements for environmental protection. It is expected that the application scope of welded pipes in the automotive industry will be further expanded in the future.