Overview of the cold rolling manufacturing process of seamless steel pipes:
The cold rolling manufacturing process of seamless steel pipes is a process that forms seamless steel pipes through multiple rolling and stretching processes of steel billets. Compared with the hot rolling manufacturing process, the cold rolling manufacturing process can ensure that the internal quality of the steel pipe is more uniform, the surface is smoother, and the size is more precise, so it is widely used in occasions with high precision requirements.
Seamless steel pipe cold rolling manufacturing process:
1. Raw material selection
The raw material of the cold rolling manufacturing process of seamless steel pipes is steel billets, which generally use high-quality low-carbon steel, low-alloy steel and high-alloy steel. The choice of raw materials has a great influence on the quality of the finished product, so raw materials with stable quality must be selected.
2. Heating
The steel billet is heated to a suitable temperature, generally around 1000℃. The purpose of heating is to make the steel billet softer and facilitate subsequent rolling and stretching.
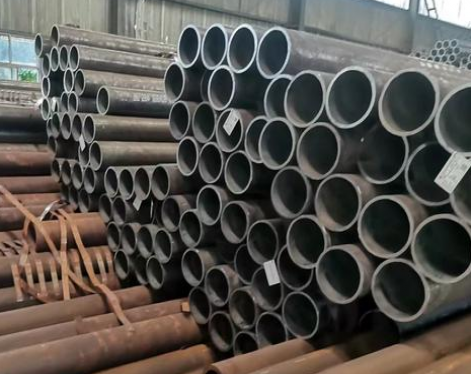
3. Rolling
The heated steel billet is rolled through a rolling mill. During the rolling process, the steel billet gradually deforms into a round shape until it becomes the shape of a seamless steel pipe.
4. Stretching
The rolled seamless steel pipe is stretched through a stretching machine to further improve the dimensional accuracy and surface quality of the steel pipe.
5. Cold rolling
The stretched seamless steel pipe is cold rolled through a cold coiling machine to further improve the dimensional accuracy and surface quality of the steel pipe.
6. Heat treatment
The cold rolled seamless steel pipe is heat treated to eliminate internal stress and tissue defects and improve the performance of the steel pipe.
Advantages and disadvantages of cold-rolled seamless pipes:
Advantages:
(1) High processing accuracy: The cold rolling production process has high processing accuracy and can produce seamless steel pipes with precise dimensions to meet high precision requirements.
(2) High surface finish: Due to the low temperature of the cold rolling production process, the surface finish of the steel pipe can be maintained, and seamless steel pipes with beautiful appearance can be produced.
(3) High strength: The cold rolling production process makes the grains of the steel pipe fine and evenly distributed, the steel pipe has high strength and good corrosion resistance.
Disadvantages:
(1) High cost: The cost of the cold rolling production process is higher than that of hot rolling production, mainly due to the high equipment and energy costs of the cold rolling process.
(2) Low production efficiency: The cold rolling production process has low production efficiency, slow processing speed, and a small number of steel pipes produced.
Characteristics and applications of cold-rolled seamless steel pipes:
The biggest characteristics of cold-rolled seamless steel pipes are no joints, smooth surface, precise dimensions, high strength, strong pressure resistance, and corrosion resistance. This makes it widely used in some specific industrial fields. For example, core parts such as drive shafts and gasoline injectors in the automotive industry require high-strength and high-precision cold-rolled seamless steel pipes. Similarly, cold-rolled seamless steel pipes are also widely used in high-precision equipment and engineering projects in the fields of aviation, petroleum, and chemical industry.
Requirements for equipment for cold rolling manufacturing process of seamless steel pipes:
The equipment required for the cold rolling manufacturing process of seamless steel pipes mainly includes heating furnaces, rolling mills, stretching machines, cold coiling machines, heat treatment furnaces, etc. The quality and performance of these equipment directly affect the quality of the finished product, so reliable equipment must be selected.
FAQ:
1. What is the difference between cold rolling and hot rolling manufacturing processes for seamless steel pipes?
Cold rolling of seamless steel pipes is more expensive than hot rolling manufacturing processes, but it can achieve higher dimensional accuracy and surface quality.
2. What are the advantages of cold rolling manufacturing processes for seamless steel pipes?
The cold rolling manufacturing process for seamless steel pipes can ensure that the internal quality of the steel pipe is more uniform, the surface is smoother, and the size is more accurate, so it is widely used in high-precision occasions.
Conclusion:
The cold rolling manufacturing process for seamless steel pipes is a high-precision processing technology that requires the selection of reliable raw materials and equipment to ensure the quality of the finished product. At the same time, it is also necessary to pay attention to the control of the process flow and the solution of common problems to achieve the optimal processing effect.
The cold rolling manufacturing process of seamless steel pipes is a process that forms seamless steel pipes through multiple rolling and stretching processes of steel billets. Compared with the hot rolling manufacturing process, the cold rolling manufacturing process can ensure that the internal quality of the steel pipe is more uniform, the surface is smoother, and the size is more precise, so it is widely used in occasions with high precision requirements.
Seamless steel pipe cold rolling manufacturing process:
1. Raw material selection
The raw material of the cold rolling manufacturing process of seamless steel pipes is steel billets, which generally use high-quality low-carbon steel, low-alloy steel and high-alloy steel. The choice of raw materials has a great influence on the quality of the finished product, so raw materials with stable quality must be selected.
2. Heating
The steel billet is heated to a suitable temperature, generally around 1000℃. The purpose of heating is to make the steel billet softer and facilitate subsequent rolling and stretching.
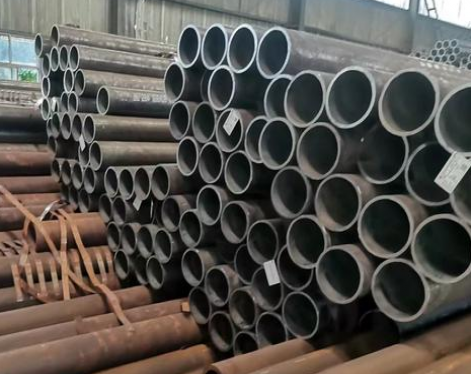
3. Rolling
The heated steel billet is rolled through a rolling mill. During the rolling process, the steel billet gradually deforms into a round shape until it becomes the shape of a seamless steel pipe.
4. Stretching
The rolled seamless steel pipe is stretched through a stretching machine to further improve the dimensional accuracy and surface quality of the steel pipe.
5. Cold rolling
The stretched seamless steel pipe is cold rolled through a cold coiling machine to further improve the dimensional accuracy and surface quality of the steel pipe.
6. Heat treatment
The cold rolled seamless steel pipe is heat treated to eliminate internal stress and tissue defects and improve the performance of the steel pipe.
Advantages and disadvantages of cold-rolled seamless pipes:
Advantages:
(1) High processing accuracy: The cold rolling production process has high processing accuracy and can produce seamless steel pipes with precise dimensions to meet high precision requirements.
(2) High surface finish: Due to the low temperature of the cold rolling production process, the surface finish of the steel pipe can be maintained, and seamless steel pipes with beautiful appearance can be produced.
(3) High strength: The cold rolling production process makes the grains of the steel pipe fine and evenly distributed, the steel pipe has high strength and good corrosion resistance.
Disadvantages:
(1) High cost: The cost of the cold rolling production process is higher than that of hot rolling production, mainly due to the high equipment and energy costs of the cold rolling process.
(2) Low production efficiency: The cold rolling production process has low production efficiency, slow processing speed, and a small number of steel pipes produced.
Characteristics and applications of cold-rolled seamless steel pipes:
The biggest characteristics of cold-rolled seamless steel pipes are no joints, smooth surface, precise dimensions, high strength, strong pressure resistance, and corrosion resistance. This makes it widely used in some specific industrial fields. For example, core parts such as drive shafts and gasoline injectors in the automotive industry require high-strength and high-precision cold-rolled seamless steel pipes. Similarly, cold-rolled seamless steel pipes are also widely used in high-precision equipment and engineering projects in the fields of aviation, petroleum, and chemical industry.
Requirements for equipment for cold rolling manufacturing process of seamless steel pipes:
The equipment required for the cold rolling manufacturing process of seamless steel pipes mainly includes heating furnaces, rolling mills, stretching machines, cold coiling machines, heat treatment furnaces, etc. The quality and performance of these equipment directly affect the quality of the finished product, so reliable equipment must be selected.
FAQ:
1. What is the difference between cold rolling and hot rolling manufacturing processes for seamless steel pipes?
Cold rolling of seamless steel pipes is more expensive than hot rolling manufacturing processes, but it can achieve higher dimensional accuracy and surface quality.
2. What are the advantages of cold rolling manufacturing processes for seamless steel pipes?
The cold rolling manufacturing process for seamless steel pipes can ensure that the internal quality of the steel pipe is more uniform, the surface is smoother, and the size is more accurate, so it is widely used in high-precision occasions.
Conclusion:
The cold rolling manufacturing process for seamless steel pipes is a high-precision processing technology that requires the selection of reliable raw materials and equipment to ensure the quality of the finished product. At the same time, it is also necessary to pay attention to the control of the process flow and the solution of common problems to achieve the optimal processing effect.