ASTM A209 is a standard specification for seamless carbon-molybdenum alloy-steel boiler and superheater tubes.
This standard applies to seamless steel tubes with an outside diameter of 1/2 to 5 inches (12.7~127mm) and a minimum wall thickness of 0.035 to 0.500 inches (0.9~12.70mm).1. Manufacturing process of ASTM A209
① Steel manufacturing-the steel should be killed steel
② The steel tube should be manufactured by seamless steel tube process and made into hot-finished or cold-finished steel tubes as specified.
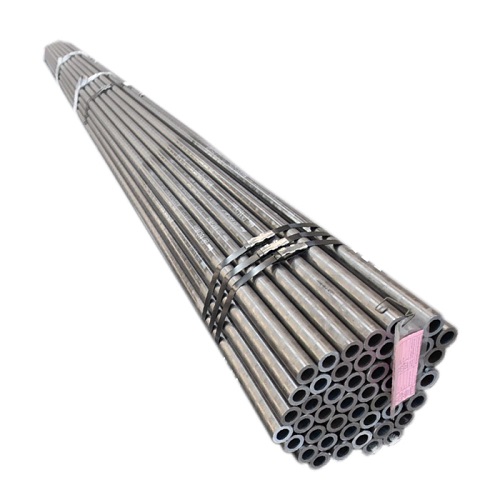
2. Heat treatment
Hot-finished tubes should be heat treated at 1200°F (650℃) or higher. Cold-finished tubes should be heat treated at 1200°F (650℃) or higher in the last cold working pass, or the steel tubes should be delivered in fully annealed, isothermally annealed or normalized and tempered state. If the steel pipe is delivered in the normalized and tempered condition, the minimum tempering temperature is 1200°F (650°C).
3.Chemical composition
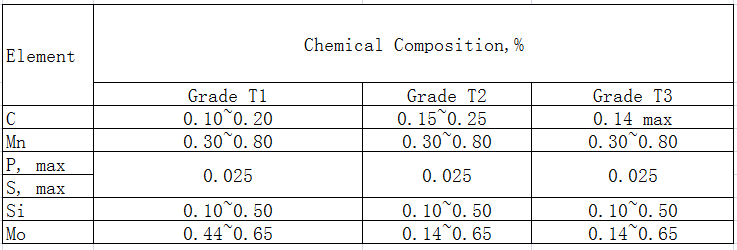
Table 1 Chemical composition requirements
4.Finished product analysis
① The manufacturer shall take one billet or one steel tube from each furnace for analysis. The measured chemical composition shall meet the specified requirements.
② If the finished product fails the initial test, two more billets or steel tubes shall be taken for retesting. Both retests of each element must meet the standard requirements; otherwise, the furnace or batch (Note 1) shall be scrapped; or the supplier shall decide whether each billet or steel tube shall be analyzed and accepted separately. Unqualified billets or steel tubes shall be scrapped.
Note 1. For flattening inspection and expansion inspection, "batch" refers to all steel tubes produced from the same furnace, with the same nominal size, the same wall thickness, and not yet cut. If the final heat treatment is carried out in a batch furnace, the batch shall refer only to steel tubes with the same furnace number, the same size, and the same furnace heat treatment. If the final heat treatment is carried out in a continuous furnace, the number of steel tubes with the same furnace number and the same size in a batch shall be determined according to the steel tube size according to Table 2.
2. For the tensile test and hardness test, a batch refers to all the steel tubes produced by the same furnace, with the same nominal diameter and wall thickness, which have not been cut. If the final treatment is carried out in a batch furnace, the batch should only refer to the steel tubes with the same size, the same furnace number and the same furnace heat treatment. If the final treatment is carried out in a continuous furnace, a batch should include all the steel tubes with the same size, the same furnace number and the same temperature, heating time and furnace speed in the same heat treatment furnace.
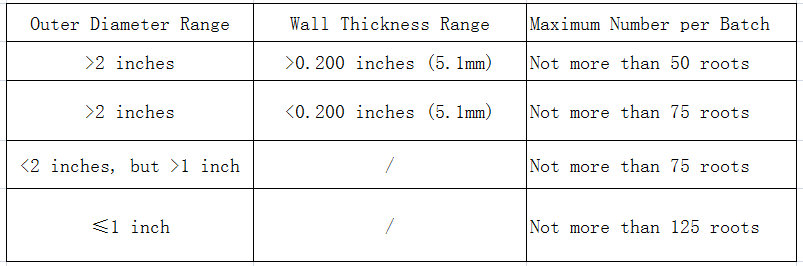
Table 2 The number of steel pipes per batch treated by continuous heat treatment process
5.Hardness requirements
The hardness of the steel pipe shall not exceed the values listed in Table 3.
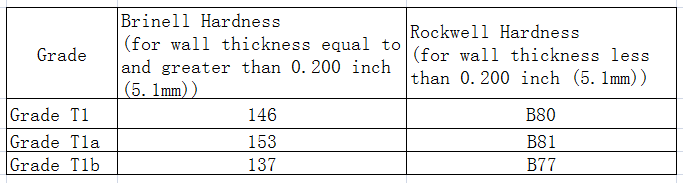
Table 3 Hardness requi rements
6.Mechanical tests required
① Tensile test - Take samples from each batch of no more than 50 steel pipes for a tensile test. Take samples from each batch of more than 50 steel pipes for two tensile tests (Note 2).
② Flattening test - Take a completed steel pipe from each batch, but not the one used for expansion test, and take samples from each end for an external flattening test (Note 2).
③ Expanding test - Take a completed steel pipe from each batch, but not the one used for flattening test, and take samples from each end for an expansion test (Note 1).
④ Hardness test - Take two steel pipes from each batch and take samples for Brinell or Rockwell hardness test (Note 2).
⑤ Hydraulic test - Each steel pipe must be subjected to hydraulic test. Non-destructive testing can be used instead of hydraulic test upon the purchaser's designation.
7. Forming operation
After the steel pipe is inserted into the boiler, it can withstand the expansion and crimping operation without cracks or cracks. Under normal operation, the superheater steel pipe should be able to withstand the necessary forging, welding and bending during production without defects.
8. Marking
In addition to the markings specified in ASTM A450/A450M, it should also include the marking of hot-processed pipes or cold-processed pipes.