Carbon steel erw pipe, also known as electric resistance welding, is a tubular product with a longitudinal weld formed by fusing the edges of steel plates or strips together through resistance welding. It is widely used in oil and gas pipelines, building structure support, and machinery manufacturing due to its mature manufacturing process, relatively low cost, and ability to meet various high and low pressure requirements.
Carbon steel erw pipe production process steps
1. Raw material preparation
To produce carbon steel ERW pipes, we must first select suitable carbon steel strip as raw material. The material, thickness, width and other parameters of the steel strip must strictly comply with production standards. For example, common carbon steel materials such as Q195 and Q235 have clear range requirements for their carbon content, sulfur and phosphorus content and other chemical compositions. The quality of raw materials is directly related to the quality of finished products. High-quality steel strips can ensure that the steel pipe has good strength and toughness. For example, in oil pipelines, the steel pipe needs to be strong enough to withstand the internal oil pressure.
2. Uncoiling and leveling
The coiled carbon steel strip is slowly unrolled using an uncoiler. Since the steel strip will produce unevenness and stress during the curling and storage process, it needs to be processed by leveling equipment. The leveling equipment is usually composed of multiple rollers. The steel strip passes between the rollers and is repeatedly rolled to eliminate unevenness and stress, making it flat, providing a stable foundation for subsequent processing and ensuring the forming quality.
3. Forming
The forming is carried out by means of a center bending deformation method or the like. Taking the center bending deformation method as an example, the bending starts from the middle of the strip and gradually expands to the edges on both sides. The bending radius is constant during the entire forming process. Through a series of forming stands, each stand is equipped with a roller of a specific shape, which applies pressure to the steel strip, causing it to gradually curl into a shape close to a round tube. This process requires precise control of the position and pressure of each stand roller to ensure the forming size accuracy and shape accuracy.
4. Welded
The edges of the formed steel strips need to be welded together to form a steel tube. Using resistance heat, high-frequency current is applied to the edge of the steel strip through electrodes, so that the edge is quickly heated to the welding temperature. Under the action of the squeezing roller, the edges of the steel strip are fused together to form a weld. During the welding process, parameters such as welding current, voltage, and welding speed have a significant impact on the quality of the weld and must be precisely controlled. For example, a suitable welding speed can avoid defects such as incomplete penetration or overburning in the weld.
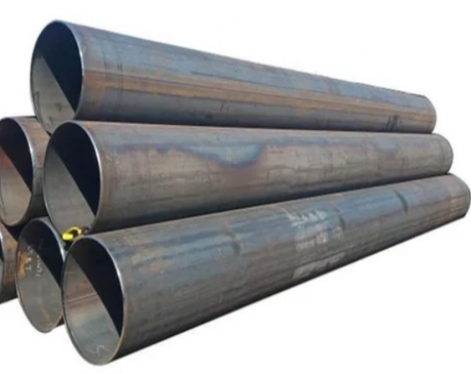
5. Deburring
After welding, burrs will form inside and outside the steel pipe, which need to be removed. Use special deburring equipment, such as internal and external bayonets, to cut the burrs inside and outside the pipe respectively. Burrs not only affect the surface quality of the steel pipe, but may also cause safety problems during use, such as blockage during fluid transportation. Therefore, deburring is an important part of ensuring the safety and life of the pipeline.
6. Sizing
After welding and deburring, the diameter of the steel pipe may have a certain deviation and needs to be sized. Through the sizing machine and specific molds, radial pressure is applied to the steel pipe to adjust the diameter to the standard size. The sizing process can ensure the dimensional accuracy of the product, meet the strict requirements of different projects on the size of steel pipes, and ensure the adaptability of steel pipes in various application scenarios.
7. Cutting
According to the actual use requirements, the sized steel pipe is cut into a specific length using cutting equipment. Common cutting equipment includes sawing machines, plasma cutting machines, etc. When cutting, the cutting speed and accuracy must be controlled to ensure that the cutting surface is flat, the length meets the requirements, reduce errors, and avoid material waste.
8. Flaw detection and inspection
Non-destructive testing technologies such as ultrasonic testing and magnetic flux leakage testing are used to detect whether there are cracks, pores, inclusions and other defects inside and on the surface of the steel pipe. According to relevant standards, the dimensional accuracy, chemical composition, mechanical properties, etc. of the steel pipe are fully inspected. Only products that meet the standards can enter the market to ensure the quality of carbon steel erw pipes.
Advantages of carbon steel erw pipe production process
1. It has a fast production speed and can achieve continuous and automated production. With a common welding speed of several meters per minute, it can efficiently produce a large number of steel pipes to meet the needs of large-scale engineering construction. For example, sufficient pipes can be quickly obtained for urban water supply network construction.
2. Low cost is also a major advantage. Hot-rolled coil is used as raw material, which is widely available and affordable. At the same time, the production process has low energy consumption and high efficiency, which reduces production costs. Compared with other welded steel pipe production processes, the cost per ton can be reduced by a certain percentage, which is very attractive in cost-sensitive industries such as construction.
3. The high quality of the weld is due to the high-frequency resistance welding technology. The heat is concentrated at the weld, the heat-affected zone is small, the weld structure is fine, and the strength and toughness are similar to those of the parent material. It can pass strict nondestructive testing and ensure the safe operation of the pipeline in high-pressure environments such as oil and natural gas transportation.
4. The dimensional accuracy is high. The production process is controlled by advanced equipment and precise molds. The pipe diameter tolerance can be controlled within a very small range. The ovality and wall thickness deviation can also be accurately controlled to meet various high-precision engineering requirements, such as occasions in mechanical manufacturing where high dimensional accuracy of parts is required.
Read more:Advantages and Disadvantages of Carbon Steel ERW Pipes
Carbon steel erw pipe production process steps
1. Raw material preparation
To produce carbon steel ERW pipes, we must first select suitable carbon steel strip as raw material. The material, thickness, width and other parameters of the steel strip must strictly comply with production standards. For example, common carbon steel materials such as Q195 and Q235 have clear range requirements for their carbon content, sulfur and phosphorus content and other chemical compositions. The quality of raw materials is directly related to the quality of finished products. High-quality steel strips can ensure that the steel pipe has good strength and toughness. For example, in oil pipelines, the steel pipe needs to be strong enough to withstand the internal oil pressure.
2. Uncoiling and leveling
The coiled carbon steel strip is slowly unrolled using an uncoiler. Since the steel strip will produce unevenness and stress during the curling and storage process, it needs to be processed by leveling equipment. The leveling equipment is usually composed of multiple rollers. The steel strip passes between the rollers and is repeatedly rolled to eliminate unevenness and stress, making it flat, providing a stable foundation for subsequent processing and ensuring the forming quality.
3. Forming
The forming is carried out by means of a center bending deformation method or the like. Taking the center bending deformation method as an example, the bending starts from the middle of the strip and gradually expands to the edges on both sides. The bending radius is constant during the entire forming process. Through a series of forming stands, each stand is equipped with a roller of a specific shape, which applies pressure to the steel strip, causing it to gradually curl into a shape close to a round tube. This process requires precise control of the position and pressure of each stand roller to ensure the forming size accuracy and shape accuracy.
4. Welded
The edges of the formed steel strips need to be welded together to form a steel tube. Using resistance heat, high-frequency current is applied to the edge of the steel strip through electrodes, so that the edge is quickly heated to the welding temperature. Under the action of the squeezing roller, the edges of the steel strip are fused together to form a weld. During the welding process, parameters such as welding current, voltage, and welding speed have a significant impact on the quality of the weld and must be precisely controlled. For example, a suitable welding speed can avoid defects such as incomplete penetration or overburning in the weld.
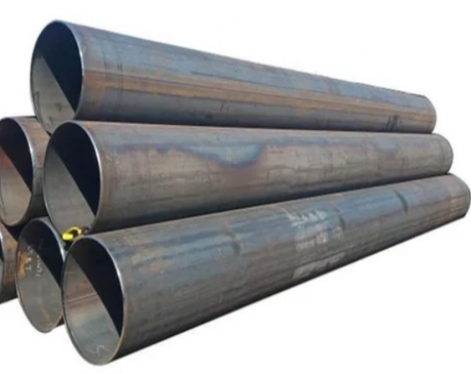
5. Deburring
After welding, burrs will form inside and outside the steel pipe, which need to be removed. Use special deburring equipment, such as internal and external bayonets, to cut the burrs inside and outside the pipe respectively. Burrs not only affect the surface quality of the steel pipe, but may also cause safety problems during use, such as blockage during fluid transportation. Therefore, deburring is an important part of ensuring the safety and life of the pipeline.
6. Sizing
After welding and deburring, the diameter of the steel pipe may have a certain deviation and needs to be sized. Through the sizing machine and specific molds, radial pressure is applied to the steel pipe to adjust the diameter to the standard size. The sizing process can ensure the dimensional accuracy of the product, meet the strict requirements of different projects on the size of steel pipes, and ensure the adaptability of steel pipes in various application scenarios.
7. Cutting
According to the actual use requirements, the sized steel pipe is cut into a specific length using cutting equipment. Common cutting equipment includes sawing machines, plasma cutting machines, etc. When cutting, the cutting speed and accuracy must be controlled to ensure that the cutting surface is flat, the length meets the requirements, reduce errors, and avoid material waste.
8. Flaw detection and inspection
Non-destructive testing technologies such as ultrasonic testing and magnetic flux leakage testing are used to detect whether there are cracks, pores, inclusions and other defects inside and on the surface of the steel pipe. According to relevant standards, the dimensional accuracy, chemical composition, mechanical properties, etc. of the steel pipe are fully inspected. Only products that meet the standards can enter the market to ensure the quality of carbon steel erw pipes.
Advantages of carbon steel erw pipe production process
1. It has a fast production speed and can achieve continuous and automated production. With a common welding speed of several meters per minute, it can efficiently produce a large number of steel pipes to meet the needs of large-scale engineering construction. For example, sufficient pipes can be quickly obtained for urban water supply network construction.
2. Low cost is also a major advantage. Hot-rolled coil is used as raw material, which is widely available and affordable. At the same time, the production process has low energy consumption and high efficiency, which reduces production costs. Compared with other welded steel pipe production processes, the cost per ton can be reduced by a certain percentage, which is very attractive in cost-sensitive industries such as construction.
3. The high quality of the weld is due to the high-frequency resistance welding technology. The heat is concentrated at the weld, the heat-affected zone is small, the weld structure is fine, and the strength and toughness are similar to those of the parent material. It can pass strict nondestructive testing and ensure the safe operation of the pipeline in high-pressure environments such as oil and natural gas transportation.
4. The dimensional accuracy is high. The production process is controlled by advanced equipment and precise molds. The pipe diameter tolerance can be controlled within a very small range. The ovality and wall thickness deviation can also be accurately controlled to meet various high-precision engineering requirements, such as occasions in mechanical manufacturing where high dimensional accuracy of parts is required.
Read more:Advantages and Disadvantages of Carbon Steel ERW Pipes