Casing spacers for pipe, also known as casing pipe spacers or simply casing spacers, are accessories used in piping systems primarily for supporting and securing pipes to ensure that the carrier pipe is correctly centered within the casing.
The role of casing seal spacers is as follows:
(1) To prevent leakage
Casing interfaces are the main areas where liquids and gases can leak. Using a sealing casing spacers can effectively prevent leakage and ensure the normal operation of the pipeline. This is especially important in harsh environments such as high temperatures, high pressures, and corrosive conditions.
(2)To relieve vibration
Casing seal spacers can alleviate noise and vibration caused by pipeline vibration, reducing the risk of pipeline sway and rupture, thereby extending the service life of the pipeline.
(3)To enhance connection strength
Sealing gaskets can also increase the connection strength of the pipeline interface, preventing the pipeline interface from being disconnected due to external forces, making the pipeline connection more secure.
In the petroleum industry, sealing with steel casing pipe gaskets is a common issue. The role of gasket sealing is to prevent fluid or gas leakage from interfaces such as pipelines, valves, or equipment. However, due to the special working environment of the petroleum industry, gasket sealing often faces challenges. Here are some common gasket sealing issues and solutions:
(1)Leakage
Leakage is one of the most common gasket sealing issues in the petroleum industry. Leakage can lead to serious safety and environmental problems, as well as production losses. The causes of leakage can be aging, wear, or inappropriateness of the gasket material, or improper installation of the gasket.
Solutions:
Use high-quality gasket materials
Choose materials that are resistant to high temperatures, corrosion, and pressure, such as metal gaskets, graphite gaskets, or PTFE gaskets.
Correctly install the spacer
Ensure the gasket fully covers the interface and avoid any defects or uneven surfaces.
Regularly inspect and replace gaskets
Regularly check the condition of the gasket and replace it immediately if wear or aging is found.
(2) Seepage
In addition to obvious leaks, gasket sealing issues also include minor seepage. Seepage may not be easily noticeable but can gradually accumulate and cause problems. The causes of seepage can be insufficient contact between the gasket and the interface, or the roughness of the gasket surface .
Solutions:
Use high-compression gaskets
High-compression gaskets have good elasticity and plasticity, which can provide a larger contact area on the interface, thus reducing the possibility of seepage.
Gasket material selection and smoothness
Choose gasket materials with better surface smoothness, such as rubber or flexible graphite, and ensure the interface surface is smooth.
(3)High temperature and high pressure environments
The working environment in the petroleum industry usually involves high temperatures and high pressures, which pose higher requirements for gasket sealing. Conventional gasket materials may not be able to withstand extreme conditions, leading to leakage or seepage.
Solutions:
Use high-temperature and high-pressure resistant gasket materials
Choose gasket materials specifically designed to withstand high temperatures and pressures, such as metal gaskets or high-temperature rubber gaskets.
Use reinforced gaskets
Some gaskets have enhanced properties, such as metal gaskets with serrated surfaces or combinations of gaskets with metal layers, which can provide better sealing performance in high-temperature and high-pressure environments.
1.What is the purpose of casing spacers?
The role of casing seal spacers is as follows:(1) To prevent leakage
Casing interfaces are the main areas where liquids and gases can leak. Using a sealing casing spacers can effectively prevent leakage and ensure the normal operation of the pipeline. This is especially important in harsh environments such as high temperatures, high pressures, and corrosive conditions.
(2)To relieve vibration
Casing seal spacers can alleviate noise and vibration caused by pipeline vibration, reducing the risk of pipeline sway and rupture, thereby extending the service life of the pipeline.
(3)To enhance connection strength
Sealing gaskets can also increase the connection strength of the pipeline interface, preventing the pipeline interface from being disconnected due to external forces, making the pipeline connection more secure.
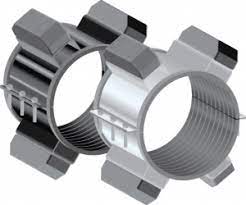
2. Common sealing issues of steel casing pipe spacers
In the petroleum industry, sealing with steel casing pipe gaskets is a common issue. The role of gasket sealing is to prevent fluid or gas leakage from interfaces such as pipelines, valves, or equipment. However, due to the special working environment of the petroleum industry, gasket sealing often faces challenges. Here are some common gasket sealing issues and solutions:(1)Leakage
Leakage is one of the most common gasket sealing issues in the petroleum industry. Leakage can lead to serious safety and environmental problems, as well as production losses. The causes of leakage can be aging, wear, or inappropriateness of the gasket material, or improper installation of the gasket.
Solutions:
Use high-quality gasket materials
Choose materials that are resistant to high temperatures, corrosion, and pressure, such as metal gaskets, graphite gaskets, or PTFE gaskets.
Correctly install the spacer
Ensure the gasket fully covers the interface and avoid any defects or uneven surfaces.
Regularly inspect and replace gaskets
Regularly check the condition of the gasket and replace it immediately if wear or aging is found.
(2) Seepage
In addition to obvious leaks, gasket sealing issues also include minor seepage. Seepage may not be easily noticeable but can gradually accumulate and cause problems. The causes of seepage can be insufficient contact between the gasket and the interface, or the roughness of the gasket surface .
Solutions:
Use high-compression gaskets
High-compression gaskets have good elasticity and plasticity, which can provide a larger contact area on the interface, thus reducing the possibility of seepage.
Gasket material selection and smoothness
Choose gasket materials with better surface smoothness, such as rubber or flexible graphite, and ensure the interface surface is smooth.
(3)High temperature and high pressure environments
The working environment in the petroleum industry usually involves high temperatures and high pressures, which pose higher requirements for gasket sealing. Conventional gasket materials may not be able to withstand extreme conditions, leading to leakage or seepage.
Solutions:
Use high-temperature and high-pressure resistant gasket materials
Choose gasket materials specifically designed to withstand high temperatures and pressures, such as metal gaskets or high-temperature rubber gaskets.
Use reinforced gaskets
Some gaskets have enhanced properties, such as metal gaskets with serrated surfaces or combinations of gaskets with metal layers, which can provide better sealing performance in high-temperature and high-pressure environments.
Previous:High Frequency Welded H Beam