Drill pipe breakage is a common problem in drilling operations, which causes serious consequences, so it needs to be taken seriously by all staff. The main reasons for drill pipe breakage include:
1. Insufficient fracture strength
Insufficient fracture strength of drill pipe is one of the main reasons for drill pipe breakage. This may be caused by poor material quality, incorrect manufacturing process or unreasonable design.
2. Fatigue fracture
Drilling operations need to withstand greater pressure and friction. During repeated loading and unloading, surface cracks and internal fatigue damage are prone to occur, eventually leading to fracture.
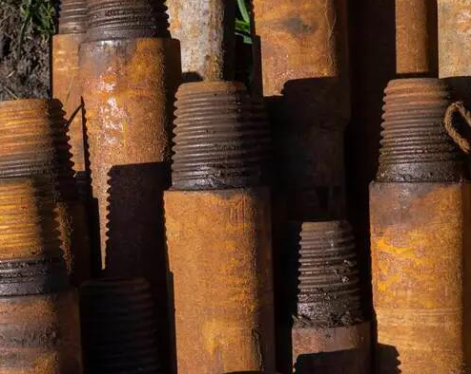
3. Excessive internal pressure
Environmental factors such as pressure and temperature in the borehole will produce internal stress on the drill pipe. If this pressure is too high, it will cause the drill pipe to deform and break.
4. Failure of drill pipe connection
Failure of drill pipe connection may cause deformation of the entire drilling tool system, thereby aggravating stress concentration and causing drill pipe breakage.
5. Improper operation
If the operator improperly uses and maintains the drilling tool, or uses inappropriate operating methods during construction, it may cause the drill pipe to break.
How to prevent drill pipe breakage?
1. High-quality materials: Select high-quality drill pipe materials to ensure that the quality meets the requirements.
2. Correct process: Ensure that the manufacturing process meets the standards and follows the correct design requirements.
3. Reasonable design of well depth: According to the actual conditions of drilling geological conditions and working environment, reasonably determine the well depth, drill pipe size and material to reduce the force and wear of the drill pipe. According to the well depth, geological conditions and working environment, select suitable drill pipe specifications and materials, such as suitable oil pipes.
4. Maintenance: Strengthen the maintenance of drill pipes, regularly check whether the drill pipes, connections, etc. have abnormal conditions such as wear and deformation, and whether they need to be replaced and repaired.
5. Proper operation: Strengthen the use of drill pipe training, and operators must follow the correct use and maintenance methods to avoid unnecessary damage and danger.
In short, the breakage of drill pipes has a serious impact on oil drilling work. In order to reduce the risk of drill pipe breakage, it is necessary to analyze and solve it from multiple aspects. It is of great significance to strengthen the management of various links such as materials, processes, maintenance and proper operation, reduce the risk of drill bit breakage, and improve the efficiency and safety of drilling work.
1. Insufficient fracture strength
Insufficient fracture strength of drill pipe is one of the main reasons for drill pipe breakage. This may be caused by poor material quality, incorrect manufacturing process or unreasonable design.
2. Fatigue fracture
Drilling operations need to withstand greater pressure and friction. During repeated loading and unloading, surface cracks and internal fatigue damage are prone to occur, eventually leading to fracture.
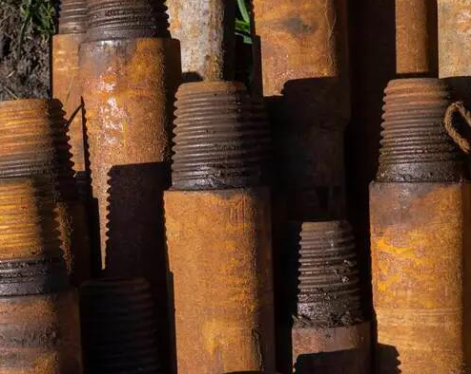
3. Excessive internal pressure
Environmental factors such as pressure and temperature in the borehole will produce internal stress on the drill pipe. If this pressure is too high, it will cause the drill pipe to deform and break.
4. Failure of drill pipe connection
Failure of drill pipe connection may cause deformation of the entire drilling tool system, thereby aggravating stress concentration and causing drill pipe breakage.
5. Improper operation
If the operator improperly uses and maintains the drilling tool, or uses inappropriate operating methods during construction, it may cause the drill pipe to break.
How to prevent drill pipe breakage?
1. High-quality materials: Select high-quality drill pipe materials to ensure that the quality meets the requirements.
2. Correct process: Ensure that the manufacturing process meets the standards and follows the correct design requirements.
3. Reasonable design of well depth: According to the actual conditions of drilling geological conditions and working environment, reasonably determine the well depth, drill pipe size and material to reduce the force and wear of the drill pipe. According to the well depth, geological conditions and working environment, select suitable drill pipe specifications and materials, such as suitable oil pipes.
4. Maintenance: Strengthen the maintenance of drill pipes, regularly check whether the drill pipes, connections, etc. have abnormal conditions such as wear and deformation, and whether they need to be replaced and repaired.
5. Proper operation: Strengthen the use of drill pipe training, and operators must follow the correct use and maintenance methods to avoid unnecessary damage and danger.
In short, the breakage of drill pipes has a serious impact on oil drilling work. In order to reduce the risk of drill pipe breakage, it is necessary to analyze and solve it from multiple aspects. It is of great significance to strengthen the management of various links such as materials, processes, maintenance and proper operation, reduce the risk of drill bit breakage, and improve the efficiency and safety of drilling work.