In the production of seamless steel pipes, the function of the perforation process is to pierce the solid tube blank into a hollow capillary tube. Perforation is the first process of metal deformation. The pierced tube has thicker wall, shorter length, and poor internal and external surface quality, so it is called capillary tube. If there are some defects in the capillary tube, it will be difficult to eliminate or reduce them through subsequent processes. Therefore, the perforation process plays an important role in the production of seamless pipes.
According to the structure of the piercing machine and the deformation characteristics of the piercing process, the piercing machine can be divided into two major categories: one is the cross-rolling piercing machine, and various types have evolved according to the different roller shapes and guide devices.
Such as Mannesmann punching machine, Diesel punching machine, etc.; the other type is pressure punching machine.
The main types of cross-rolling piercing machines are: barrel roller piercing machine, Diesel piercing machine, tapered roller piercing machine and three-roller piercing machine.
1.1.1 Barrel roller punching machine
The two-roller cross-rolling piercing machine has two left and right rollers rotating in the same direction, two guide plates arranged vertically up and down are fixed, and a follower head in the middle. The axis of the roller and the rolling line intersect to form an inclination angle. The rollers are arranged left and right, and the guide plates are arranged up and down for horizontal piercers, while the opposite is vertical piercers. The advantages of the two-roller cross-rolling piercing machine are good centering and uniform wall thickness of the capillary tube; a large primary elongation coefficient, generally between 1.25 and 4.5, and it can be directly pierced from a solid round blank into a thinner capillary tube.
The main disadvantage is that this processing method causes complex deformation and is easy to produce and expand defects on the inner and outer surfaces of the capillary tube, so the quality requirements for the tube blank are relatively high. Due to the continuous improvement of the requirements for the surface quality of steel pipes, the continuous growth of the proportion of alloy steel, especially the promotion and use of continuous cast round billets, the current two-roll cross-rolling machine with a feed angle of less than 13° can no longer meet the needs of seamless steel pipe production. Due to the requirements on productivity and steel pipe quality, new structures of cross-rolling piercing machines have appeared one after another.
1.1.2 Diesel punch
Diesel piercing machine is an active rotating guide plate two-roller (barrel roller) cross-rolling piercing machine, which is evolved from the two-roller barrel roller piercing machine. The rollers are arranged up and down, and each roller is directly driven by a separate main motor through a universal connecting shaft; the guide plates on the left and right sides are replaced by two active rotating guide plates. Because the guide plate is driven by the main drive, the tangential speed of the guide plate rotation in the compression zone is 20% to 25% greater than the tangential speed of the roll on the rolling axis, exerting an axial feed force on the rolled piece to reduce The axial resistance of the rolled piece. The pore throat ovality can be adjusted to 1.0, so that the maximum elongation coefficient reaches 5.0, the axial metal sliding coefficient increases, and the quality of the internal and external surfaces of the capillary tube is greatly improved, thereby increasing productivity and reducing unit consumption. The exit speed of Diesel punching machine reaches 1.2m/s. The guide plate has little wear and long service life. It does not need to be replaced frequently, which is beneficial to improving the operation rate.
1.1.3 Tapered roller punching machine
In the 1980s, based on the structural characteristics of the Diesel piercing machine, a two-roller cross-rolling piercing machine with a tapered roller and a large feed angle appeared. The biggest difference between it and the Diesel piercing machine is that the roller shape is changed from barrel to tapered. This roller shape is better than the barrel roller in terms of adaptability to the cross-rolling piercing machine. Because on this kind of piercing machine, the diameter of the tapered roller gradually increases along the piercing deformation zone. Therefore, the tangential shear stress during the deformation process of the tube blank is reduced to a large extent, the rotational transverse forging effect is suppressed, and the capillary tube is improved. The internal and external surface quality allows many difficult-to-wear high-alloy steel pipe blanks to be rolled smoothly on this rolling mill. The tapered roller piercing machine has high piercing efficiency. It is reported that the maximum exit speed can reach 1.5m/s, which is conducive to the selection of high-productivity units; in addition to the feed angle of about 10° between the roll axis and the rolling line, there is also a The rolling angle is about 15°, which can make the axial sliding coefficient of this type of perforation reach 0.9, and the maximum elongation coefficient can reach 6.0. In terms of the distribution of deformation, it can bear larger deformation, thereby reducing the deformation of the pipe rolling machine. ; The diameter expansion of the perforation reaches 30%~40%, which not only provides thin-walled capillary tubes, but also reduces the range of tube blank specifications and simplifies production management. Tapered roller piercing machines are equipped with both guide plates and guide plates. Both configurations are used in new pipe rolling units that have been built or are under construction.
Diesel punches and cone punches are new types of punches widely used in contemporary times. They have high punching efficiency and high product accuracy, and are suitable for punching continuous casting billets. Among them, the tapered roller piercing machine has greater application prospects.
Pressure piercing of tube blanks is often performed on a vertical hydraulic press or hydraulic press. It places a square or polygonal steel ingot in an extrusion cylinder and extrudes it into a hollow cup. The elongation coefficient is 1.0~1.1, and the piercing ratio is not greater than
7~10. Compared with two-roll cross rolling, the center of the blank in this processing method is in an unequal omnidirectional compressive stress state, and the outer surface is subject to greater radial pressure. Because defects will not occur on the inner and outer surfaces during the processing, it is The material has no strict requirements and can be used for perforating steel ingots, continuous cast billets and low plasticity materials. This method of processing mainly involves central deformation, which is especially beneficial to the densification of the coarse and loose structures in the center of the steel ingot. Although the maximum elongation coefficient is only 1.1, the deformation effect of the central part is equivalent to 5 times the external processing effect. The main disadvantages are low productivity, low yield, and large eccentricity.
Use punches and molds to extrude solid square ingots into ring-shaped capillary tubes. The metal is in a state of full compressive stress and can be used to make steel ingots with poor plasticity, such as continuous casting billets and low-plasticity alloy steels; the internal and external surfaces are of good quality; the ingot (billet) The central deformation is severe, which is beneficial to improving the metal structure; the elongation coefficient of the square-section blank that can be punched is small; the perforation ratio is small. However, its disadvantage is that the capillary wall thickness is seriously uneven; the productivity is low and it is not suitable for mass production.
The longitudinal roller with a round hole replaces the die barrel, the top replaces the punch, and the feeding mechanism is used to apply axial force to the blank. The elongation coefficient is larger than that of pressure punching, μ=1.1~1.2; the punching ratio is large, l/d reaches 40; the productivity is high;
The consumption of tools and molds is low; square-section low-plastic blanks can be worn. But the disadvantage is that the elongation coefficient is smaller than cross rolling, and the capillary wall thickness is seriously uneven.
In short, through comparative analysis of the above methods, it can be found that: Mannesmann method, Diesel perforation method, Stiefel method and other methods are relatively backward and have been used less; while Transvaal perforation method,
Methods such as the extrusion piercing method are limited in wide-scale use due to limitations; thus, the cone roller piercing method, the three-roller cross-rolling piercing method, the longitudinal rolling piercing method, etc. will be popularized and applied through their own advantages.
Based on the above classification and comparison, it is not difficult to see that: the two-roller cross-rolling piercing machine with double supports, active large guide plate, large feed angle, small entrance roller surface taper angle, cone roller type (bacteria type), and rolling angle is the most suitable ideal structure
form.
1. Classification of seamless pipe perforation methods
According to the structure of the piercing machine and the deformation characteristics of the piercing process, the piercing machine can be divided into two major categories: one is the cross-rolling piercing machine, and various types have evolved according to the different roller shapes and guide devices.Such as Mannesmann punching machine, Diesel punching machine, etc.; the other type is pressure punching machine.
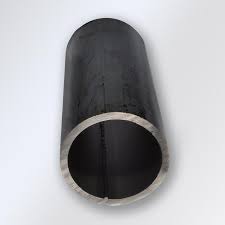
1.1 Cross-rolling punching machine
The main types of cross-rolling piercing machines are: barrel roller piercing machine, Diesel piercing machine, tapered roller piercing machine and three-roller piercing machine.1.1.1 Barrel roller punching machine
The two-roller cross-rolling piercing machine has two left and right rollers rotating in the same direction, two guide plates arranged vertically up and down are fixed, and a follower head in the middle. The axis of the roller and the rolling line intersect to form an inclination angle. The rollers are arranged left and right, and the guide plates are arranged up and down for horizontal piercers, while the opposite is vertical piercers. The advantages of the two-roller cross-rolling piercing machine are good centering and uniform wall thickness of the capillary tube; a large primary elongation coefficient, generally between 1.25 and 4.5, and it can be directly pierced from a solid round blank into a thinner capillary tube.
The main disadvantage is that this processing method causes complex deformation and is easy to produce and expand defects on the inner and outer surfaces of the capillary tube, so the quality requirements for the tube blank are relatively high. Due to the continuous improvement of the requirements for the surface quality of steel pipes, the continuous growth of the proportion of alloy steel, especially the promotion and use of continuous cast round billets, the current two-roll cross-rolling machine with a feed angle of less than 13° can no longer meet the needs of seamless steel pipe production. Due to the requirements on productivity and steel pipe quality, new structures of cross-rolling piercing machines have appeared one after another.
1.1.2 Diesel punch
Diesel piercing machine is an active rotating guide plate two-roller (barrel roller) cross-rolling piercing machine, which is evolved from the two-roller barrel roller piercing machine. The rollers are arranged up and down, and each roller is directly driven by a separate main motor through a universal connecting shaft; the guide plates on the left and right sides are replaced by two active rotating guide plates. Because the guide plate is driven by the main drive, the tangential speed of the guide plate rotation in the compression zone is 20% to 25% greater than the tangential speed of the roll on the rolling axis, exerting an axial feed force on the rolled piece to reduce The axial resistance of the rolled piece. The pore throat ovality can be adjusted to 1.0, so that the maximum elongation coefficient reaches 5.0, the axial metal sliding coefficient increases, and the quality of the internal and external surfaces of the capillary tube is greatly improved, thereby increasing productivity and reducing unit consumption. The exit speed of Diesel punching machine reaches 1.2m/s. The guide plate has little wear and long service life. It does not need to be replaced frequently, which is beneficial to improving the operation rate.
1.1.3 Tapered roller punching machine
In the 1980s, based on the structural characteristics of the Diesel piercing machine, a two-roller cross-rolling piercing machine with a tapered roller and a large feed angle appeared. The biggest difference between it and the Diesel piercing machine is that the roller shape is changed from barrel to tapered. This roller shape is better than the barrel roller in terms of adaptability to the cross-rolling piercing machine. Because on this kind of piercing machine, the diameter of the tapered roller gradually increases along the piercing deformation zone. Therefore, the tangential shear stress during the deformation process of the tube blank is reduced to a large extent, the rotational transverse forging effect is suppressed, and the capillary tube is improved. The internal and external surface quality allows many difficult-to-wear high-alloy steel pipe blanks to be rolled smoothly on this rolling mill. The tapered roller piercing machine has high piercing efficiency. It is reported that the maximum exit speed can reach 1.5m/s, which is conducive to the selection of high-productivity units; in addition to the feed angle of about 10° between the roll axis and the rolling line, there is also a The rolling angle is about 15°, which can make the axial sliding coefficient of this type of perforation reach 0.9, and the maximum elongation coefficient can reach 6.0. In terms of the distribution of deformation, it can bear larger deformation, thereby reducing the deformation of the pipe rolling machine. ; The diameter expansion of the perforation reaches 30%~40%, which not only provides thin-walled capillary tubes, but also reduces the range of tube blank specifications and simplifies production management. Tapered roller piercing machines are equipped with both guide plates and guide plates. Both configurations are used in new pipe rolling units that have been built or are under construction.
Diesel punches and cone punches are new types of punches widely used in contemporary times. They have high punching efficiency and high product accuracy, and are suitable for punching continuous casting billets. Among them, the tapered roller piercing machine has greater application prospects.
1.2 Pressure perforation
Pressure piercing of tube blanks is often performed on a vertical hydraulic press or hydraulic press. It places a square or polygonal steel ingot in an extrusion cylinder and extrudes it into a hollow cup. The elongation coefficient is 1.0~1.1, and the piercing ratio is not greater than7~10. Compared with two-roll cross rolling, the center of the blank in this processing method is in an unequal omnidirectional compressive stress state, and the outer surface is subject to greater radial pressure. Because defects will not occur on the inner and outer surfaces during the processing, it is The material has no strict requirements and can be used for perforating steel ingots, continuous cast billets and low plasticity materials. This method of processing mainly involves central deformation, which is especially beneficial to the densification of the coarse and loose structures in the center of the steel ingot. Although the maximum elongation coefficient is only 1.1, the deformation effect of the central part is equivalent to 5 times the external processing effect. The main disadvantages are low productivity, low yield, and large eccentricity.
2. Comparison of perforation methods
2.1 Cross-rolled piercing
The analysis and comparison of the advantages and disadvantages of the cross-rolled piercing method are shown in Table 1.Piercing Method | Characteristics | Advantages | Disadvantages |
---|---|---|---|
Mannesmann Method | Two-roll slant rolling + guide plate | Good concentricity and uniform wall thickness | Complex deformation, prone to surface defects |
Diestel Piercing Method | Two-roll slant rolling + active guide disc | High friction coefficient, high sliding coefficient, high surface quality | Poor hole type sealing, unstable rolling, not flexible in changing specifications |
Fungal-shaped Piercing Method | Fungal-shaped rolling shape | Simple structure | Poor rigidity and strength of the mill; fixed roll angle, narrow specification range |
Disc Piercing Method | Disc-shaped roll shape | Simple structure | Poor rigidity and strength of the mill; fixed roll angle, narrow specification range |
Conical Roll Piercing | Two-roll slant rolling, with a conical roll shape | Good bite-in conditions, high quality of rough tubes, high piercing efficiency | Inconvenient to change specifications |
Three-roll Oblique Piercing Method | Three rolls rotating around the rolling line | Significant three-directional compressive stress on metal, improved plasticity; improved surface quality of rolled pieces; fast piercing speed; high-quality rough tubes | Cannot pierce thin-walled tubes |
Transvaal Piercing Method | Rotating frame | Significant three-directional compressive stress on metal, improved plasticity; improved surface quality of rolled pieces; stable tube size, high precision; convenient to change specifications; can pierce wall tubes | Easily forms ring-shaped cavities during piercing |
Table 1
2.2 Punching and perforation method
Use punches and molds to extrude solid square ingots into ring-shaped capillary tubes. The metal is in a state of full compressive stress and can be used to make steel ingots with poor plasticity, such as continuous casting billets and low-plasticity alloy steels; the internal and external surfaces are of good quality; the ingot (billet) The central deformation is severe, which is beneficial to improving the metal structure; the elongation coefficient of the square-section blank that can be punched is small; the perforation ratio is small. However, its disadvantage is that the capillary wall thickness is seriously uneven; the productivity is low and it is not suitable for mass production.
2.3 Longitudinal rolling and piercing method (push rolling and piercing method-PPM method)
The longitudinal roller with a round hole replaces the die barrel, the top replaces the punch, and the feeding mechanism is used to apply axial force to the blank. The elongation coefficient is larger than that of pressure punching, μ=1.1~1.2; the punching ratio is large, l/d reaches 40; the productivity is high;The consumption of tools and molds is low; square-section low-plastic blanks can be worn. But the disadvantage is that the elongation coefficient is smaller than cross rolling, and the capillary wall thickness is seriously uneven.
In short, through comparative analysis of the above methods, it can be found that: Mannesmann method, Diesel perforation method, Stiefel method and other methods are relatively backward and have been used less; while Transvaal perforation method,
Methods such as the extrusion piercing method are limited in wide-scale use due to limitations; thus, the cone roller piercing method, the three-roller cross-rolling piercing method, the longitudinal rolling piercing method, etc. will be popularized and applied through their own advantages.
3.Conclusion
Based on the above classification and comparison, it is not difficult to see that: the two-roller cross-rolling piercing machine with double supports, active large guide plate, large feed angle, small entrance roller surface taper angle, cone roller type (bacteria type), and rolling angle is the most suitable ideal structureform.