The production process of hot-rolled seamless steel pipes involves multiple links, and quality problems may occur in each link. Nansteel Manufacturing Co., Ltd carefully summarizes the common quality problems in the production process of hot-rolled seamless steel pipes:
1. Tube Billet Tube defects:
Cracks: Cracks on the surface or inside the tube billet may be caused by the solidification or rolling process of the ingot or continuous casting billet.
Inclusions: Non-metallic inclusions such as oxides and sulfides inside or on the surface of the tube billet will reduce the mechanical properties of the steel pipe.
Porosity: Porosity inside the tube billet affects the density and strength of the steel pipe.
Segregation: The chemical composition inside the tube billet is uneven, resulting in inconsistent performance of the steel pipe.
Pipe billet size deviation: The diameter, length and other dimensions of the tube billet exceed the allowable deviation range, affecting subsequent piercing and rolling.
Overheating or overburning: Excessive heating temperature leads to coarse grains, reduces the mechanical properties of the steel tube, and even produces cracks. Overburning refers to severe oxidation of the steel surface, forming oxide scale, which affects the surface quality of the steel tube.
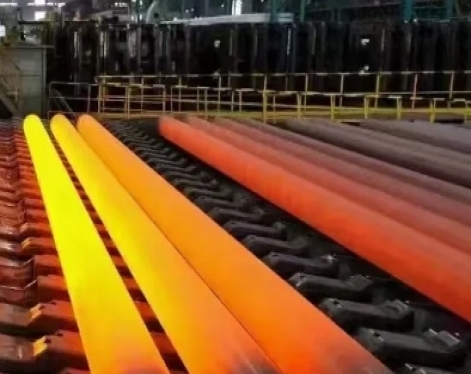
3. Perforation
Uneven wall thickness
During the perforation process, the wall thickness of the rough tube is uneven due to reasons such as incorrect head position and improper roller adjustment.
Internal and external surface defects
Spiral channel: Spiral defects on the internal and external surfaces of the rough tube, affecting the surface quality and mechanical properties of the steel tube.
Ear: A protrusion formed on the end or surface of the rough tube, affecting subsequent rolling.
Inner fold: A fold formed on the inner surface of the rough tube, affecting the internal quality of the steel tube.
Center hole deviation
During the perforation process, due to the deflection of the head or roller, the center hole of the rough pipe is offset, affecting the wall thickness uniformity and straightness of the steel pipe.
4. Rolling
Uneven wall thickness
During the rolling process, the wall thickness of the steel pipe is uneven due to roller wear, improper adjustment and other reasons.
Outer diameter tolerance:
During the rolling process, due to improper adjustment or wear of the rollers, the outer diameter of the steel pipe exceeds the allowable deviation range.
Surface defects
Scratches: The surface of the steel pipe is scratched, affecting the surface quality.
Rolling overlap: Overlapping defects formed on the surface of the steel pipe affect the surface quality and mechanical properties.
Straightness exceeds tolerance
The steel pipe is bent and deformed after rolling, and the straightness exceeds the allowable deviation range.
5. Cooling and straightening
Uneven cooling: Uneven cooling speed causes residual stress inside the steel pipe, affecting the mechanical properties of the steel pipe.
Over-straightening or under-straightening: Over-straightening will cause new defects in the steel pipe, while under-straightening will not eliminate the bending deformation of the steel pipe.
6. Inspection
Missed inspection: Due to improper inspection methods or operations, the defects of the steel pipes are not discovered in time.
Misjudgment: Qualified steel pipes are misjudged as unqualified, or unqualified steel pipes are misjudged as qualified.
In view of the above quality problems, hot rolled seamless steel pipes need to take corresponding control measures
Strictly control the quality of raw materials: select qualified tube billets and conduct necessary inspections.
Optimize the heating process: ensure that the tube billets are heated evenly to avoid overheating or overburning.
Reasonably adjust the perforation and rolling parameters: ensure the smooth perforation and rolling, and control the wall thickness and outer diameter accuracy of the steel pipe.
Strengthen equipment maintenance and care: regularly check and maintain equipment, and replace worn parts in time.
Improve inspection methods: use advanced inspection equipment and methods to improve the accuracy and reliability of inspection.
Strengthen quality management: establish a complete quality management system and strengthen the monitoring and management of the production process.
Through the above analysis, we can understand the various quality problems that may occur in the production process of hot-rolled seamless steel pipes, and take corresponding control measures to improve product quality.
Read more: Surface oxidation treatment of hot-rolled seamless pipe
1. Tube Billet Tube defects:
Cracks: Cracks on the surface or inside the tube billet may be caused by the solidification or rolling process of the ingot or continuous casting billet.
Inclusions: Non-metallic inclusions such as oxides and sulfides inside or on the surface of the tube billet will reduce the mechanical properties of the steel pipe.
Porosity: Porosity inside the tube billet affects the density and strength of the steel pipe.
Segregation: The chemical composition inside the tube billet is uneven, resulting in inconsistent performance of the steel pipe.
Pipe billet size deviation: The diameter, length and other dimensions of the tube billet exceed the allowable deviation range, affecting subsequent piercing and rolling.
2. Heating
Uneven heating: The temperature inside and outside the tube is uneven, resulting in uneven deformation during perforation, affecting the uniformity of the wall thickness of the steel tube.Overheating or overburning: Excessive heating temperature leads to coarse grains, reduces the mechanical properties of the steel tube, and even produces cracks. Overburning refers to severe oxidation of the steel surface, forming oxide scale, which affects the surface quality of the steel tube.
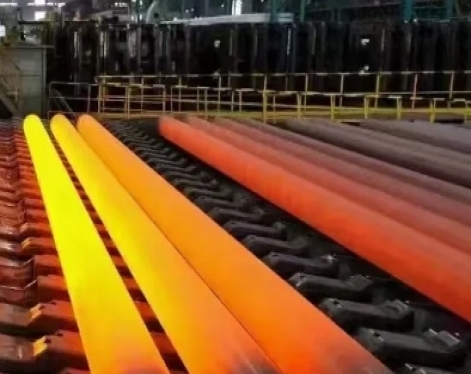
3. Perforation
Uneven wall thickness
During the perforation process, the wall thickness of the rough tube is uneven due to reasons such as incorrect head position and improper roller adjustment.
Internal and external surface defects
Spiral channel: Spiral defects on the internal and external surfaces of the rough tube, affecting the surface quality and mechanical properties of the steel tube.
Ear: A protrusion formed on the end or surface of the rough tube, affecting subsequent rolling.
Inner fold: A fold formed on the inner surface of the rough tube, affecting the internal quality of the steel tube.
Center hole deviation
During the perforation process, due to the deflection of the head or roller, the center hole of the rough pipe is offset, affecting the wall thickness uniformity and straightness of the steel pipe.
4. Rolling
Uneven wall thickness
During the rolling process, the wall thickness of the steel pipe is uneven due to roller wear, improper adjustment and other reasons.
Outer diameter tolerance:
During the rolling process, due to improper adjustment or wear of the rollers, the outer diameter of the steel pipe exceeds the allowable deviation range.
Surface defects
Scratches: The surface of the steel pipe is scratched, affecting the surface quality.
Rolling overlap: Overlapping defects formed on the surface of the steel pipe affect the surface quality and mechanical properties.
Straightness exceeds tolerance
The steel pipe is bent and deformed after rolling, and the straightness exceeds the allowable deviation range.
5. Cooling and straightening
Uneven cooling: Uneven cooling speed causes residual stress inside the steel pipe, affecting the mechanical properties of the steel pipe.
Over-straightening or under-straightening: Over-straightening will cause new defects in the steel pipe, while under-straightening will not eliminate the bending deformation of the steel pipe.
6. Inspection
Missed inspection: Due to improper inspection methods or operations, the defects of the steel pipes are not discovered in time.
Misjudgment: Qualified steel pipes are misjudged as unqualified, or unqualified steel pipes are misjudged as qualified.
In view of the above quality problems, hot rolled seamless steel pipes need to take corresponding control measures
Strictly control the quality of raw materials: select qualified tube billets and conduct necessary inspections.
Optimize the heating process: ensure that the tube billets are heated evenly to avoid overheating or overburning.
Reasonably adjust the perforation and rolling parameters: ensure the smooth perforation and rolling, and control the wall thickness and outer diameter accuracy of the steel pipe.
Strengthen equipment maintenance and care: regularly check and maintain equipment, and replace worn parts in time.
Improve inspection methods: use advanced inspection equipment and methods to improve the accuracy and reliability of inspection.
Strengthen quality management: establish a complete quality management system and strengthen the monitoring and management of the production process.
Through the above analysis, we can understand the various quality problems that may occur in the production process of hot-rolled seamless steel pipes, and take corresponding control measures to improve product quality.
Read more: Surface oxidation treatment of hot-rolled seamless pipe