Mechanical tubes can be called the "vascular system" of industrial equipment. They are core components for transporting fluids and gases and are widely used in many fields such as petroleum, chemical industry, and machinery manufacturing. In the oil field, mechanical tubes are responsible for the transportation of crude oil and natural gas; in the chemical industry, they carry the transmission of various corrosive chemicals; in mechanical manufacturing, mechanical tubes are also indispensable to assist in the power transmission and medium supply of equipment.
Four core steps of mechanical tube maintenance
1. Daily cleaning: preventing hidden dangers from the source
Surface cleaning: During daily operation, the surface of the mechanical tube is prone to absorb dust, oil and other impurities. You can use a neutral detergent and a soft cloth to wipe it to remove surface dirt;
Internal unblocking: Critical pipelines such as hydraulic pipes are easily blocked by impurities in the medium.
Environmental control: Create a good "living environment" for mechanical pipes to avoid close contact with corrosive substances such as acids and alkalis.
2. Regular lubrication: reduce friction loss
Lubricant selection: According to the type of pipeline, choose lubricants such as engine oil and gear oil reasonably, focus on the lubrication of moving parts and connection points, reduce friction between parts, and make the mechanical pipe run more smoothly.
Seal maintenance: carefully check whether the seal is aging and replace the problematic seal in time.
Dynamic monitoring: After lubrication, closely observe the operation status of the pipeline and pay attention to whether there is any abnormal vibration or noise.
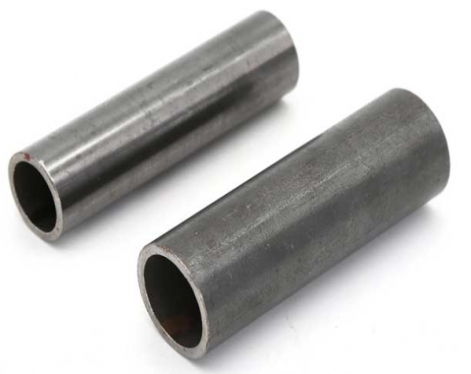
3. Key inspection: Prevent problems before they happen
Appearance inspection: Regularly conduct "physical inspections" on mechanical pipes, focusing on welds and elbows to check for cracks, deformation or leakage.
Pressure test: For high-pressure pipes, water pressure or air pressure tests should be performed regularly to ensure that their pressure-bearing capacity meets the standards.
Sealing test: Apply soapy water to the interface and observe carefully whether there are bubbles to determine whether there is a leak.
4. Scientific operation: avoid maintenance misunderstandings
Avoid excessive maintenance: When a mechanical tube has a minor fault, repair it first rather than blindly replacing parts.
Avoid ignoring the fit clearance: For precision parts such as plunger pumps, assemble them strictly according to the standards to ensure that the fit clearance meets the requirements.
Avoid not checking the travel allowance: Regularly check the travel allowance of moving parts to avoid insufficient travel due to excessive wear, which may cause equipment failure.
Practical tips to extend the life of mechanical tubes
1. Moisture-proof and anti-corrosion: Moisture and corrosive substances are the enemies of mechanical pipes and will accelerate the corrosion of pipes. Before the rainy season comes, apply a layer of anti-rust paint to the mechanical pipes to effectively isolate moisture and air and slow down the rust rate; During storage, raise the bottom of the mechanical pipe by more than 10 cm to avoid direct contact with the ground and reduce the risk of moisture.
2. Prevent vibration damage: Vibration can loosen the internal structure of the mechanical tube and reduce its strength.
3. Repair defects promptly: Once the zinc layer on the surface of the mechanical tube is found to be falling off or local oxidation occurs, it should be immediately treated with special repair paint. Repairing these minor problems promptly can prevent them from further deteriorating and extend the service life of the mechanical tube.
Conclusion
The maintenance of mechanical pipes needs to be combined with cleaning, lubrication, inspection and scientific operation. Preventive maintenance can extend the service life and reduce the risk of sudden failures. The selection of professional tools and standardized processes is the core to ensure the efficient and stable operation of equipment. Cleaning in place to avoid hidden dangers, lubrication in time to reduce wear, regular inspections to detect early, and scientific operations to ensure safety.
Read more: Advantages and Disadvantages of Mechanical Tubes
Four core steps of mechanical tube maintenance
1. Daily cleaning: preventing hidden dangers from the source
Surface cleaning: During daily operation, the surface of the mechanical tube is prone to absorb dust, oil and other impurities. You can use a neutral detergent and a soft cloth to wipe it to remove surface dirt;
Internal unblocking: Critical pipelines such as hydraulic pipes are easily blocked by impurities in the medium.
Environmental control: Create a good "living environment" for mechanical pipes to avoid close contact with corrosive substances such as acids and alkalis.
2. Regular lubrication: reduce friction loss
Lubricant selection: According to the type of pipeline, choose lubricants such as engine oil and gear oil reasonably, focus on the lubrication of moving parts and connection points, reduce friction between parts, and make the mechanical pipe run more smoothly.
Seal maintenance: carefully check whether the seal is aging and replace the problematic seal in time.
Dynamic monitoring: After lubrication, closely observe the operation status of the pipeline and pay attention to whether there is any abnormal vibration or noise.
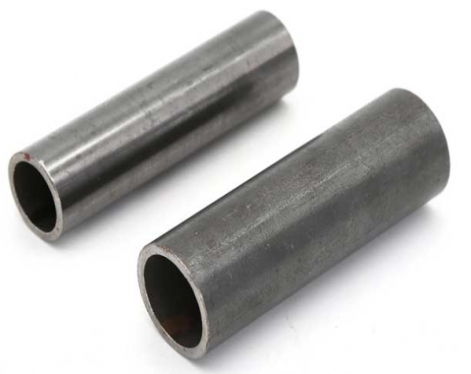
3. Key inspection: Prevent problems before they happen
Appearance inspection: Regularly conduct "physical inspections" on mechanical pipes, focusing on welds and elbows to check for cracks, deformation or leakage.
Pressure test: For high-pressure pipes, water pressure or air pressure tests should be performed regularly to ensure that their pressure-bearing capacity meets the standards.
Sealing test: Apply soapy water to the interface and observe carefully whether there are bubbles to determine whether there is a leak.
4. Scientific operation: avoid maintenance misunderstandings
Avoid excessive maintenance: When a mechanical tube has a minor fault, repair it first rather than blindly replacing parts.
Avoid ignoring the fit clearance: For precision parts such as plunger pumps, assemble them strictly according to the standards to ensure that the fit clearance meets the requirements.
Avoid not checking the travel allowance: Regularly check the travel allowance of moving parts to avoid insufficient travel due to excessive wear, which may cause equipment failure.
Practical tips to extend the life of mechanical tubes
1. Moisture-proof and anti-corrosion: Moisture and corrosive substances are the enemies of mechanical pipes and will accelerate the corrosion of pipes. Before the rainy season comes, apply a layer of anti-rust paint to the mechanical pipes to effectively isolate moisture and air and slow down the rust rate; During storage, raise the bottom of the mechanical pipe by more than 10 cm to avoid direct contact with the ground and reduce the risk of moisture.
2. Prevent vibration damage: Vibration can loosen the internal structure of the mechanical tube and reduce its strength.
3. Repair defects promptly: Once the zinc layer on the surface of the mechanical tube is found to be falling off or local oxidation occurs, it should be immediately treated with special repair paint. Repairing these minor problems promptly can prevent them from further deteriorating and extend the service life of the mechanical tube.
Conclusion
The maintenance of mechanical pipes needs to be combined with cleaning, lubrication, inspection and scientific operation. Preventive maintenance can extend the service life and reduce the risk of sudden failures. The selection of professional tools and standardized processes is the core to ensure the efficient and stable operation of equipment. Cleaning in place to avoid hidden dangers, lubrication in time to reduce wear, regular inspections to detect early, and scientific operations to ensure safety.
Read more: Advantages and Disadvantages of Mechanical Tubes