1. Flexibility of molding system
The roller is an important part of the ERW pipe equipment and the most important tool in the forming process. However, due to the special requirements of its manufacturing materials and processes, the purchase and use costs are high. How to use as few rolls as possible to complete the forming process (same specifications or different specifications) is the key to reducing equipment investment and improving production efficiency.
Japan's FFX forming system can be said to be a pioneer in simplifying welded pipes. The multi-step bending forming process not only simplifies the forming system, but also it greatly makes up for the disadvantages of high dependence of different specifications of welded pipe products on the roll pass shape.
2. Super row roller
The flexible and adjustable roll arrangement equipment not only makes up for the shortcomings of the large number and high cost of traditional roller forming rolls, but also greatly reduces the deformation and damage to the strip caused by rigid forming, reflecting the characteristics of universal, progressive and flexible.
In the future, roller row technology can also develop in the direction of strengthening the stiffness of the inner roller group and improving the functional scope of the roller row section (lengthening the distance between the roller row sections and replacing more vertical roller frames).
3. Quick roll changing technology
Although flexible forming has great advantages in roll replacement and adjustment, the pass shape of the precision forming, extrusion, and sizing rolls determines the outer diameter of the finished welded pipe, so it must be replaced according to the specifications. When the order specifications are many , the roll change and adjustment time are particularly important during batch hours. Therefore, the roll adjustment and quick replacement system are also important indicators for judging the advanced level of the ERW unit. The machine frame is specially designed so that the rollers and connecting parts automatically move to the replacement position and the rollers disengage.
4. Computer control of molding system
Flexible forming reduces the number of rolls, but also increases the frequency and difficulty of tooling adjustment. As the quality requirements for welded pipe products in the domestic and international markets continue to increase, there are also higher requirements for the adjustment accuracy of equipment in production.
The major international ERW pipe forming equipment suppliers have their own control systems, which use high-precision linear sensors to accurately measure and regulate the roll position. Modern molding systems at least require a memory function, that is, to store the product specifications and parameters after passing the production, so that they can be used again, saving a lot of adjustment time.
The future ERW welded pipe forming system can also have intelligent analysis functions to comprehensively uate complex and changeable production factors, select the optimal solution and issue action instructions at the same time. The development of advanced forming control systems is also one of the breakthroughs in the development of my country's welded pipe technology.
The roller is an important part of the ERW pipe equipment and the most important tool in the forming process. However, due to the special requirements of its manufacturing materials and processes, the purchase and use costs are high. How to use as few rolls as possible to complete the forming process (same specifications or different specifications) is the key to reducing equipment investment and improving production efficiency.
Japan's FFX forming system can be said to be a pioneer in simplifying welded pipes. The multi-step bending forming process not only simplifies the forming system, but also it greatly makes up for the disadvantages of high dependence of different specifications of welded pipe products on the roll pass shape.
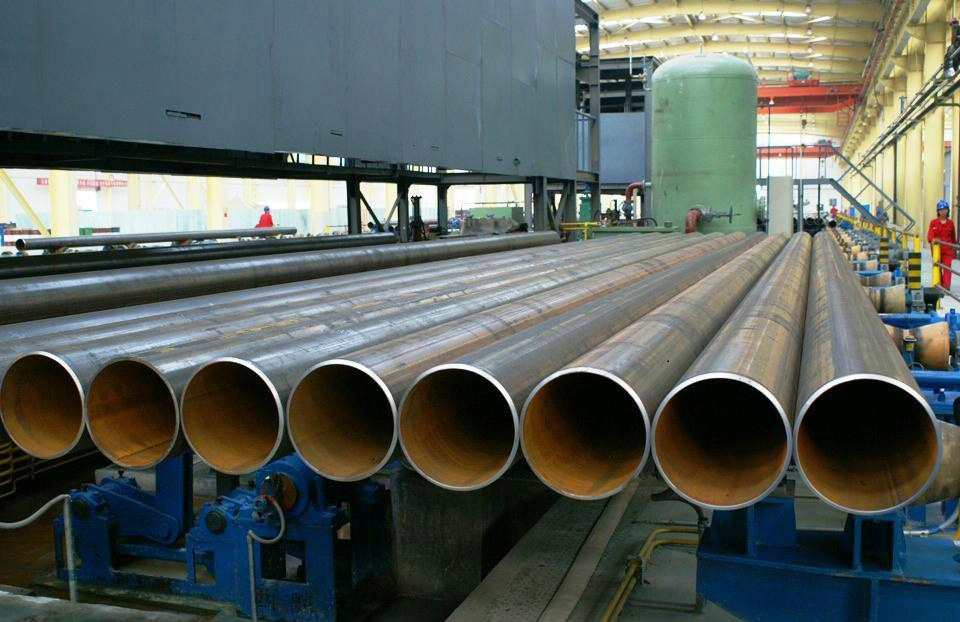
The flexible and adjustable roll arrangement equipment not only makes up for the shortcomings of the large number and high cost of traditional roller forming rolls, but also greatly reduces the deformation and damage to the strip caused by rigid forming, reflecting the characteristics of universal, progressive and flexible.
In the future, roller row technology can also develop in the direction of strengthening the stiffness of the inner roller group and improving the functional scope of the roller row section (lengthening the distance between the roller row sections and replacing more vertical roller frames).
3. Quick roll changing technology
Although flexible forming has great advantages in roll replacement and adjustment, the pass shape of the precision forming, extrusion, and sizing rolls determines the outer diameter of the finished welded pipe, so it must be replaced according to the specifications. When the order specifications are many , the roll change and adjustment time are particularly important during batch hours. Therefore, the roll adjustment and quick replacement system are also important indicators for judging the advanced level of the ERW unit. The machine frame is specially designed so that the rollers and connecting parts automatically move to the replacement position and the rollers disengage.
4. Computer control of molding system
Flexible forming reduces the number of rolls, but also increases the frequency and difficulty of tooling adjustment. As the quality requirements for welded pipe products in the domestic and international markets continue to increase, there are also higher requirements for the adjustment accuracy of equipment in production.
The major international ERW pipe forming equipment suppliers have their own control systems, which use high-precision linear sensors to accurately measure and regulate the roll position. Modern molding systems at least require a memory function, that is, to store the product specifications and parameters after passing the production, so that they can be used again, saving a lot of adjustment time.
The future ERW welded pipe forming system can also have intelligent analysis functions to comprehensively uate complex and changeable production factors, select the optimal solution and issue action instructions at the same time. The development of advanced forming control systems is also one of the breakthroughs in the development of my country's welded pipe technology.