ERW pipe, namely Electric Resistance Welding Pipe, is abbreviated as ERW. It is welded by steel plates, and the weld is formed by melting the base material of the steel strip body, which makes its mechanical strength better than that of ordinary welded pipes. Compared with seamless steel pipes, the most obvious difference of erw pipes is the weld seam, which is also the key to its quality. However, in the production process of erw pipes, welding defects are the key issue affecting their quality and performance. Welding defects may not only lead to safety hazards such as pipeline leakage and reduced structural strength, but also increase production and maintenance costs. Therefore, in-depth understanding of the common defects and preventive measures of erw pipe welding is of great significance to improving the quality and reliability of erw pipes.
Advantages of erw welding process
Common defects of erw pipe welding
1. Lack of fusion: Lack of fusion is one of the more serious defects in erw pipe welding, which can be divided into complete lack of fusion, partial lack of fusion and incomplete fusion (mainly cold welding). This defect occurs mainly because the welding heat input is insufficient and the edge of the strip is not heated to a sufficient temperature; excessive or small deformation of the edge of the strip, the presence of a crescent bend and rust, etc., can also lead to incomplete fusion.
2. Undercut: Undercut is a depression or groove in the parent material along the toe of the weld. This is mainly because the arc heat is too high during welding, that is, the current is too large and the wire feeding speed is too slow, so that after the arc melts the base material at the edge of the weld, it is not fully supplemented by the deposited metal.
3. Weld nodules: Weld nodules are excess metal nodules formed on the surface of the weld when liquid metal flows outside the weld during the welding process. Excessive welding specifications, rapid melting of welding rods, poor welding rod quality (such as eccentricity), unstable welding power supply characteristics and improper operating posture are all likely to cause weld nodules, which are more likely to occur when welding in horizontal, vertical or overhead positions.
Prevention strategies
3. Improving operator skills: The skill level of the operator directly affects the welding quality. Operators should have a good sense of responsibility and quality awareness. At the same time, operators are regularly assessed on their skills to encourage them to continuously improve their operating levels.
Read more: Application of ERW Pipes in Construction Industry
Advantages of erw welding process
1. High production efficiency: When welding erw pipes, the skin effect and proximity effect generated by high-frequency current make the energy highly concentrated on the edge of the steel strip to be welded, the heating speed is extremely fast, and the welding speed is also very high.
2. Lower cost: The welding of erw pipe is pressure welding, which does not require filler metal, reducing the cost of filler materials. At the same time, its production process is relatively simple, the equipment investment is small, and the production efficiency is high. The output per unit time is large, and the production cost allocated to each pipe is reduced. While ensuring product quality, it saves a lot of costs for the company.
3. Easy to automate: From the high-frequency welding machine converting ordinary AC into high-frequency current to the welded pipe forming machine extruding the molten part through the extrusion roller frame, the entire welding process has clear steps and parameters. Accurately control the welding process according to the preset program, reduce manpower input, reduce labor costs, improve production stability, and reduce the impact of human factors on product quality.
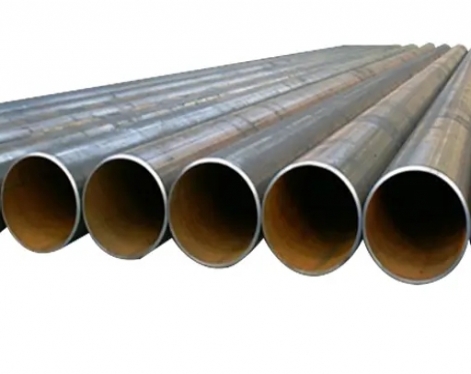
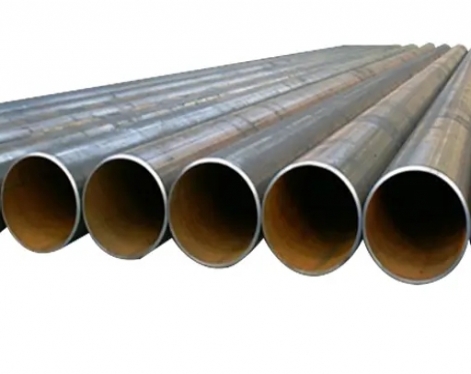
Common defects of erw pipe welding
1. Lack of fusion: Lack of fusion is one of the more serious defects in erw pipe welding, which can be divided into complete lack of fusion, partial lack of fusion and incomplete fusion (mainly cold welding). This defect occurs mainly because the welding heat input is insufficient and the edge of the strip is not heated to a sufficient temperature; excessive or small deformation of the edge of the strip, the presence of a crescent bend and rust, etc., can also lead to incomplete fusion.
2. Undercut: Undercut is a depression or groove in the parent material along the toe of the weld. This is mainly because the arc heat is too high during welding, that is, the current is too large and the wire feeding speed is too slow, so that after the arc melts the base material at the edge of the weld, it is not fully supplemented by the deposited metal.
3. Weld nodules: Weld nodules are excess metal nodules formed on the surface of the weld when liquid metal flows outside the weld during the welding process. Excessive welding specifications, rapid melting of welding rods, poor welding rod quality (such as eccentricity), unstable welding power supply characteristics and improper operating posture are all likely to cause weld nodules, which are more likely to occur when welding in horizontal, vertical or overhead positions.
Prevention strategies
1. Optimizing welding process parameters: Welding current, voltage and speed are key parameters that affect welding quality. If the welding current is too high, it is easy to cause defects such as undercut and weld bead; if the current is too low, incomplete fusion may occur.
2. Control raw material quality: The quality of raw materials is the basis for ensuring welding quality. The condition of the strip edge has a great influence on the welding quality. The edge should be flat, free of cracks and rust. At the same time, the chemical composition and mechanical properties of the strip steel must be controlled to ensure that they meet the relevant standard requirements.3. Improving operator skills: The skill level of the operator directly affects the welding quality. Operators should have a good sense of responsibility and quality awareness. At the same time, operators are regularly assessed on their skills to encourage them to continuously improve their operating levels.
Read more: Application of ERW Pipes in Construction Industry