Differences in production processes
The production process of mechanical tubes can be called "technical flow". It usually adopts rolling and stretching forming processes, and strictly controls the selection of materials from the beginning, using high-quality carbon steel or alloy steel materials to ensure the basic performance of the steel tube. At high temperature, the steel billet is heated until it is sufficiently softened, and then enters the piercing machine to be pierced and elongated to form a seamless tube. The mechanical properties and surface quality of the tube are then further improved through processes such as pickling, cold drawing, and cold rolling.
Ordinary steel tubes belong to the "conventional school" and are mostly processed by drawing plates, welding and other processes. Taking welded steel pipes as an example, straight strips or rolled strips are often used as raw materials, and are welded by furnace welding, resistance welding or arc welding. The welds are divided into straight seams and spiral seams. This process is relatively simple and direct, but it also buries some "hidden dangers" in its performance.
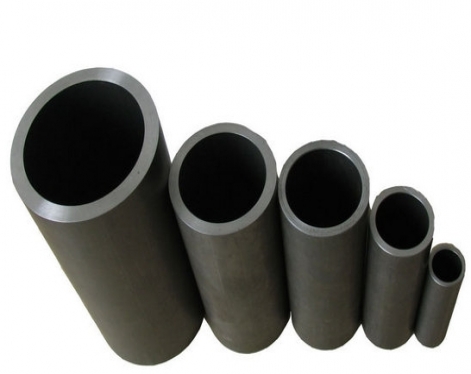
Differences in performance characteristics
1. Pressure resistance and temperature resistance
The pressure resistance and temperature resistance of mechanical tubes are excellent. In some high-pressure environments, such as pipeline transportation in the petrochemical industry, mechanical tubes can withstand pressures of up to tens of megapascals. In high-temperature environments, such as high-temperature furnace pipelines, mechanical tubes can work stably at 500℃ or even higher temperatures without easily deforming or damaging. Ordinary steel tubes can usually only withstand a pressure of several megapascals, and the operating temperature is generally below 200℃. Once this range is exceeded, problems such as leakage and deformation may occur.
2. Torsional strength
Mechanical tubes have extremely high torsional strength due to their sophisticated craftsmanship and high-quality materials. In the manufacture of some mechanical parts that require frequent twisting and bending, mechanical tubes can do a good job and are not prone to breakage or deformation. If ordinary steel tubes want to achieve similar torsional strength, they often need to increase their own models and increase the proportion of internal steel. However, this will not only greatly increase the weight, but also bring inconvenience to installation and use, and the cost will also increase significantly.
3. Surface and internal quality
The inner surface of the mechanical tube is very smooth, the wall thickness is uniform, and the error is very small, which can effectively reduce the resistance during fluid transportation and improve the transportation efficiency. Due to the limitations of welding technology, ordinary steel tubes are prone to roughness and unevenness at the welding point, and there may also be defects such as skewed welds and pores. These not only affect the appearance, but may also become the weak point of the pipeline, reducing the overall performance and service life of the pipeline.
Different application areas
Mechanical tubes are used extensively in the fields of petroleum, chemical industry, aviation manufacturing, etc. due to their outstanding performance. In the oil and gas industry, mechanical tubes are used as oil well casings, gas pipelines, etc. and must withstand high pressure and high temperature; the chemical industry's reactors and heat exchanger pipelines also rely on the stable and reliable performance of mechanical steel pipes to ensure production safety. In the oil and gas industry, mechanical tubes are used as oil well casings, gas pipelines, etc. and must withstand high pressure and high temperature; the chemical industry's reactors and heat exchanger pipelines also rely on the stable and reliable performance of mechanical steel pipes to ensure production safety. The aerospace field has extremely high requirements for material performance. Mechanical tubes are often used to manufacture key parts such as aircraft landing gear and engine components, providing solid protection for flight safety.
Ordinary steel tubes are more widely used in fields with relatively low performance requirements such as construction, bridges, water and water supply and drainage. In construction, ordinary steel tubes are often used to build scaffolding to provide a safe working platform for construction workers; in urban water supply and drainage systems, ordinary steel tubes are responsible for transporting domestic water and discharging sewage.
How to choose: The best one is the one that suits you best
In practical applications, how to choose between mechanical tubes and ordinary steel tubes? This depends on specific needs. If the working environment has high pressure, high temperature, and complex forces, mechanical tubes are the best choice; if the pressure and temperature requirements are not high, such as building simple building structures and general water supply and drainage pipes, ordinary steel tubes can meet the needs and save costs. In short, the most suitable one is the best. When choosing, you must combine the actual situation and comprehensively consider the performance, cost and other factors of the steel tube, so that you can choose the steel tube product that best meets your needs.
Read more: Advantages and Disadvantages of Mechanical Tubes
The production process of mechanical tubes can be called "technical flow". It usually adopts rolling and stretching forming processes, and strictly controls the selection of materials from the beginning, using high-quality carbon steel or alloy steel materials to ensure the basic performance of the steel tube. At high temperature, the steel billet is heated until it is sufficiently softened, and then enters the piercing machine to be pierced and elongated to form a seamless tube. The mechanical properties and surface quality of the tube are then further improved through processes such as pickling, cold drawing, and cold rolling.
Ordinary steel tubes belong to the "conventional school" and are mostly processed by drawing plates, welding and other processes. Taking welded steel pipes as an example, straight strips or rolled strips are often used as raw materials, and are welded by furnace welding, resistance welding or arc welding. The welds are divided into straight seams and spiral seams. This process is relatively simple and direct, but it also buries some "hidden dangers" in its performance.
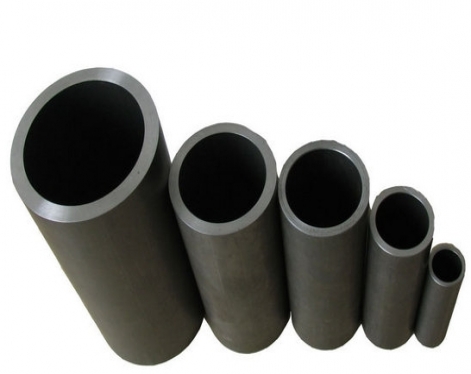
Differences in performance characteristics
1. Pressure resistance and temperature resistance
The pressure resistance and temperature resistance of mechanical tubes are excellent. In some high-pressure environments, such as pipeline transportation in the petrochemical industry, mechanical tubes can withstand pressures of up to tens of megapascals. In high-temperature environments, such as high-temperature furnace pipelines, mechanical tubes can work stably at 500℃ or even higher temperatures without easily deforming or damaging. Ordinary steel tubes can usually only withstand a pressure of several megapascals, and the operating temperature is generally below 200℃. Once this range is exceeded, problems such as leakage and deformation may occur.
2. Torsional strength
Mechanical tubes have extremely high torsional strength due to their sophisticated craftsmanship and high-quality materials. In the manufacture of some mechanical parts that require frequent twisting and bending, mechanical tubes can do a good job and are not prone to breakage or deformation. If ordinary steel tubes want to achieve similar torsional strength, they often need to increase their own models and increase the proportion of internal steel. However, this will not only greatly increase the weight, but also bring inconvenience to installation and use, and the cost will also increase significantly.
3. Surface and internal quality
The inner surface of the mechanical tube is very smooth, the wall thickness is uniform, and the error is very small, which can effectively reduce the resistance during fluid transportation and improve the transportation efficiency. Due to the limitations of welding technology, ordinary steel tubes are prone to roughness and unevenness at the welding point, and there may also be defects such as skewed welds and pores. These not only affect the appearance, but may also become the weak point of the pipeline, reducing the overall performance and service life of the pipeline.
Different application areas
Mechanical tubes are used extensively in the fields of petroleum, chemical industry, aviation manufacturing, etc. due to their outstanding performance. In the oil and gas industry, mechanical tubes are used as oil well casings, gas pipelines, etc. and must withstand high pressure and high temperature; the chemical industry's reactors and heat exchanger pipelines also rely on the stable and reliable performance of mechanical steel pipes to ensure production safety. In the oil and gas industry, mechanical tubes are used as oil well casings, gas pipelines, etc. and must withstand high pressure and high temperature; the chemical industry's reactors and heat exchanger pipelines also rely on the stable and reliable performance of mechanical steel pipes to ensure production safety. The aerospace field has extremely high requirements for material performance. Mechanical tubes are often used to manufacture key parts such as aircraft landing gear and engine components, providing solid protection for flight safety.
Ordinary steel tubes are more widely used in fields with relatively low performance requirements such as construction, bridges, water and water supply and drainage. In construction, ordinary steel tubes are often used to build scaffolding to provide a safe working platform for construction workers; in urban water supply and drainage systems, ordinary steel tubes are responsible for transporting domestic water and discharging sewage.
How to choose: The best one is the one that suits you best
In practical applications, how to choose between mechanical tubes and ordinary steel tubes? This depends on specific needs. If the working environment has high pressure, high temperature, and complex forces, mechanical tubes are the best choice; if the pressure and temperature requirements are not high, such as building simple building structures and general water supply and drainage pipes, ordinary steel tubes can meet the needs and save costs. In short, the most suitable one is the best. When choosing, you must combine the actual situation and comprehensively consider the performance, cost and other factors of the steel tube, so that you can choose the steel tube product that best meets your needs.
Read more: Advantages and Disadvantages of Mechanical Tubes