Excess weld metal refers to the height of the metal on the line connecting the two toes on the surface of the weld. There should be excess weld metal in the welding process of the welded pipe. Because it plays the role of the last layer of heat preservation and slow cooling, it plays a great role in refining grains and reducing welding stress. It is also a collection area for inclusions such as pores.
However, whether it is LSAW steel pipe or SSAW steel pipe, if the excess weld metal is too large and it is not a smooth transition, the stress concentration factor at the weld toe of the weld is large.
In addition, if the outer excess weld metal is too large, it will increase the anti-corrosion difficulty of the steel pipe; if the inner excess weld metal is too large, it will increase the frictional resistance of the pipeline and increase the energy consumption. Therefore, the excess weld metal must be controlled.
Harm of excess weld metal
1.Stress corrosion cracks are easily formed at the weld toe
The larger the residual height of the weld, the more serious the stress concentration, and the lower the strength of the welded joint. After welding, trimming the remaining height, as long as it is not lower than the base metal, reduces the stress concentration, and sometimes can improve the strength of the welded joint.
2.The outer excess weld metal is large, which is not conducive to anti-corrosion
When the steel pipe is used, if the epoxy resin glass cloth is used for anti-corrosion, the outer excess weld metal will be large, which will make the weld toe difficult to press firmly. At the same time, the higher the weld, the thicker the anti-corrosion layer should be. Because the standard stipulates that the thickness of the anti-corrosion layer is measured based on the apex of the outer weld, which increases the cost of anti-corrosion.
3.The outer excess weld metal is large, which affects the tube shape after hydraulic expansion.
When the LSAW steel pipe is expanded by water pressure, the steel pipe is wrapped by the left and right two parts of the outer mold whose inner cavity is the same as the diameter of the steel pipe. Therefore, if the excess height of the weld is too large, the shear stress on the weld will be large when the diameter is expanded, and the phenomenon of "small straight edges" will easily appear on both sides of the weld.
4.The internal excess weld metal is large, which increases the energy loss of the conveying medium
If the inner surface of the submerged arc welded pipe for conveying is not coated with anti-corrosion treatment, the residual height of the inner weld will be large, and the frictional resistance to the conveying medium will also be large, which will increase the energy consumption of the conveying pipeline.
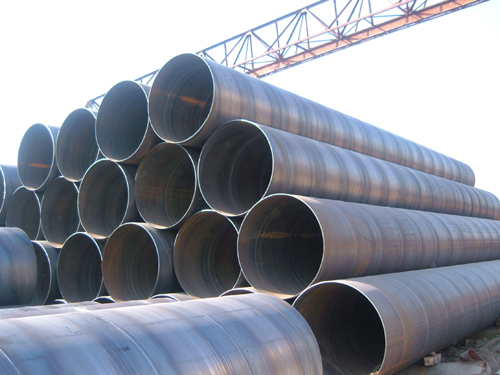
Control measures for excess weld metal
1.Steel pipes with larger wall thicknesses should be beveled
For steel pipes with wall thickness greater than 14.3mm, X-shaped grooves should be opened and pre-welded. If the pre-welding conditions are not mature, the root should be cleaned by air gouging after internal welding, or by automatic grinding with grinding wheel, or by milling and other methods, and the outer weld should be processed into a U-shaped groove before welding before welding.
2.Adjust the welding line energy
To check whether the welding line energy is suitable, generally use the acid etching sample of the welded joint to check. One is to check the degree of overlap of the inner and outer welds, and the other is to check the width of the waist of the weld bead.The line energy is large, not only the penetration depth is large, but also the excess weld metal is large. If the groove or U-shaped groove is not opened, the excess weld metal will be larger. This is because the greater the welding line energy, the more welding wire melted per unit time. For high-strength steel, the welding line energy should be strictly controlled. When welding high-strength steel plates, in order to reduce the line energy of each layer, multi-pass welding (more than 2 passes) is generally used, and the shape factor of the weld should be within 1.3-2.0 mm.
3.Thinner front wire should be used in multi-wire welding
When multi-wire welding is adopted, if the matching diameter of the original external welding three wires is 4mm+3.2mm+3.2mm (DC-AC-AC), it is better to change the front wire to Ф3.2mm. Because in the case of using the same current, the penetration depth of the wire with Ф3.2mm is larger than that of the wire with Ф4mm. That is to say, if the front wire adopts Ф3.2mm welding wire, even if the line energy is reduced, the same penetration effect can be achieved when using Ф4mm, which is due to the fact that the current density of the thin wire is higher than that of the thick wire.
4.Spiral welding must adjust the position of the inner and outer welding heads
When the spiral submerged arc welded pipe is internally welded, the position of the internal welding head should be adjusted to minimize or eliminate the "saddle-shaped" internal welding seam;During external welding, the spatial position of the welding head should also be adjusted to minimize or eliminate the "fish-back-shaped" external weld, which is mainly achieved by adjusting the eccentric value of the external welding spot. Different calibers of spiral welded pipes have different eccentric values of the outer welded joints.
However, whether it is LSAW steel pipe or SSAW steel pipe, if the excess weld metal is too large and it is not a smooth transition, the stress concentration factor at the weld toe of the weld is large.
In addition, if the outer excess weld metal is too large, it will increase the anti-corrosion difficulty of the steel pipe; if the inner excess weld metal is too large, it will increase the frictional resistance of the pipeline and increase the energy consumption. Therefore, the excess weld metal must be controlled.
Harm of excess weld metal
1.Stress corrosion cracks are easily formed at the weld toe
The larger the residual height of the weld, the more serious the stress concentration, and the lower the strength of the welded joint. After welding, trimming the remaining height, as long as it is not lower than the base metal, reduces the stress concentration, and sometimes can improve the strength of the welded joint.
2.The outer excess weld metal is large, which is not conducive to anti-corrosion
When the steel pipe is used, if the epoxy resin glass cloth is used for anti-corrosion, the outer excess weld metal will be large, which will make the weld toe difficult to press firmly. At the same time, the higher the weld, the thicker the anti-corrosion layer should be. Because the standard stipulates that the thickness of the anti-corrosion layer is measured based on the apex of the outer weld, which increases the cost of anti-corrosion.
3.The outer excess weld metal is large, which affects the tube shape after hydraulic expansion.
When the LSAW steel pipe is expanded by water pressure, the steel pipe is wrapped by the left and right two parts of the outer mold whose inner cavity is the same as the diameter of the steel pipe. Therefore, if the excess height of the weld is too large, the shear stress on the weld will be large when the diameter is expanded, and the phenomenon of "small straight edges" will easily appear on both sides of the weld.
4.The internal excess weld metal is large, which increases the energy loss of the conveying medium
If the inner surface of the submerged arc welded pipe for conveying is not coated with anti-corrosion treatment, the residual height of the inner weld will be large, and the frictional resistance to the conveying medium will also be large, which will increase the energy consumption of the conveying pipeline.
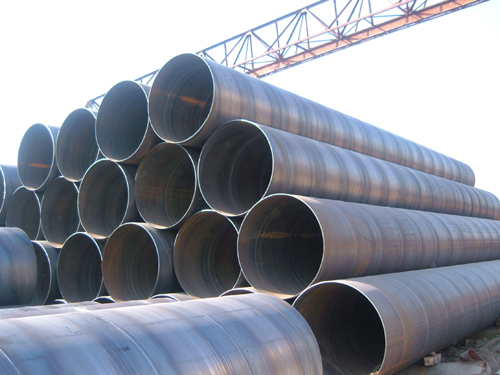
Control measures for excess weld metal
1.Steel pipes with larger wall thicknesses should be beveled
For steel pipes with wall thickness greater than 14.3mm, X-shaped grooves should be opened and pre-welded. If the pre-welding conditions are not mature, the root should be cleaned by air gouging after internal welding, or by automatic grinding with grinding wheel, or by milling and other methods, and the outer weld should be processed into a U-shaped groove before welding before welding.
2.Adjust the welding line energy
To check whether the welding line energy is suitable, generally use the acid etching sample of the welded joint to check. One is to check the degree of overlap of the inner and outer welds, and the other is to check the width of the waist of the weld bead.The line energy is large, not only the penetration depth is large, but also the excess weld metal is large. If the groove or U-shaped groove is not opened, the excess weld metal will be larger. This is because the greater the welding line energy, the more welding wire melted per unit time. For high-strength steel, the welding line energy should be strictly controlled. When welding high-strength steel plates, in order to reduce the line energy of each layer, multi-pass welding (more than 2 passes) is generally used, and the shape factor of the weld should be within 1.3-2.0 mm.
3.Thinner front wire should be used in multi-wire welding
When multi-wire welding is adopted, if the matching diameter of the original external welding three wires is 4mm+3.2mm+3.2mm (DC-AC-AC), it is better to change the front wire to Ф3.2mm. Because in the case of using the same current, the penetration depth of the wire with Ф3.2mm is larger than that of the wire with Ф4mm. That is to say, if the front wire adopts Ф3.2mm welding wire, even if the line energy is reduced, the same penetration effect can be achieved when using Ф4mm, which is due to the fact that the current density of the thin wire is higher than that of the thick wire.
4.Spiral welding must adjust the position of the inner and outer welding heads
When the spiral submerged arc welded pipe is internally welded, the position of the internal welding head should be adjusted to minimize or eliminate the "saddle-shaped" internal welding seam;During external welding, the spatial position of the welding head should also be adjusted to minimize or eliminate the "fish-back-shaped" external weld, which is mainly achieved by adjusting the eccentric value of the external welding spot. Different calibers of spiral welded pipes have different eccentric values of the outer welded joints.