Cracking is one of the common defects of seamless steel pipe. When the seamless steel pipe is quenched, it will also cause cracking of the seamless steel pipe due to improper handling.
The quenching process is mainly used for steel parts, which is to heat the steel to a temperature above the critical temperature Ac3 (hypo-eutectoid steel) or Ac1 (hyper-eutectoid steel), and keep it for a period of time to make it fully or partially austenitized.Then the heat treatment process of martensite (or bainite) transformation is carried out by cooling rapidly below Ms (martensitic transformation initiation temperature) (or isothermal near Ms) at a cooling rate greater than the critical cooling rate.Quenching cracks refer to cracks generated during the quenching process or at room temperature after quenching, and the latter is also called aging cracks.
Cause of cracks
Melt-fire cracking mainly occurs in the later stage of melt-fire cooling, that is, after the martensitic transformation is basically completed or completely cooled, at this time, the plasticity of the steel pipe is very poor and the strength is high.When the internal stress exceeds the tensile strength of the material, cracks will occur, or even complete fractures. If the steel pipe is only deformed after the fire is dissolved, it can still be corrected, but if it is dissolved, it will become a waste product. There are many reasons for melt fire cracking. The fundamental reason is that the tensile stress exceeds the tensile strength of the material, and the crack is usually perpendicular to the direction of the maximum tensile stress.
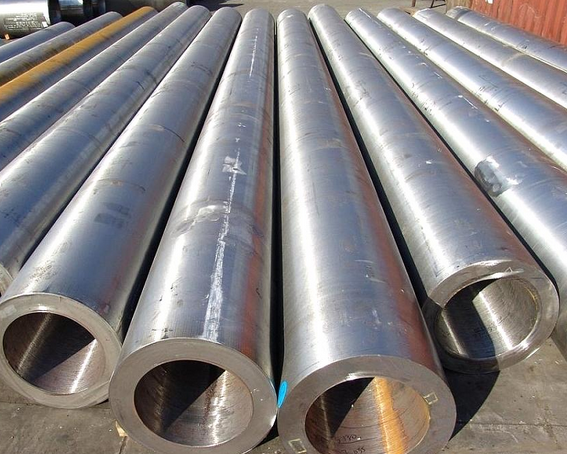
Methods to prevent cracking
(1) Try to achieve uniform heating and correct heating
Sometimes steel pipes are deformed due to uneven heating. For this reason, before the steel pipe is installed in the furnace, the holes that do not need to be hardened and the sudden change of the cross-section should be blocked or tied with asbestos ropes to improve the heating conditions, which is conducive to uniform heating and uniform cooling.
When the steel pipe is heated in the furnace, it should be placed evenly to prevent heating on one side, and it should be laid flat to avoid deformation of the steel pipe due to its own weight in the high-temperature plastic state.
Limiting or reducing the heating rate can reduce the temperature difference of the steel pipe section and make the heating uniform. Reasonable selection of quenching heating temperature is also the key to reducing or preventing deformation and cracking. Selecting the lower limit quenching temperature and reducing the temperature difference between the steel pipe and the quenching medium can reduce the cooling rate in the high temperature stage of quenching and cooling, thereby reducing the thermal stress during quenching and cooling. In addition, coarsening of crystal grains can also be prevented. This prevents deformation and cracking. Sometimes in order to adjust the volume deformation before and after quenching, the quenching heating temperature can also be appropriately increased.
(2) Basic principles for correct selection of cooling method and cooling medium
Pre-cooling should be used as much as possible, that is, before the steel pipe is quenched into the quenching medium, it should be cooled to the vicinity of Ar as slowly as possible to reduce the temperature difference in the steel pipe. Under the premise of ensuring that the depth and hardness of the hardened layer are met, the quenching medium that cools and slows the steamed steamer is used as much as possible. Reasonable selection and adoption of graded or isothermal quenching process.
(3) The basic principle of correctly selecting the way and running direction of the quenched steel pipe immersed in the quenching medium
When quenching, try to ensure the most uniform cooling. Quenching in the direction of least resistance.
Carry out timely and correct tempering. Some steel pipes are not cracked during quenching, but cracked because they are not tempered in time after quenching. This is because during the quenching stay, the fine cracks existing in the steel pipe are fused and expanded under the action of a large quenching stress, so that their size reaches the critical crack size for fracture, resulting in delayed fracture.
The distortion of the steel pipe can be corrected by straightening, but it must be within the allowable range of the plasticity of the steel pipe. Sometimes it can also be calibrated with a specific calibration jig during tempering heating. Deformation of the quenched volume is often unavoidable. However, as long as the deformation law is mastered through experiments, according to the amount of expansion and contraction, it can be properly corrected during forming and processing before quenching, and then the required geometric dimensions can be obtained after quenching. Once the steel pipe has quenching cracks, it will be scrapped.
The quenching process is mainly used for steel parts, which is to heat the steel to a temperature above the critical temperature Ac3 (hypo-eutectoid steel) or Ac1 (hyper-eutectoid steel), and keep it for a period of time to make it fully or partially austenitized.Then the heat treatment process of martensite (or bainite) transformation is carried out by cooling rapidly below Ms (martensitic transformation initiation temperature) (or isothermal near Ms) at a cooling rate greater than the critical cooling rate.Quenching cracks refer to cracks generated during the quenching process or at room temperature after quenching, and the latter is also called aging cracks.
Cause of cracks
Melt-fire cracking mainly occurs in the later stage of melt-fire cooling, that is, after the martensitic transformation is basically completed or completely cooled, at this time, the plasticity of the steel pipe is very poor and the strength is high.When the internal stress exceeds the tensile strength of the material, cracks will occur, or even complete fractures. If the steel pipe is only deformed after the fire is dissolved, it can still be corrected, but if it is dissolved, it will become a waste product. There are many reasons for melt fire cracking. The fundamental reason is that the tensile stress exceeds the tensile strength of the material, and the crack is usually perpendicular to the direction of the maximum tensile stress.
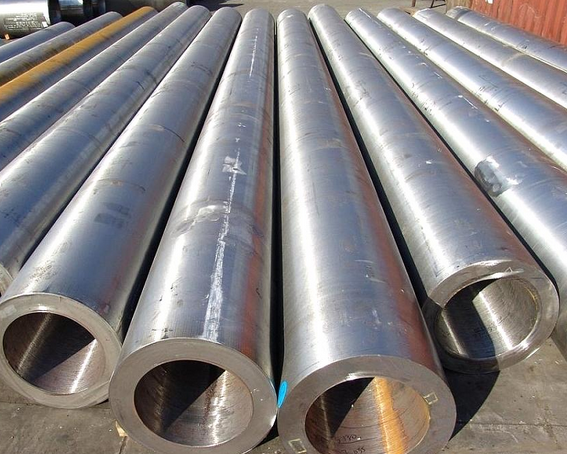
Methods to prevent cracking
(1) Try to achieve uniform heating and correct heating
Sometimes steel pipes are deformed due to uneven heating. For this reason, before the steel pipe is installed in the furnace, the holes that do not need to be hardened and the sudden change of the cross-section should be blocked or tied with asbestos ropes to improve the heating conditions, which is conducive to uniform heating and uniform cooling.
When the steel pipe is heated in the furnace, it should be placed evenly to prevent heating on one side, and it should be laid flat to avoid deformation of the steel pipe due to its own weight in the high-temperature plastic state.
Limiting or reducing the heating rate can reduce the temperature difference of the steel pipe section and make the heating uniform. Reasonable selection of quenching heating temperature is also the key to reducing or preventing deformation and cracking. Selecting the lower limit quenching temperature and reducing the temperature difference between the steel pipe and the quenching medium can reduce the cooling rate in the high temperature stage of quenching and cooling, thereby reducing the thermal stress during quenching and cooling. In addition, coarsening of crystal grains can also be prevented. This prevents deformation and cracking. Sometimes in order to adjust the volume deformation before and after quenching, the quenching heating temperature can also be appropriately increased.
(2) Basic principles for correct selection of cooling method and cooling medium
Pre-cooling should be used as much as possible, that is, before the steel pipe is quenched into the quenching medium, it should be cooled to the vicinity of Ar as slowly as possible to reduce the temperature difference in the steel pipe. Under the premise of ensuring that the depth and hardness of the hardened layer are met, the quenching medium that cools and slows the steamed steamer is used as much as possible. Reasonable selection and adoption of graded or isothermal quenching process.
(3) The basic principle of correctly selecting the way and running direction of the quenched steel pipe immersed in the quenching medium
When quenching, try to ensure the most uniform cooling. Quenching in the direction of least resistance.
Carry out timely and correct tempering. Some steel pipes are not cracked during quenching, but cracked because they are not tempered in time after quenching. This is because during the quenching stay, the fine cracks existing in the steel pipe are fused and expanded under the action of a large quenching stress, so that their size reaches the critical crack size for fracture, resulting in delayed fracture.
The distortion of the steel pipe can be corrected by straightening, but it must be within the allowable range of the plasticity of the steel pipe. Sometimes it can also be calibrated with a specific calibration jig during tempering heating. Deformation of the quenched volume is often unavoidable. However, as long as the deformation law is mastered through experiments, according to the amount of expansion and contraction, it can be properly corrected during forming and processing before quenching, and then the required geometric dimensions can be obtained after quenching. Once the steel pipe has quenching cracks, it will be scrapped.