H beam is an important structural steel, widely used in construction, machinery manufacturing, ships,bridges and other fields.When producing High-Frequency Welded(HFW) H-shaped steel, there are many factors that affect its quality, and these factors interact with each other, affecting the whole body.
Welding process is the key to welding quality. For welding H-shaped steel, the appropriate welding method should be selected according to the material and requirements of the steel, such as manual arc welding, submerged arc welding or gas shielded welding. Before welding, the welds and steel should be derusted and cleaned to ensure welding quality. Before welding, the appropriate welding current and voltage should be adjusted according to the type of welding material and the size of the welding pipe to ensure the welding effect.
After welding is completed, quality inspection should be carried out to ensure the quality of welded H-shaped steel. Commonly used welding quality inspection methods include visual inspection, dimensional inspection, mechanical property testing of welded joints and non-destructive testing. Through these inspections, the density, welding strength and appearance quality of the weld can be uated.
Visual inspection is the most basic welding quality inspection method. It mainly checks whether the weld is complete, the appearance of the weld is smooth, and there are no pores, slag inclusions, cracks and other defects. Dimensional inspection is mainly to check whether the size of the welding part meets the design requirements, including the width, height, length and other dimensional parameters of the weld.
In short, the quality requirements for welded H-shaped steel production involve the selection of welding materials, the control of welding processes and the implementation of welding quality inspection. Only when these requirements are strictly followed can welding H-shaped steel ensure the stability and safety of its structure.
1.Factors affecting HFW of H section
(1) Frequency
During production, the frequency of high-frequency welding affects the current distribution inside the high-frequency welded H-shaped steel. The frequency also affects the width of the heat-affected zone of the weld. If a higher frequency is used, the efficiency can be improved.(2) Meeting angle
If the meeting angle is small, the speed of high-frequency welding will be accelerated, but if it is too small, deep pits and small holes will easily occur, making it difficult to press. If it is too large, the efficiency of the angle will be greatly reduced. Energy consumption will also increase.(3) Welding methods
High-frequency welding is divided into two types: contact welding and induction welding. Contact welding has good current, high efficiency and low power consumption, but large losses and poor stability; induction welding refers to placing one or more turns of induction coils outside the steel pipe to be welded, without loss, smooth surface, and neat welds .(4) Output power
If the power is too small, it will cause problems such as virtual soldering and desoldering; if the power is too high, it will cause problems such as splashing and small holes, which are called burning defects.(5) Pipe blank groove
If an "I"-shaped groove is used, the inner edge layer needs to be removed, which will produce internal burrs and make the central layer and outer layer inaccessible to heat. Weld strength will be affected. Therefore, it is better for the groove to be in an "X" shape.(6) Welding speed
Welding speed affects welding quality. When the welding speed is high, the heat affected zone is shortened; conversely, when the welding speed is low, the heat affected zone becomes larger, larger welding burrs will appear, and the quality of the weld seam becomes worse.(7) Resistor
The resistor matches the pipe diameter to keep the magnetic flux stable. To ensure the magnetic permeability of the resistor, in addition to the material requirements of the resistor, it is also necessary to ensure that the ratio of the cross-sectional area of the resistor to the cross-sectional area of the pipe diameter is large enough.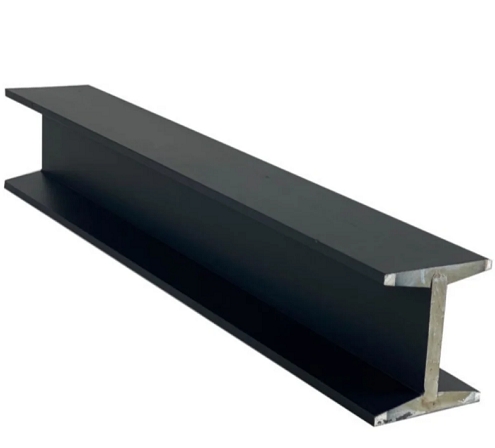
2. Quality requirements for HFW H-shaped steel
During the production process of welded H-shaped steel, a series of quality requirements need to be followed to ensure the strength and stability of the welded structure. The following will introduce the quality requirements for H-beam welding in terms of welding materials, welding processes and welding quality inspection.(1)Welding material requirements
Welding materials are one of the important factors that affect welding quality. When selecting welding materials, the corresponding welding rod or wire should be selected according to the material and requirements of the H-shaped steel to be welded. The strength and plasticity of the welding material should match the H-shaped steel to ensure the strength and reliability of the welded part.
(2)Welding process requirements
Welding process is the key to welding quality. For welding H-shaped steel, the appropriate welding method should be selected according to the material and requirements of the steel, such as manual arc welding, submerged arc welding or gas shielded welding. Before welding, the welds and steel should be derusted and cleaned to ensure welding quality. Before welding, the appropriate welding current and voltage should be adjusted according to the type of welding material and the size of the welding pipe to ensure the welding effect.
(3)Welding quality inspection requirements
After welding is completed, quality inspection should be carried out to ensure the quality of welded H-shaped steel. Commonly used welding quality inspection methods include visual inspection, dimensional inspection, mechanical property testing of welded joints and non-destructive testing. Through these inspections, the density, welding strength and appearance quality of the weld can be uated.Visual inspection is the most basic welding quality inspection method. It mainly checks whether the weld is complete, the appearance of the weld is smooth, and there are no pores, slag inclusions, cracks and other defects. Dimensional inspection is mainly to check whether the size of the welding part meets the design requirements, including the width, height, length and other dimensional parameters of the weld.
In short, the quality requirements for welded H-shaped steel production involve the selection of welding materials, the control of welding processes and the implementation of welding quality inspection. Only when these requirements are strictly followed can welding H-shaped steel ensure the stability and safety of its structure.
Previous:Production Process of H Beams