Seamless steel pipes (smls) are widely used in various fields, and the production process mainly includes forging and casting. The forging process includes blank preparation, heating, forming, etc., and the casting process includes smelting, pouring, etc. Both processes require strict control of parameters such as temperature and chemical composition to ensure the quality and performance of the pipe.
Forging process:
Forging process is an important process in the production of seamless steel pipe, mainly including billet preparation, heating, forming, cooling after forging and finishing.
1. Billet preparation
The billet for forging seamless steel pipe is usually continuous casting billet or rolled billet, and its outer diameter, length and material must meet the process requirements. The quality of the billet directly affects the quality and performance of the final product.
2. Heating
Heating is an important link in the forging process, the purpose of which is to soften the billet and improve the plasticity. The heating temperature and time should be controlled according to the material and process requirements to avoid problems such as oxidation, decarburization, and overburning.
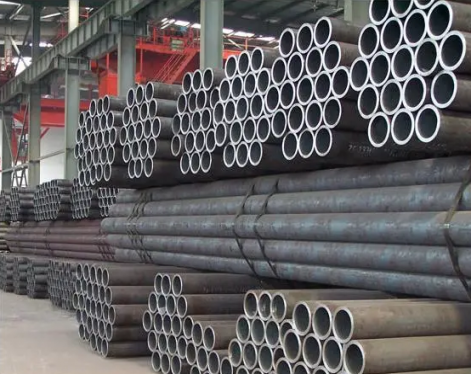
3. Forming
Forming is the process of forming the heated billet into the desired shape by forging or rolling. There are many ways to form seamless steel pipes, such as free forging, die forging, ring rolling, etc. Different forming methods have different requirements for process parameters and equipment, but all of them need to ensure the quality and dimensional accuracy of the inner and outer surfaces of the pipe.
4. Cooling after forging
Cooling after forging is the process of cooling high-temperature forgings to room temperature, the purpose of which is to avoid deformation or cracking caused by excessive internal stress. There are two cooling methods: natural cooling and forced cooling. The specific selection depends on the material and process requirements.
5. Finishing
Finishing is an important process in the production of seamless steel pipes, including straightening, cutting heads and tails, and surface cleaning. Through finishing, the internal stress of the pipe can be eliminated, and the straightness and appearance quality of the pipe can be improved.
Casting process:
Casting process is another production process of seamless steel pipes, which mainly includes smelting, pouring, cooling and blanking.
1. Melting
Smelting is the process of melting metal materials into liquid and adding appropriate amounts of alloying elements to adjust their chemical composition. The quality of the molten metal after smelting directly affects the quality and performance of the cast pipe. During the smelting process, the temperature and chemical composition must be strictly controlled to avoid problems such as oxidation, slag inclusion, and pores.
2. Pouring
Pouring is the process of pouring the molten metal into the mold to form the desired shape of the pipe. During the casting process, the pouring temperature, pouring speed and pouring method must be controlled to ensure the dimensional accuracy and internal quality of the pipe.
3. Cooling
The cooling method of the cast pipe is usually natural cooling or forced cooling. Different cooling methods have a certain impact on the quality and performance of the pipe. During the cooling process, attention should be paid to controlling the cooling speed to avoid problems such as cracks and deformation.
4. Blanking
Open blank is the process of removing the cast pipe from the mold and performing preliminary processing. The open blank process includes peeling, cutting, straightening, etc., the purpose of which is to remove casting defects, adjust the pipe size and improve the quality of the pipe.
Forging process:
Forging process is an important process in the production of seamless steel pipe, mainly including billet preparation, heating, forming, cooling after forging and finishing.
1. Billet preparation
The billet for forging seamless steel pipe is usually continuous casting billet or rolled billet, and its outer diameter, length and material must meet the process requirements. The quality of the billet directly affects the quality and performance of the final product.
2. Heating
Heating is an important link in the forging process, the purpose of which is to soften the billet and improve the plasticity. The heating temperature and time should be controlled according to the material and process requirements to avoid problems such as oxidation, decarburization, and overburning.
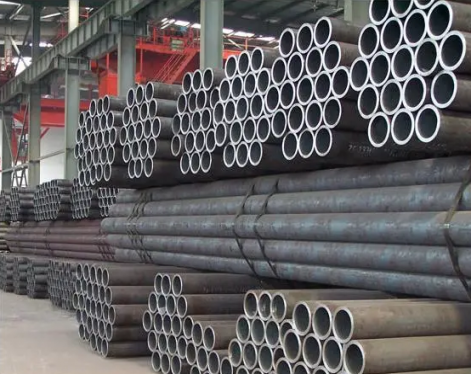
3. Forming
Forming is the process of forming the heated billet into the desired shape by forging or rolling. There are many ways to form seamless steel pipes, such as free forging, die forging, ring rolling, etc. Different forming methods have different requirements for process parameters and equipment, but all of them need to ensure the quality and dimensional accuracy of the inner and outer surfaces of the pipe.
4. Cooling after forging
Cooling after forging is the process of cooling high-temperature forgings to room temperature, the purpose of which is to avoid deformation or cracking caused by excessive internal stress. There are two cooling methods: natural cooling and forced cooling. The specific selection depends on the material and process requirements.
5. Finishing
Finishing is an important process in the production of seamless steel pipes, including straightening, cutting heads and tails, and surface cleaning. Through finishing, the internal stress of the pipe can be eliminated, and the straightness and appearance quality of the pipe can be improved.
Casting process:
Casting process is another production process of seamless steel pipes, which mainly includes smelting, pouring, cooling and blanking.
1. Melting
Smelting is the process of melting metal materials into liquid and adding appropriate amounts of alloying elements to adjust their chemical composition. The quality of the molten metal after smelting directly affects the quality and performance of the cast pipe. During the smelting process, the temperature and chemical composition must be strictly controlled to avoid problems such as oxidation, slag inclusion, and pores.
2. Pouring
Pouring is the process of pouring the molten metal into the mold to form the desired shape of the pipe. During the casting process, the pouring temperature, pouring speed and pouring method must be controlled to ensure the dimensional accuracy and internal quality of the pipe.
3. Cooling
The cooling method of the cast pipe is usually natural cooling or forced cooling. Different cooling methods have a certain impact on the quality and performance of the pipe. During the cooling process, attention should be paid to controlling the cooling speed to avoid problems such as cracks and deformation.
4. Blanking
Open blank is the process of removing the cast pipe from the mold and performing preliminary processing. The open blank process includes peeling, cutting, straightening, etc., the purpose of which is to remove casting defects, adjust the pipe size and improve the quality of the pipe.